Enabling sound design through more accurate industrial vibro-acoustic trim models
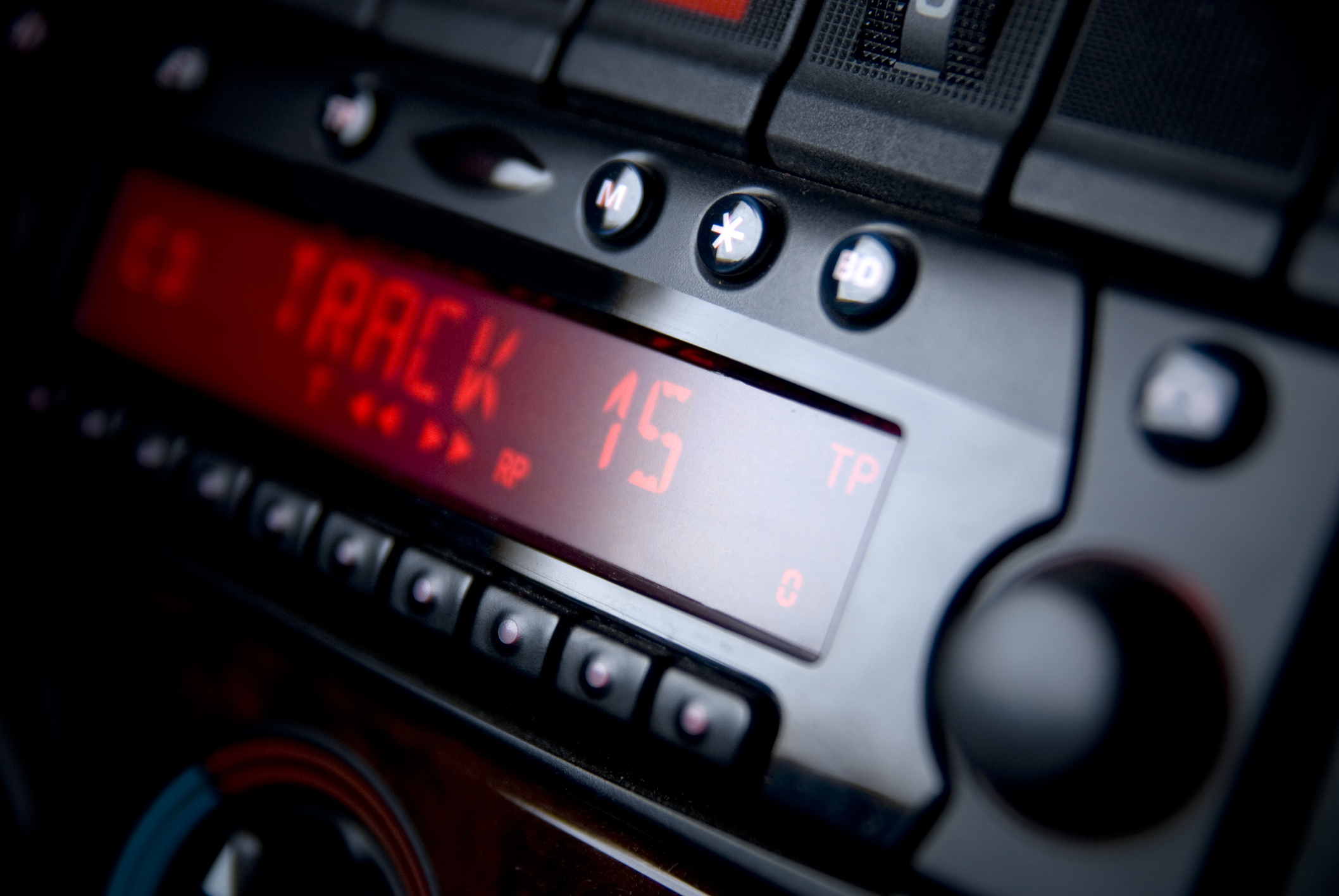
Current-day product design engineers from many industries (manufacturers of cars, trains, planes, industrial machinery, white goods, smartphones, …) find themselves at the crossing of two important industrial trends. On the one side, ecological awareness and high commodity prices push towards more lightweight products to reduce mass (and thus CO2 emissions) and material cost. This typically however, affects the Noise, Vibration and Harshness (NVH) characteristics of the product. And that conflicts with the second trend, namely the increased attention of customers to the NVH performance of products. Clearly, manufacturers need to master the NVH performance of their product and optimize it to meet customer expectations (characteristic brand sound, associated with quality) and legal requirements (e.g., on mitigating interior and exterior noise level).
Essential for making more quiet lightweight solutions are so-called Trim materials. These materials are often multi-material layups consisting of poro- and visco-elastic layers, which essentially dissipate NVH energy present in the system to mitigate vibration and noise. The trim materials are patched onto the main structure to dissipate the acoustic energy of sound waves and the vibrational energy of the structure, which in turn also reduces the radiated noise from the structure.
Unfortunately, it is challenging to accurately capture the trimming material’s damping characteristics in a vibro-acoustic simulation model. This can lead to a model with a high computational cost (as needed to capture the underlying physics). Practical applicability often requires an expert to fine-tune such models to balance the computational load and accuracy as much as possible.
Efficient trim modeling and accurate vibro-acoustic integration
Virtual prototyping has become a cornerstone in the product design engineering process. By first modeling the envisaged product and virtually simulating its performance for various performance attributes including NVH, design engineers can make better products, faster [1].
The Simcenter 3D Acoustics environment [2] is packed with relevant acoustics modeling and simulation capabilities, such as FEMAO (Finite Element Method with Adaptive Order, a high-order adaptive Finite Element technology [3][4]) and AML (Automatically Matched Layer, an automatic non-reflecting perfectly matched layer / PML) for unbounded acoustics [5]). Recently, these have been extended to include trim material modeling and predicting their effect on the vibro-acoustic product performance [6]. These enhancements are based on two recent methodological breakthroughs that were achieved by researchers at Siemens Digital Industries Software.
Firstly, the applicability of the FEMAO method is extended to the modeling of noise reduction materials [5][6], which allows non-expert users to create tailor-made and highly efficient numerical models of trim components inside their vibro-acoustic environment. Starting from a geometrically accurate Finite Element model, all physics of the problem are considered, e.g., including the fluid-structure interaction. We enable our users to estimate upfront the accuracy of their FE model, which gives them the handle to balance computational effort with user-specified accuracy targets.
The second innovation is predicting the impact of trimming materials on the vibro-acoustic system model without solving the fully coupled problem [7]. Firstly, the undamped vibro-acoustic system is reduced to its characteristic eigenmodes, resulting in a highly efficient modal model, which is the recommended practice for solving problems of industrial complexity. Next, the trim system is investigated separately to assess its damping- and transmission properties between the acoustic- and structural interfaces. These analyses can leverage on the FEMAO achievements mentioned above. In a last step, the undamped vibro-acoustic modal model is corrected with correction terms for the trim treatment, which results in a system-level damped vibro-acoustic modal model.
Demonstration case
The modeling capabilities are shown [8] on a representative generic car cabin with a flexible roof, with and without trimming treatment. The cavity is excited through a boundary condition representing the vibrating membrane of the sound system loudspeaker in the driver’s door, and the acoustic response at the driver’s head location is captured.

The vibro-acoustic model (left) is projected onto its 149 structural- and 722 acoustic modes between 1 and 1200 Hz. The trimming is modelled using an adaptive order FE model, which, due to the order adaptivity, can be run on a rather coarse mesh (right). The element orders are calculated to satisfy a set error threshold on an a prior error indicator (see example of order distribution below).
The influence of the trimming on the acoustic response at the driver’s ear can be seen in the averaged FRF at the driver’s ear, shown in the figure below. It shows that the treatment starts to play a role around 400 Hz (where the effect of damping starts to become clear) and has an outspoken influence from 800 Hz onwards (with a high damping effect achieved). For the driver, mainly the amplitude of the higher tones will be reduced, while the booming of the cavity will still be present.

Looking at the left- and right channel spectrogram for P1, generating using the Short Time Fourier Transform (STFT), the undamped case shows overall more energy, especially at higher frequencies.
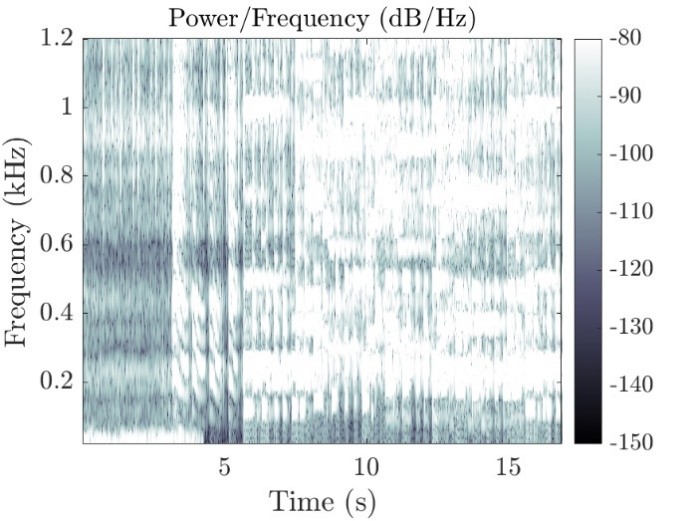
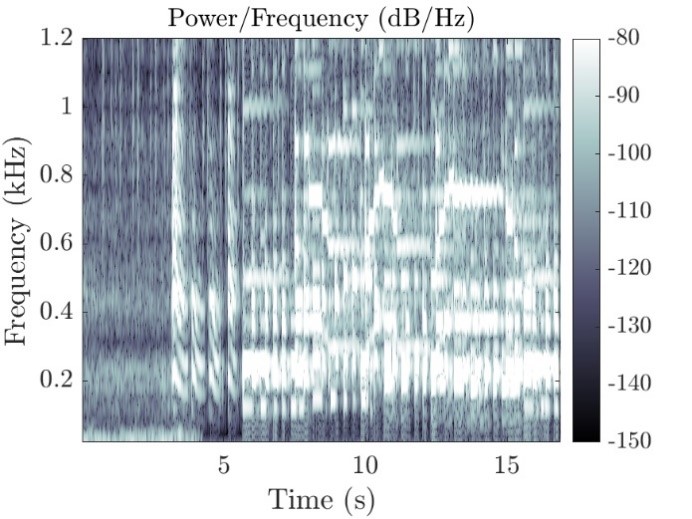
This is further demonstrated in the following audio sample, where the driver’s head moves around freely as captured using a Virtual Reality device. Additionally, the user switches between the undamped and damped configuration every 5 seconds to verify the influence of the material treatment, allowing to assess the acoustic treatment effects in real time. Obvious changes between the undamped and damped configurations are the dulling of the sample, especially the drumstick beats in the beginning.
Acknowledgements
The work leading to this publication has been performed by Dr. Stijn Jonckheere in the frame of the project “Advanced modelling and correlation of complex VIbro-acoustic systems – towards Digital twins” (AVID), a VLAIO (Flemish government agency Flanders Innovation & Entrepreneurship) Innovation Mandate which provides support to postdoctoral researchers to achieve an effective transfer of knowledge and valorization of their research results, allowing them to make the transition into the business world and bridging the gap between academia and industry.
In the project, Siemens Digital Industries Software joined forces with the KU Leuven Mecha(tro)nic System Dynamics research group (LMSD) as the academic partner. The group strives for international leadership in engineering dynamics through excellent research, education and services; building upon an expertise of five decades in dynamics modeling, simulation and testing, and with the Digital Twin concept – a physics based virtual replica of a real life system which is continuously updated with measurement data – playing a pivotal role in its roadmap towards Industry 5.0 [9]. In the entrepreneurial LMSD philosophy, cross-fertilization between strategic basic research, application-oriented developments and technology transfer activities is key. Being at the origin of spin-off company LMS International, now Siemens Digital Industries Software, as well as the collaboration within AVID are a prime example of this.
References
- D. Lowther, R. Bornoff, “Engineering simulation part 2 – Productivity, Personas and Processes”, ‘The Art of the Possible’ blogpost, July 10, 2023.
- Siemens Digital Industries Software, Simcenter 3D, Retrieved 2024.
- Siemens Digital Industries Software, “Efficient and Accurate Broadband FEM-based Vibro-acoustics (Part 1)”, Simcenter Blogpost on FEMAO technology, April 2018.
- Siemens Digital Industries Software, “Broadband vibro-acoustics – Simplifying modeling and speeding up simulations”, Simcenter 3D White Paper, 2019.
- S. Jonckheere, H. Bériot, O. Dazel, W. Desmet, “An Adaptive Order Finite Element Method for poroelastic materials described through the Biot equations”, submitted to International Journal for Numerical Methods in Engineering, 2021.
- S. Jonckheere, H. Bériot, O. Dazel, W. Desmet, “Efficient adaptive order poroelastic material modelling within modal vibro-acoustic system models”, Proceedings of ISMA 2020, Leuven, Belgium, September 7-9, 2020.
- K. Hamiche, “Efficient and accurate trim modeling with Simcenter 3D”, Simcenter blogpost, May 2021.
- S. Jonckheere, J. Cardenuto, T. van Putten, H. Bériot, E. Deckers, “Efficient auralization of vibro-acoustic systems with trim packages”, Proceedings of ISMA 2022, Leuven, Belgium, September 12-14, 2022.
- J. Schlegel, “Industry 5.0 already??”, Simcenter blogpost, January 19, 2022.