How to plan and optimize auto manufacturing operations virtually to drive efficiency
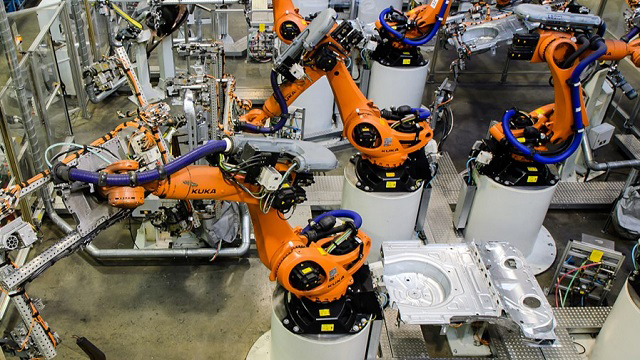
The automotive industry is undergoing transformation due to new technologies and consumer demands, making new product launches more complex than ever. Virtual manufacturing engineering offers a solution: all engineering disciplines collaborate in a unified digital environment. This accelerates development across work cells, lines, operations, and plants. Advanced simulation allows for virtual equipment testing and issue identification before physical commissioning, avoiding costly redesign cycles and delays. Automotive manufacturers and suppliers can also optimize energy and raw material usage for sustainability. At the same time, human simulation capabilities reduce downtime, errors, rework, and costs and enhance workplace safety.
Watch the video to learn how to rethink your approach to production line creation and optimization and deliver high-quality products on time all the time with virtual manufacturing engineering.
Organize every aspect of the automotive manufacturing lifecycle
Historically, product development begins with engineering, testing, and validation, followed by the development of manufacturing processes. This iterative exercise requires numerous physical builds, tests, failures, and redesigns that increase costs, waste resources, and delay new product introductions. With some key improvements, you can design and optimize operations earlier in development to ensure flawless launches, on-time ramp-ups, efficient production, and a safe and healthy work environment.
Be collaborative in automotive manufacturing engineering
With a digital data backbone, you can share critical product information with manufacturing engineering much earlier, enabling collaboration between product and production teams. This early access to data allows your manufacturing team to develop assembly processes and plan for automation in the digital world before launching production.
Add predictability in your automotive plant
The digital backbone of data is also your first step to building a virtual replication of manufacturing, the digital twin, which you can use to simulate the behavior of your plant, assembly lines, and individual assets to understand how everything will interact. This preemptive identification allows for modifying processes and implementing safety measures before the production line is physically established.
Ensure safety in automotive production
By leveraging digital simulations and immersive technologies like virtual reality (VR) and augmented reality (AR), you can identify potential safety issues and address them before they become real-world problems. You can also perform ergonomic analyses by simulating the physical strain on workers performing their tasks. Subsequently, production becomes safer, allowing you to resolve potential issues before they occur.
Be sustainable in automotive manufacturing
Plan for sustainability upfront to optimize resource use, reduce waste, and minimize energy consumption. Efficient design and process simulation allow for the precise planning of material flow and energy usage, enabling the development of eco-friendly plants and lines and reducing your carbon footprint.
Virtual manufacturing engineering for the automotive industry
Putting it all together, our Virtual Manufacturing Engineering solution is designed to enable virtual manufacturing development and optimization for the automotive industry. The solution allows automotive manufacturers to simulate the entire manufacturing process, from product design to production planning, by creating virtual models of their plants and production lines.

With Virtual Manufacturing Engineering from Siemens, you can:
- Virtually design and validate machines, cells, lines, and plants
- Integrate BOM management
- Ensure worker safety with reliable human simulations
- Reduce downtime, errors, and rework