Autonomous vehicles: the Chevy Spark problem
Autonomous driving is cool and sexy. Everyone is talking about it. Everyone has an opinion. My German friends say “no thanks, I’d rather drive myself on the Autobahn.” Technologists ask, “how can machine learning algorithms be demonstrated as functionally safe using conventional methodology?” (Sorry, they can’t). And everyone, established companies and newcomers, are dumping massive R&D into the effort to get self-driving to move from science experiment to reality. Throw in electrification and we’re really talking about a once-in-a-century industry transformation — eventually.
For now, we as an industry are firmly in the R&D domain. The new business models and revenue streams driving these massive investments (McKinsey estimates $1.5 trillion in new revenue streams by 2030, including shared mobility, apps for cars, remote services and vehicle enhancements sold as software over the air) require manufacturable vehicles, in volume, to a budget, and across multiple electrical and electronic platforms. How do we cross that chasm from R&D prototyping, proof of concept, and test cars, to mass-produced, commercially viable autonomous and electric mobility?
Here are five things that need to be addressed to get there:
- Increasing number and variety of sensors. Autonomous vehicles require an array of sensors to create an environmental map of their surroundings and process that data in real-time, then decide what the correct course of action is. Today we see plenty of test cars in many U.S. cities with cameras and lidars, collecting driving data and testing software algorithms. But these vehicles are not even close to commercially viable. A mechanical lidar can cost as much as six Chevy Sparks today. Which is bad news if you want a self-driving Spark. And if we think of robo-taxis and fleets of small-form vehicles as the future of mobility, this clearly doesn’t work. Sensors — especially lidar as we move towards solid-state solutions — need to come down in price and size, and then located in optimal locations around the vehicle for performance and manufacturability. (Some carmakers are looking at lidar in the headlamp casing, for example.) But placing miniaturized components into confined spaces creates thermal issues. This means more physical testing to ensure reliability & spec compliance, which adds time and cost. Increasingly the industry is using virtual models of sensors and their environment to speed up this process, get more accurate data, and solve cost and size problems in the virtual world rather than exclusively using test cars.
- E/E architecture optimization. Stats are frequently cited on the complexity of electrical and electronic (E/E) system today. A premium vehicle can have 5,000 meters of cabling, 100+ ECUs, 500 LEDs and so on. Designing these complex E/E systems is now beyond human capability. Just as the semiconductor industry had to adopt synthesized design methodology decades ago, the auto industry is shifting in exactly the same direction for vehicle architecture design. Automation was inevitable even before we added in 30+ sensors for full autonomous drive, multiple voltage rails required for the power electronics in electric vehicles, and the high-bandwidth communication lines to shuffle massive amounts of sensor data around the vehicle. The solution is to create an abstracted model of this reality, with automatic transitions from simpler to more detailed levels of abstraction. This comprehends design rules (e.g., a maximum of five wires going into the door), and also the complexity that consumer options can create. Multiple car platforms with pages of options can easily create billions of E/E permutations. Virtual design of the E/E system allows an optimized architectural platform to be created, correct-by-construction, reducing the cost and weight of the vehicle.
- Sensor fusion power management. In the prototype world it doesn’t really matter that much if the autonomous drive test car has a boot (ok, trunk) full of electronics, burning a gazillion watts, and 50 kilos of extra wiring to handle all this mess. But in the real-world future of electric, autonomous mobility, this mess has significant implications for vehicle range. When everything is powered from a battery, the difference between a centralized autonomous drive system consuming 100 watts and some kind of distributed system at 1,000 watts can be more than a 30% reduction in vehicle range. Hybrids can help in the near future, but with six countries already having announced a ban on gasoline by 2040, and others including China having indicated the same intent, the power consumption problem looms. Again the answer is simulation, in this case how the electric powertrain. Take the Urban Dynamometer Driving Schedule (UDDS), an EPA-derived city drive cycle for measuring fuel efficiency of light vehicles, model how an electric powertrain would handle the same cycle, and determine the vehicle range impact of different sensor fusion power loads. Then add in the rest of the vehicle network for the same analysis. Simulating vehicle electronics enables designers to quickly trade off vehicle range against new features and find creative ways to maximize range — all in a virtual environment, which speeds up time to market and reduce the need for in-car, physical testing.
- Validation and verification of autonomous drive systems. Akio Toyoda, president of Toyota, estimates that 8.8 billion miles of road testing is needed to get a high enough confidence in a level 5 autonomous vehicle system. Or to put it another way, 500 cars, driving at a constant speed of 60 mph, 24 hours a day, would take 54 years to gather enough data to validate and verify the system. Most traffic scenarios are predictable and manageable, hence the need to cover so many miles to find the edge cases and complex scenarios that can be used to train the machine learning algorithms. An alternative is to create virtual models of the real world and build traffic scenarios using a sensor model library. These scenarios can be fed into a hardware validation and verification platform, similar to a production-level sensor fusion platform, creating labeled and traceable sensor events. The decisions taken by the sensor fusion system can then be fed to a driving simulator to check that expected results = measured results. Then the loop is closed by sending this result back to the input phase. This type of simulation can comprehend databases of traffic accident data, enabling virtual testing of autonomous driving scenarios in a closed loop environment — and giving system designers a realistic path to validation and verification without the 54-year lead time.
- Digital data continuity. The points above represent an illustration of how vehicles are a complex system of systems. Sensors influence vehicle architecture, which defines the E/E framework of the vehicle; the power loads of this system directly impact vehicle range, and this, in turn, requires optimization of every other subsystem. How do we understand the big-picture impact of something as simple as consolidating two ECUs into one, for example? What about cost, weight, power and space constraints? Digital data continuity is an essential element of the design process, allowing fast analysis of changes to the system between domains, and enabling optimal engineering trade-off decisions to be understood and verified. The above examples (1-4) illustrate that designing systems in isolation doesn’t work in the world of autonomous electric mobility. This digital thread enables an unbroken data flow within and between engineering disciplines, which in turn enables traceability, impact analysis and design change management — continuity that is not optional if we want to jump the chasm.
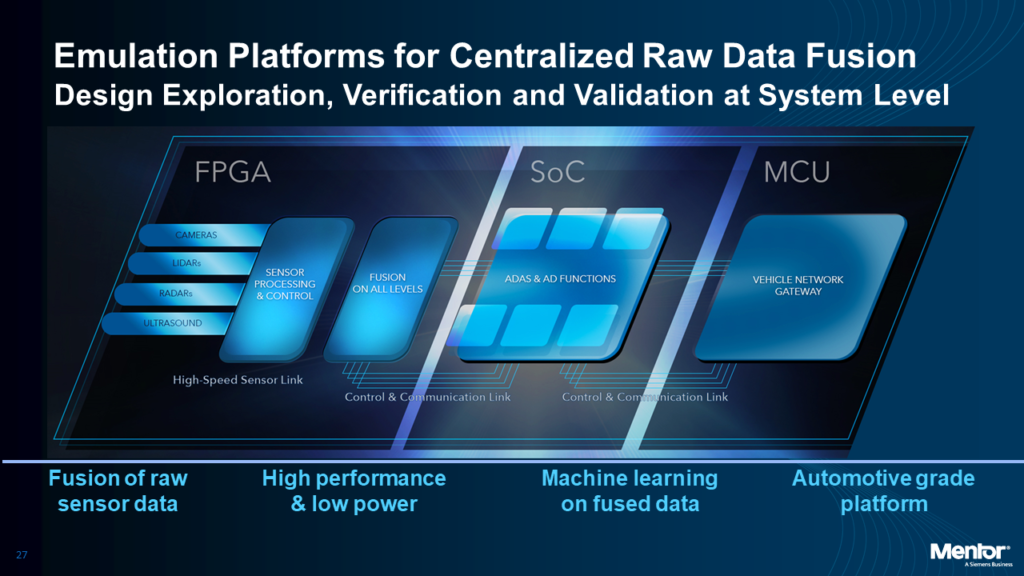
So what’s the conclusion? Well just as semiconductor design evolved from manual to computer-based virtual design, so too is design for automotive electronics and mechanical systems. Creating a digital twin of an automotive system (a model-based representation) is now required for the optimization of system performance, cost and reliability. And those who master and apply virtual design, simulation, verification and validation technology in the automotive space will be those who capitalize fully on the opportunities created by autonomous and electrified mobility, and help the industry jump that chasm from R&D to viable mass production.
And that’s good news for Chevy Spark fans.
I invite you to follow me on Twitter (@AndyMacleod_MG).