Student whisks his way to glory in Siemens Student Design Contest!
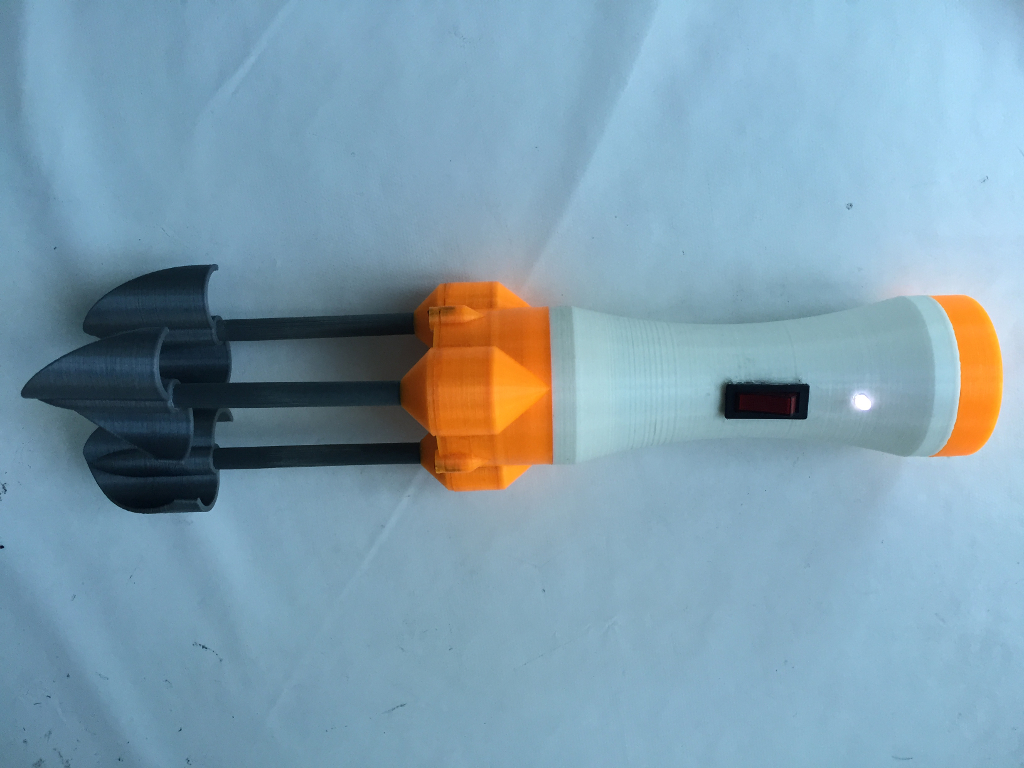
Tom Fothergill is a student at Nottingham Trent University in the UK. Check out this video to see the food whisk that he designed in Solid Edge and then 3D printed.
Here Tom talks us through his designprocess:
I created the electric cooking whisk for a college project that I was doing, I wanted to design and make a product that incorporated electrical and mechanical engineering as this is the degree I will be studying for.
I had some previous knowledge on gear systems and I wanted to incorporate this in to my project. My Mum does a lot cookingand I noticed that an electric whisk uses a gear system, thus I decided to try and make some improvement to the design.
When it came to designing it I looked at existing products on the market and tried to incorporate their best features into my design and the bad features I wanted to improve on. I sketched out lots of different designs that could be manufactured using 3D printing technology and finally decided to incorporate 3 blades. All of the individual pieces had to be designed separately, so that they all fitted together correctly. I designed the shape of the whisk around the electronics that needed to fit inside. All of the electronics were incorporated off a Cordless screw driver (Mac Allister 3.6 v).
I wanted to make the product as ergonomic as possible by addingcontours to the design where required to contain the standard motor/electronics and be sturdy enough for use (given that it is all plastic). The entire whisk took about 58 hours to print. Everything on the design is 3D printed apart from the parts salvaged from the cordless screwdriver and bearings . The product itself works very well at carrying out its function of mixing and stirring foodingredients together. In the video I mixed egg, flour and milk together which it achieved quite well considering this whisk is 3D printed.
I would recommend Solid Edge to other users as it allows novice and professionals alike to produce complex parts/assemblies with a very short learning curve helped by the intuitive way the menu system works . Compared to other engineering CAD software available Solid Edge certainly has the ‘Edge’. As with any 3D design generated with software the real challenge comes when you have to physically manufacture parts from that data. With Solid Edge this was made quite easy using the ‘smart dimension’ command allowing for re-adjustments when 3D printing the parts.
Aside from the regularly used construction features that enabled me to produce the assembly, the integrated feature of KeyShot was invaluable in producing a photo realistic visual render. This feature was also useful in getting a real feel for the finished product throughout the whole design process.
Here is the article from 3dprint.com
Congratulations Tom, a shiny new iPad will be winging its way towards you shortly!
Check out our gallery of other previous winners from around the world.