Maximize Additive Manufacturing with the Cloud-Based AM Network
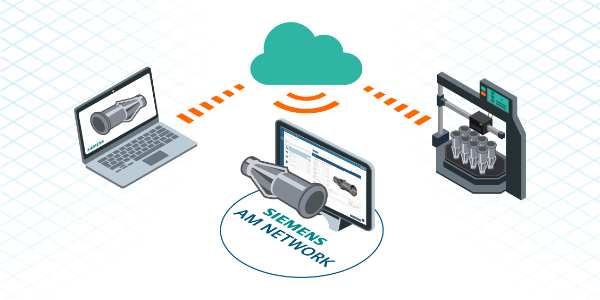
How can today’s industrial companies use new technologies such as additive manufacturing to gain a competitive advantage?
Additive manufacturing is opening new doors to more individual designs and a lot-size of one production. With end-to-end solutions as part of Siemens’ Xcelerator portfolio, companies can leverage 3D printing technologies through an open ecosystem. This cloud-based network of part buyers, print shops, and engineering consultancy gives manufacturers the tools to succeed.
But let’s dive deeper.
In this interview, David Swisa, Business Development Manager, Additive Manufacturing Network, explains what additive manufacturing has in common with a sports car, how a retail sporting goods company boosted production and the value of ecosystems operating in the cloud.
Let’s get started.
David, why do you think additive manufacturing is not being used to its full potential?
I do like to think of industrial additive – so taking this production technology out of its first stages and making it mainstream – like a beautiful sports car. In many ways it inspires us to think about elegant designs, how to be faster, more efficient and reimagine things we could have never done before. But in reality, most of the time we don’t take full advantage of the amazing machine, whether its additive or a sports car.
A sports car sitting in traffic is not utilized to their full degree. Additive manufacturing is no different. Planned utilization of AM machines is high but actual utilization is low, therefore companies want to use additive to its potential but they’re not realizing that potential. Even when controlling for higher costs of additive and increased quality, there are still discrepancies between how it’s planned to be used in a company versus the reality.
When we investigated this further, we found many factors for the low demand in companies, such as the limited know-how of additive among the designers, lack of understanding of the benefits, the difficulties to build a new additive supply chain, unsure of how to manage these additive operations effectively.
And this led to the creation of the Additive Manufacturing (AM) Network. Tell me about the origins of the network.
We took the challenges I just stated very seriously. We, at Siemens, transformed our entire product portfolio for engineering and upgraded it to additional capability dedicated to additive manufacturing starting from product development using generative design and simulation to validate that design. Then we went to manufacturing planning with build preparation and simulation for the build, and eventually for production execution. Finally, we included the analytics of it.
Working with our customers and partners, we realized that AM is not just a technology that changes production – it actually changes how the business is done, like printing spare part on demand instead of building up costly inventory. These new business processes involve not just engineering processes, but also new commercial business processes. For that we built the AM Network, which is a cloud-based collaboration platform designed to streamline and digitalize the end to end order-to-delivery business processes.
What partners are part of the network?
They include machine vendors, part buyers, software vendors, print shops, engineering consultancy, material vendors and others. They provide their expertise and software technology in order to make the entire process of ordering parts more efficient and more effective.
Can you explain how the Siemens’ AM Network supports industrial business processes?
Sure. There are multiple industrial business processes we support, the first being manufacturing. For example, whenever a company needs a part, they can locate and manage their global additive manufacturing suppliers, so you can find the supplier within the network that can produce the part closer to wherever you need it with the right specifications and the right qualities to meet your particular needs.
We also support sharing across the organization while increasing the utilization of the machine. Manufacturers can map them down so that whenever a new demand for a part comes up, they can find out which manufacturing capacities are available within the company, which experts they can connect with in order to get it utilized and eventually utilize and optimize their machines in the most efficient ways. This keeps the knowledge internally within the company. So, this means enterprise companies can be more effectively manage their internal enterprise additive manufacturing resources and can create a network of all the resources within the company.
Finally, AM service providers that operate printers can manage AM operations more effectively while providing customers with better support and transparency. We provide them with the tools they need to streamline their operations, from customer interaction to production planning and monitoring.
And all of this is managed in the cloud.
Correct. Siemen’s AM Network is provided as a cloud solution offered as a software-as-a-service (SaaS) for the customers. So, Siemens assumes all the responsibilities needed to build and maintain the infrastructure instead of the customer and, therefore, the customer reduces their IT infrastructure cost.
What benefits does this model bring?
Our AM Network is built on a robust infrastructure providing enterprise-ready IT solutions with SaaS. This means, all functionality is accessed using a web browser so there is no installation or other maintenance of the solution required. We implement state-of-the-art security best practices via role-based access management. Sensitive data is encrypted from start to finish, and everything is centralized via authentication management. Of course, everything is compliant with privacy regulations. It’s the customer who owns the IP, not Siemens.
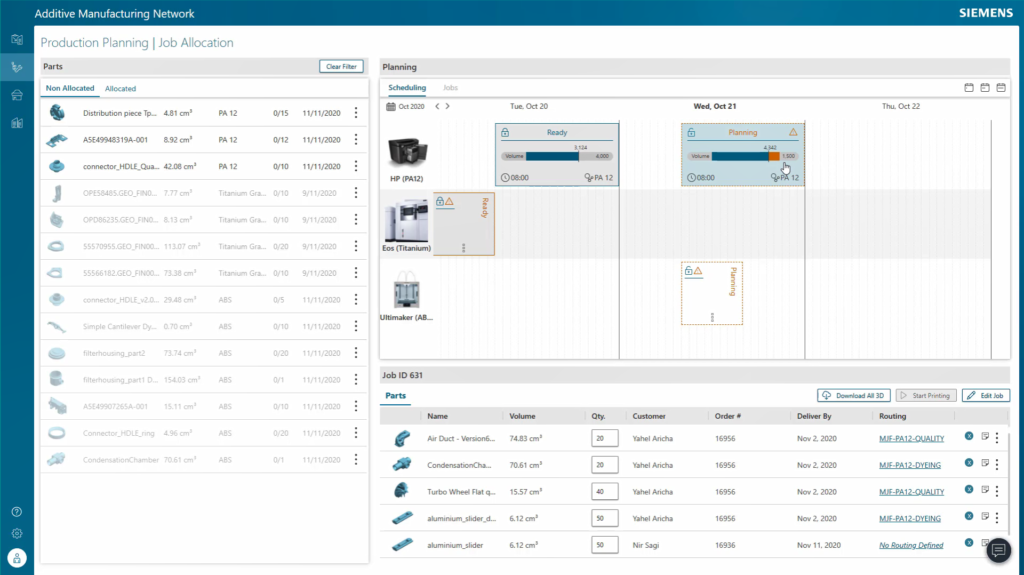
How does the AM Network fit into the Xcelerator portfolio?
Xcelerator is a comprehensive portfolio of software, services and applications which supports the digital transformation of industrial companies. This includes collaborative design, simulation and validation software which is so important for industrializing additive manufacturing. By enabling participation in an open ecosystem of innovation, collaboration and improved operational performance – like the AM Network – it gives companies the tools they need to create previously unimaginable designs and a lot-size of one production.
Can you name a company that has utilized the network?
The one I like to share is one of the largest sporting goods retailers in the world.
They were rapidly expanding on-demand product development process leveraging additive manufacturing and they started to experiment with additive as a tool for manufacturing prototypes.
Very quickly they got huge demands from their designers. Everyone wanted to use the technology to get their parts produced quickly. The challenge was they couldn’t manage the overwhelming amount of parts into their shop. So, this retailer came to us and we set them up with Siemens’ AM network. Within the network, we built the company’s own internal network for managing the different production sites so they were able to manage and track resources across the entire company no matter the designer sits or where the part has been produced. This was all in one centralized solution. They were also able to expand their business from one single machine to 40 in just two years increasing their output to 65x more parts produced in that time.
But it’s not only for internal demand, they were also able to connect to external suppliers that would fulfill orders for material and technology they could not support internally. And they were able to serve external customers within the AM network and connect to the system and order parts from their particular production shops.
How has COVID-19 changed the need for cloud-based collaboration models like the AM network?
One of the consistent, never-ending needs in a pandemic or even, let’s say, a bad flu season is medical supplies and devices. You try to flatten the curve to spread out hospitalizations and it’s more manageable. But during spikes the need is greater and often the supplies are fewer. Moreover, the global supply chain was broken – companies couldn’t get the products and spare parts from their regular suppliers overseas. We’ve opened the Siemens’ AM Network Platform to everyone who requires medical device design or print services.
And it’s this open network that allows professionals to reach designers and local suppliers who will prepare the parts needed to keep medical centers running.
If the reader could take away one aspect of the benefits of the Siemens’ AM Network, what would you want them to remember?
AM is fundamentally changing the approach to designing products. Siemens created this network because companies need a fast, efficient and cost-effective entry into additive manufacturing capabilities in order to remain competitive and to scale their business. Looking for more information?
Check out our webinar: Maximize your business potential with Siemens’ Additive Manufacturing Network or our AM Network website and learn how the this network was built to accelerate the adoption of industrial additive manufacturing and unite manufacturers, suppliers and technology partners to form an AM ecosystem.