Customized Simcenter Templates Speed Success of Student Competition Teams
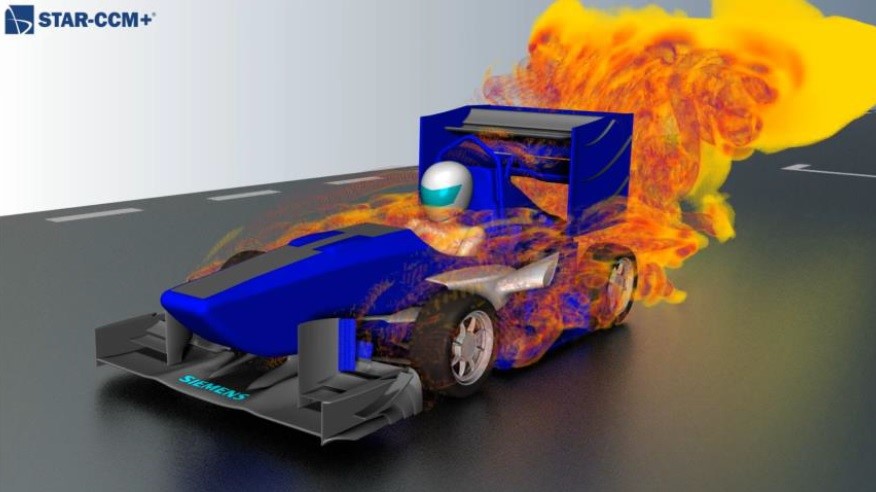
Siemens Digital Industries Software supports dozens of student design-build engineering competitions around the world with no-cost software grants from its Xcelerator software suite, online training and tech support. These compettions reach thousands of student teams and over a quarter-million students.
An additional way that Siemens speeds these students success is by creating advanced templates and tutorials that are specific to the type of competition, such as Formula Student racecars, solar racecars, and rockets. These templates educate the students in best practices and help them learn and achieve results quickly – despite their frequent 70-100 hour work-weeks across their demanding studies and team tasks. For example just understanding 3D aerodynamics simulation theory and principles as an undergraduate student is daunting, let alone learning a CFD simulation software package and then customizing it for their vehicle. Starting with a blank screen is quite difficult. These simulation templates get them going quickly on the right track. They might even get a bit more sleep!
Following are three examples for Simcenter STAR-CCM+, a very popular 3D multi-physics simulator known especially for it’s aerodynamic and cooling uses (specifically using the software’s Computational Fluid Dynamics capbilities – ‘CFD’ for short). There are vast additional resources for student teams at Siemens’ Formula Student & FSAE Forum which, despite it’s title, also has valuable content for solar car and rocketry teams. Online courses are at Xcelerator Academy.
Much credit for this content goes to Chris Penny of Siemens for developing and refining these templates; he supports student competition teams in the Americas region, but these templates are well used worldwide.
Formula Student/SAE Racecars
STAR-CCM+ has become the de facto standard CFD simulator for Formula Student (FS) teams around the world. There are 823 FS teams in over a dozen countries, with about 25,000 elite students participating. These amazing students are innovating by designing and fabricating racecars with electric drivetrains, autonomous racing and carbon-fiber construction. Top FS racecars can hit 2.5 G’s in corners and accelerate 0-100 km/hr (60 mph) in a shocking 1.5 seconds. See another blog article about Formula Student and digital twin methodology results HERE.
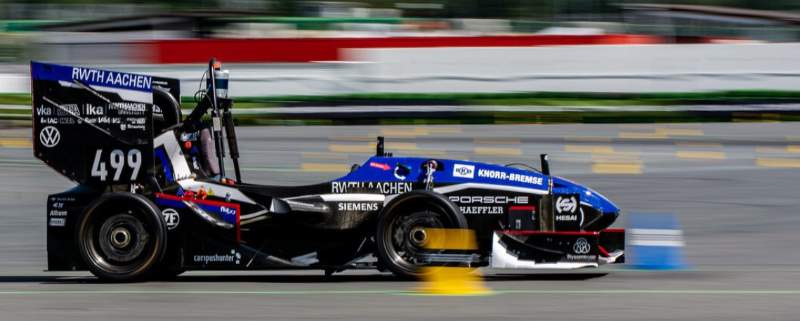
While being as accurate and powerful as its main competitor software, STAR-CCM+ is factors easier to learn and use – even before considering these templates – a mission-critical criterion for student teams – that suffer from large annual personnel turnover. The simulation template for FS teams is at this link: Fully setup FS car CFD in 1 hour: STAR-CCM+ sim template with surface wrapper. A screen shot of that web page is below:
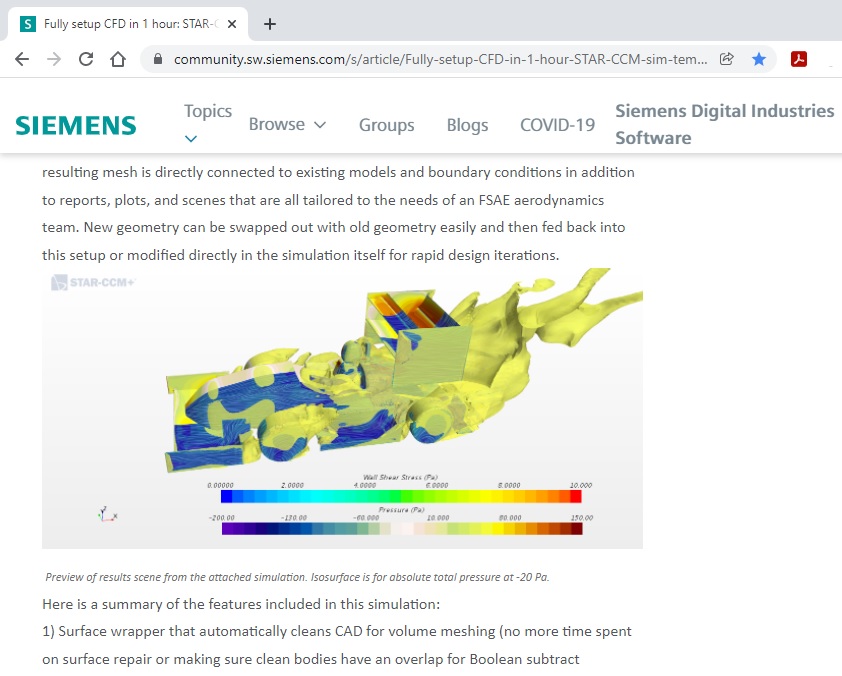
There is an even more advanced followup tutorial that models the drag and downforce while the racecar is turning – a dynamic situation with markedly different air flow. See this advanced 3D CFD simluation technique explained at Formula Student Car cornering CFD setup
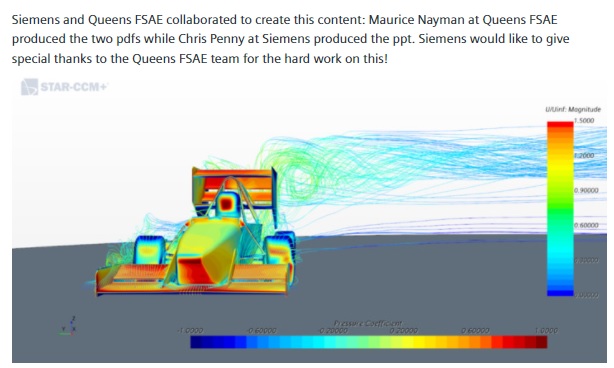
Solar Race Cars
Moving on to solar race cars, there is another STAR-CCM+ simulation template specifically tailored to the needs of student designed and built solar cars.
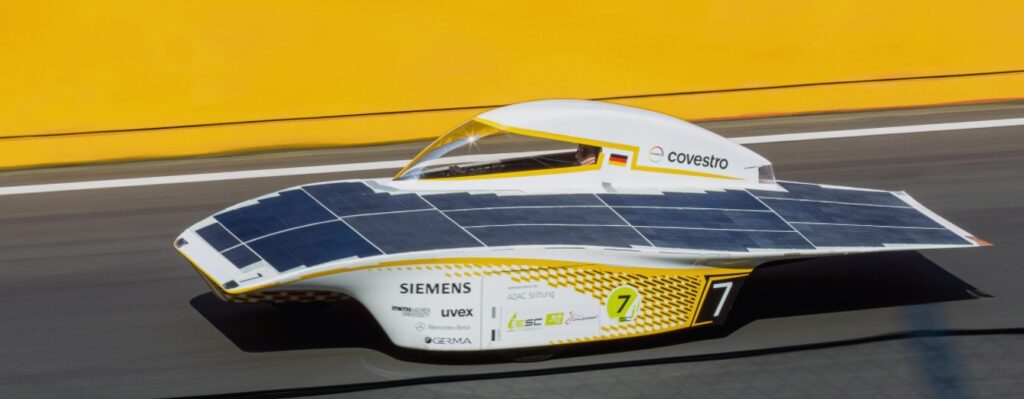
of racing across 3,000 kilometers/1,875 miles of the vast outback of Australia.
This template for solar cars is also easy to adapt to a specific team’s racecar – like the FS car template. The CAD model can be simply changed by modifying the supplied typical model or teams can import their specific CAD from NX or other CAD packages and use STAR-CCM+ surface wrapping and mesh tuning capabilities to make a computationally efficent CFD model. The template can be found HERE.
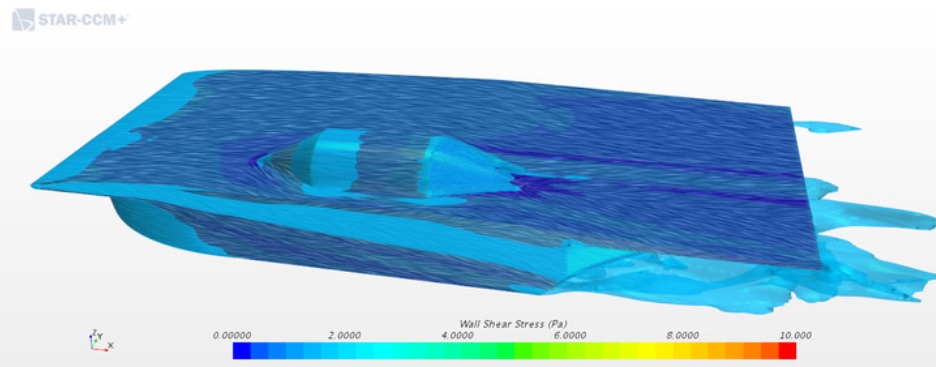
One of the things about sponsoring real-world competitions that Siemens focuses on (versus design-only student competitions) is that the real world can be quite surprisingly educational and even devastating! In the most recent Solar World Challenge in Australia some race leaders crashed and overturned heavily off road when some strong crosswinds rose up.
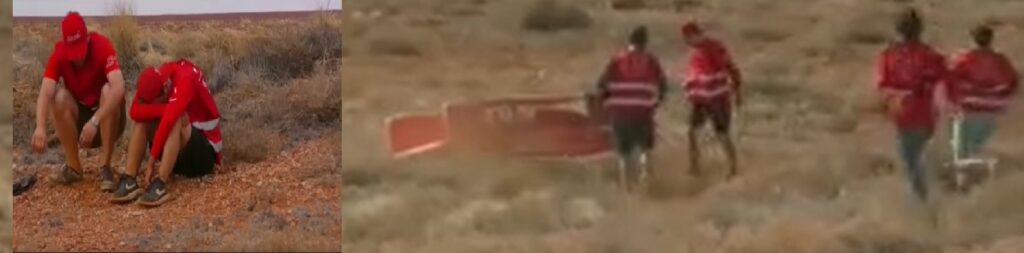
After Chris and Leigh heard about these unfortunate crashes in Australia, Chris upgraded the solar car template to help teams model the effects of dangerous crosswinds.
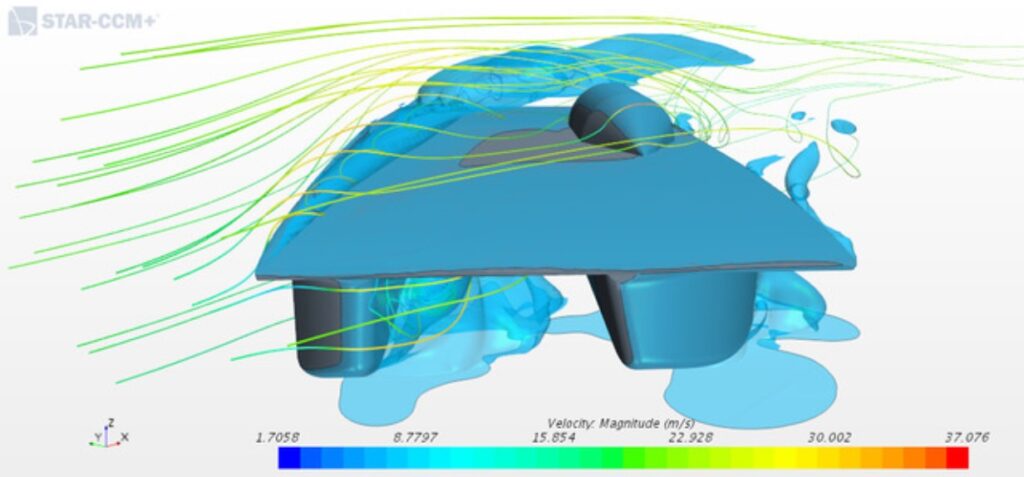
Rockets!
Spaceport America Cup is the premier aerospace competition in the world, featuring student designed and built rockets that soar to 30,000 ft/~9,000 meters (higher than Mt. Everest) reaching speeds in excess of Mach 5 (~6,000 km/hr or ~3,700 mph), enduring extreme stresses. These are clearly not ‘model rockets’ from a hobby shop! Siemens has been a proud sponsor of this competition from soon after its inception, offering rocket-specific technical workshops, software grants and tech support to about 150 teams from ~17 countries. You can find a blog article about the competition HERE.
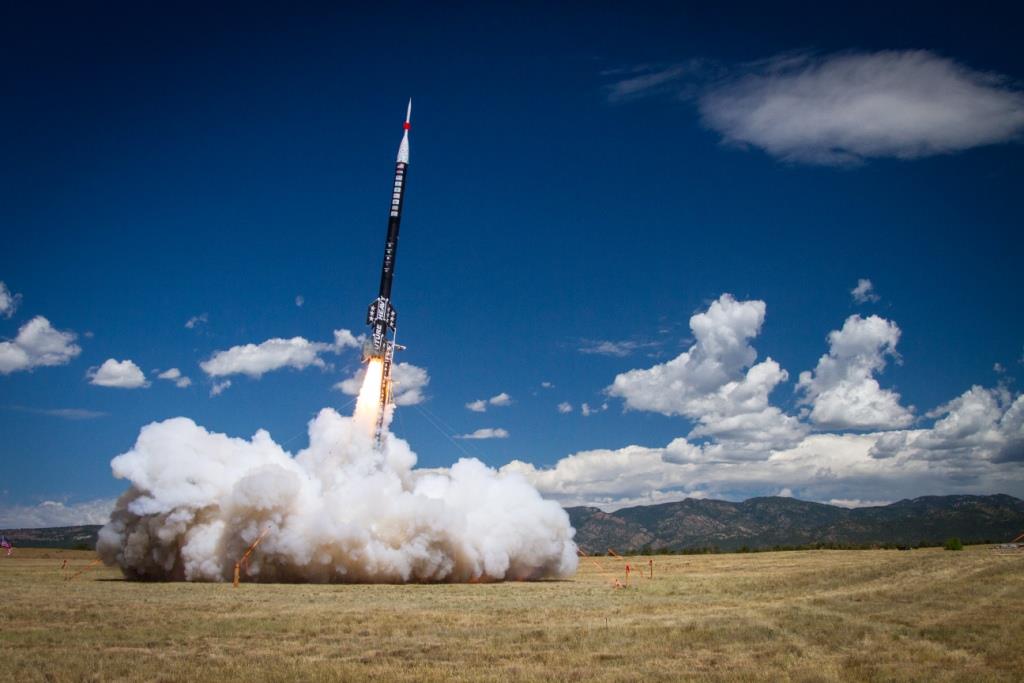
The rocket simulation template can be found HERE. Plus commercial-scale rocket engine simulation articles HERE and THERE. The students use the STAR-CCM+ template to predict drag, thrust, shocks, pressure distribution, etc at different speeds and altitudes in order to optimize fuel load and dozens of other parameters to hit a target apogee just right – they get points for hitting the target altitude precisely.
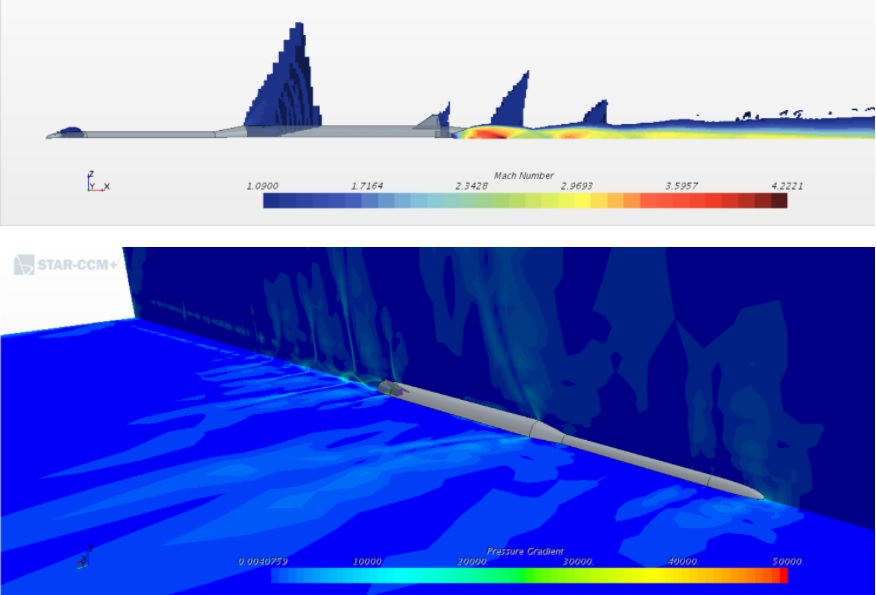
The rocket simulation template can be found HERE. Note that unlike in the automotive world, simulation is the only way to understand rocket designs, except for expensive test launches – there are no physical wind tunnels for Mach 5 speeds!
…and the picture below shows why students need to use tools such as Siemens FEA (strength analysis, Finite Element Analysis) tools and STAR-CCM+ aerodynamic simulations to determine strength of the structure, supersonic shock waves, drag, turbulence plus nozzle flows and pressures.
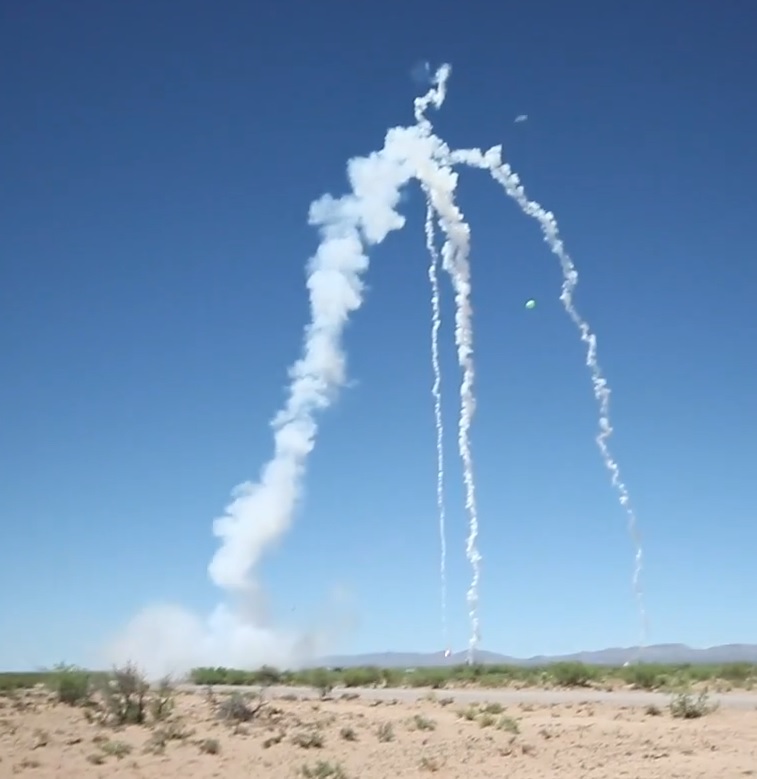
A key life lesson in engineering is about sometimes failing – then doing failure analysis, often with simulation tools (such as Siemens Simcenter tools) and trying – and trying again till you succeed, using the digital twin methodology to succeed more and more often – the first time.
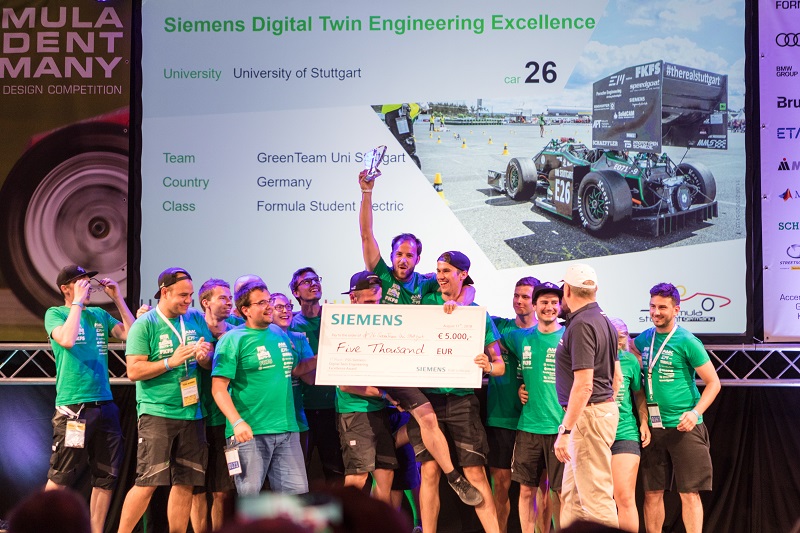
Get your Team a No-Cost Software Grant!
Student competition teams can get free student editions at this site, or apply for full commercial functional software packages, (some of which don’t have student editions) using this online form.
Employers!
Are you concerned about your aging engineering workforce? These student team members are the elite of all engineering students – smart, innovative, incredibly hard-working, with an engineering methodology and Siemens-software experience that will make them great contributors right away. Hire them!
<end>