Part 3: Top ADAS issues
These topics to deserve a little more attention so this will be broken into a 3 part series. Part 1: Introduction to ADAS; Part 2: Impact of ADAS on wire harness design
Part 3: Top ADAS issues
Among the most rewarding aspects of work at Mentor is the chance to collaborate with our experts around the world working on a range of disruptive automotive technologies that appear regularly in the news. One of these experts is Martin O’Brien who is based in Newbury, England and serves as general manager of the Integrated Electrical Services Division focusing on cabling and wiring design, and harness engineering. Another is Amin Kashi, Mentor’s director of ADAS based in the Silicon Valley (in our Fremont, Calif. office). The two recently collaborated on an article that will run this fall in Hanser Automotive, a leading German trade publication. Here is the English version of Part three in a three part series. To read part 1 which is the Introduction to ADAS please click here and Part 2 discusses the issues in wire harness click here.
EDS design and engineering teams aren’t the only ones dealing with complexity and tradeoffs. Those working on ADAS technologies face balancing acts of their own: How to add more features without overwhelming, or worse, distracting drivers? And how to keep drivers engaged in operating the vehicle even though more safety-related enhancements are available?
Wrestling with such questions can be a highly public matter and tech enthusiasts armed with cell phones and social media accounts don’t always make life easy for carmakers. A 2014 YouTube video “Infiniti Q50 Active Lane Control – Selfdriving Car” includes footage, set to Wagner’s “Ride of the Valkyries,” of the driver testing the system on the highway from the backseat. One commenter on the video, viewed more than 680,000 times, draws the most apt conclusion: “Car’s got more brains than the driver.”
The behind-the-scenes ADAS issues are hard enough without the PR headaches. Much of the complication stems from issues of centralization, particularly when it comes to processing sensor data. Surely there are advantages, including lower cost, to moving to a smaller number of more powerful onboard computers. A minor fendHer bender quickly gets expensive if damage results to front-grille radar module powered by a complex SoC and lots of custom software. Better to gradually shift to relatively dumb sensors and cameras that send data back to a central processing hub.
However, this shift and convergence of systems brings with it a number of integration challenges. One way to consolidate functions and reduce electronic component count is by leveraging software to combine multiple complex domains, e.g. via a virtualization technology such as a hypervisor, which allows various applications to share a single ECU. In essence, the ECU is divided into several virtual environments, each running its own distinct, secure real-time operating system and software. The individual applications think they have their own physical piece of hardware, and so can work side by side on the ECU, without knowing anything about each other. A recent article by Ann Steffora Mutschler delves into the details of hypervisor. Expert knowledge of system-level design – including architecture definition, safety and security, hardware and embedded software techniques, all operating under the broader umbrella of automotive industry requirements – is key to addressing the challenge of development of next-generation ADAS systems.
Other ADAS-related challenges have little to do with engineering at all. As just one example, a several regulatory and insurance decisions loom as computers and algorithms take on more driving tasks. How is fault apportioned in an accident in which ADAS technologies are involved? Uncertainty about this and many other questions is likely to be the norm for years to come.
Which isn’t to say this ambiguity is dampening ADAS innovation and investment. Sensing and mapping seem to be the biggest opportunities and hottest trends, at least based on startup activity. Among the notable examples: Quanergy (backed by Delphi), which offers the first solid-state LiDAR sensor for ADAS , and Civil Maps (backed by Ford), developing 3D mapping technology.
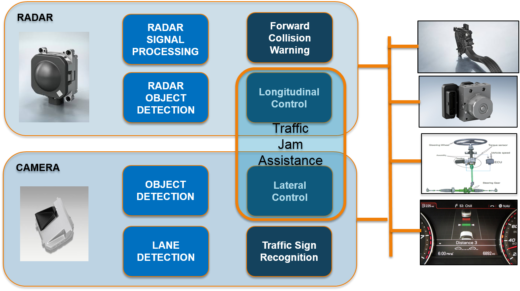
Most industry analysts expect to see ADAS-related revenues increase by more than 10% annually through 2020, according to a McKinsey report. The same report includes survey data from 4,500 car buyers in five countries, including Germany. Nearly 90% of respondents driving ADAS-equipped cars said they would likely buy a car with ADAS features in the future.
This suggests that today and for years to come, the premium will be on those design teams — and technology vendors, like Mentor — that can handle cascading systems engineering challenges, from software platforms to hardware design to automotive networking (data and electrical). Design flows will need to span domains as never before, from early-stage specs to final realization. Such flows will need to be flexible enough to handle everything from proof-of-concept to full production intent. And all this must be implemented while adhering to the industry’s rigid safety and reliability requirements — the spirit and intent of which motivate much of the work on ADAS in the first place.
Martin O’Brien is general manager of the Integrated Electrical Systems Division at Mentor Graphics based in Swindon, England. His 2016 IESF conference presentation, “You Can’t Test Quality into Products!”, is available here: http://bit.ly/2a7ZvTr. Contact him at martin_obrien@mentor.com.
Amin Kashi is director of ADAS at Mentor Graphics, based in Fremont, California. Contact him at amin_kashi@mentor.com.
ADAS, ECU, engineering, fatalities, safety, systems engineering, wire harness