NHL Stenden uses Teamcenter, NX, and Simcenter to provide students with digitalization skills
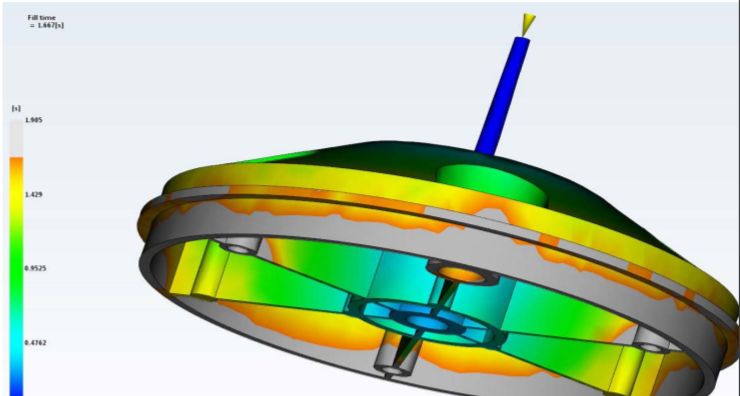
Siemens Digital Industries Software solutions help NHL Stenden prepare students for product development and manufacturing challenges
By: Hannah Straub
Emmen, The Netherlands
The multi-campus NHL Stenden University of Applied Sciences is an internationally recognized institution that awards accredited degrees. Based at Emmen in the northern part of the Netherlands, it has already successfully educated thousands of Dutch and international students with its Dutch and English-language bachelor and master programs in a variety of subject areas. These range from international hospitality management to international teacher education for primary schools to information technology.
Design-based education
The educational concept of the NHL Stenden University of Applied Sciences based in Emmen, the Netherlands, combines an interdisciplinary approach, with real-world assignments to solve. With design-based education (DBE), ideas are turned into practical solutions, often in an international context.

Model-based engineering
The university of applied science is running a center of expertise where students get acquainted with smart production technologies. During their first year at NHL Stenden, mechanical engineering students learn the basics of drawing and modeling. During all phases, NHL Stenden students work with computer-aided engineering (CAE).

Smart production technologies
Using NX for computer-aided manufacturing (CAM), the students learn how to generate programs for numerical control (NC) machines. In their second year, NHL Stenden students design and produce plastic parts as well as the molds needed for their parts’ production on injection molding machines. Once completed, the students store their NC programs electronically to introduce them to NC machine tools, where the components are manufactured using aluminum. “The NC programs are fully associative with the models of both the molds and the parts to produce,” says Gerrit Ottens, tool design and construction lecturer at NHL Stenden. “Using NX for all tasks along the way helps our students to fulfill their future employers’ need for efficiency and to product error-free designs with a short implementation time.”

Product lifecycle management included
What really distinguishes NHL Stenden is that product lifecycle management (PLM) is an integral part of the technical education there. The university of applied science uses Teamcenter software, also from Siemens, to store and manage all product-related information. Working in small teams, each student relies on the completeness and validity digital twin they require to complete their parts of the overall task. Better organization, more efficient product design and faster production preparation are not the only benefits the comprehensive use of Teamcenter provides. “With Teamcenter, students comfortably (re)use existing data and create new designs,” says Dr. Ing Wilbert van den Eijnde, associate lecturer of smart sustainable manufacturing at NHL Stenden. “The software also makes it easy for teachers to review the students’ work.”NHL Stenden prepares graduates to be real-world ready, and Siemens works with academic partners like NHL Stenden to develop a future-proof workforce through software, curriculum, training, and real-world application. “NHL Stenden students always know where the information is and do not need to spend time searching,” says Ir. Mark van der Staay of NHL Stenden.

Students are taught how to overcome multiple challenges including how to teach product development and production, turn ideas to practical solutions, and collaborate in small teams on real-life assignments from industrial clients.

The student keys to success include:
- Use Teamcenter for all engineering-related information from day one
- Use NX for all design and engineering tasks
- Teach students to combine product design, verification and production

Using Siemens software made it easier for teachers to review the students’ work, enabled students to design and build products and the tools required for their production, and empowered students to maximize design and production efficiency.
To read the full case study, click here.