Leveraging digital tools to support faster iteration in software-defined vehicle development
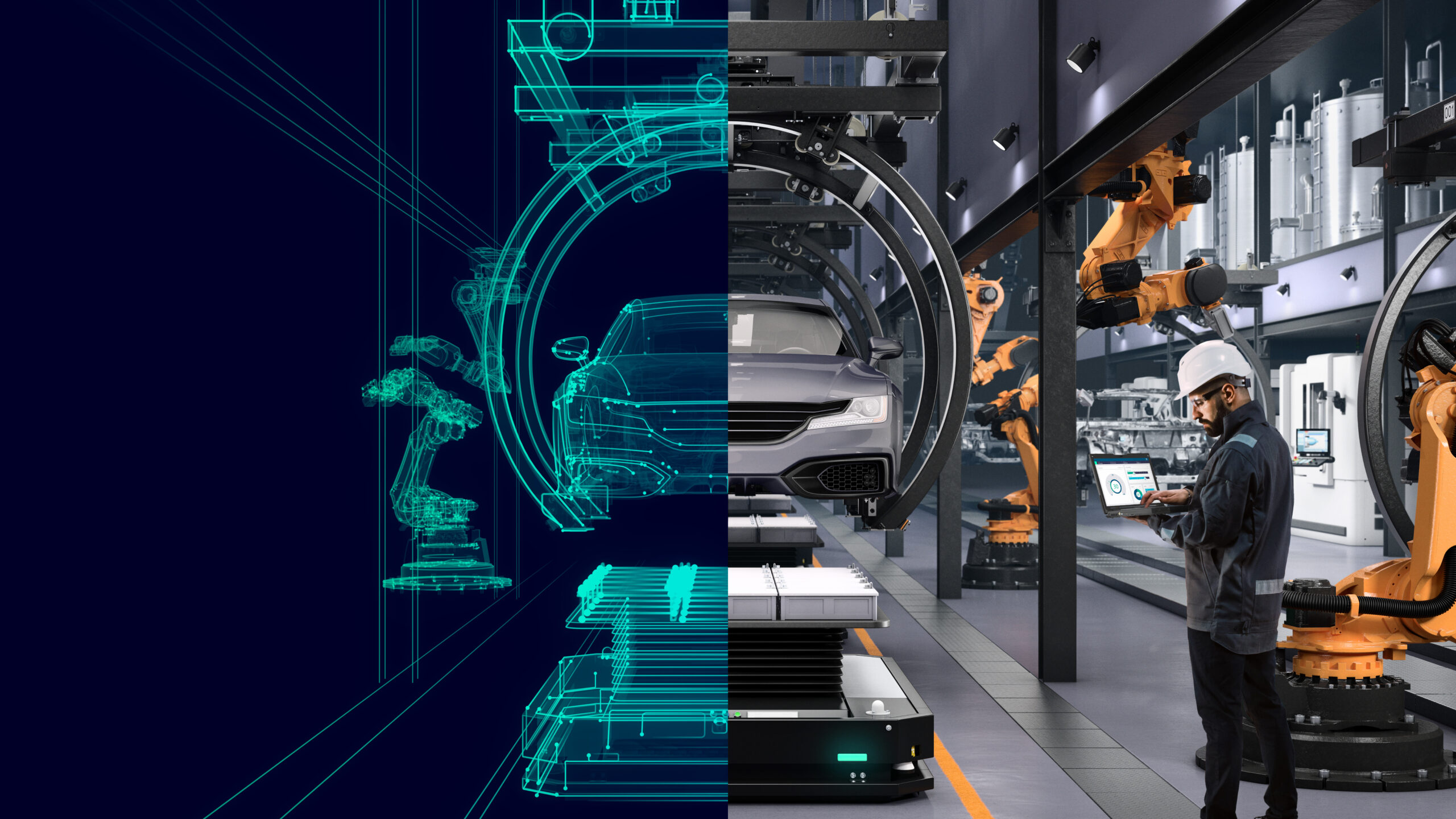
Development of modern vehicles is equal parts excitingly innovating and overwhelmingly complex. Today’s automotive manufacturers are edging closer to autonomous driving, breakthrough safety capabilities, and more sustainable power consumption as software-defined vehicles (SDVs) enable new features.
Unlocking software-defined vehicle engineering through IDE
The engineering work to make these features a reality is significant, including an exponentially growing number of sensors, huge amounts of onboard network traffic, a rising number of custom integrated circuits (ICs) and electronic control units (ECUs), and gigabytes of software code.
This last aspect of modern vehicles, the software side of things, is growing fast. It has become a key enabler of so many features that a new term is being used to describe the trend: software-defined vehicles. As original equipment manufacturers (OEMs) make the shift to developing software-defined vehicles, it begs a critical question: How can engineering teams implement these complex new features in a fast iteration cycle?
Engineering, fundamentally, is about discovery and experimentation. Engineering teams use design models to guide them towards better decisions. Mechanical engineers use mechanical computer-aided design (CAD) and simulation tools. Board systems engineers use electronic design automation (EDA) and simulation tools.
Software engineers rely on integrated development environments (IDE) and emulators. Yet, engineers looking to bring all the different systems together—to iterate and explore the right mix of hardware and software to meet requirements—are often using older, outdated methods and tools that make it difficult to assess the interactions between these different domains.

Digital twins for software-defined vehicles
Traditionally, the engineers responsible for integrating different domain systems have relied heavily on physical prototyping and testing. Unfortunately, this approach is not only incredibly time-consuming—it is also quite expensive.
When engineering teams follow this path, verification and validation happens very late in the design process. This makes it more difficult for engineering to identify potential issues or make larger design changes that could help optimize the design. This approach results in longer development timelines and often comes with significant design rework.
Engineers can also struggle to collect data for analysis, which can limit their ability to iterate and innovate. This can lead to requirements only being partially met, or more pedestrian features that make it harder for companies to compete in the marketplace.
To overcome these challenges, engineers can employ a variety of digital technologies and modeling techniques to hasten their ability to design, test, and iterate different features. By using modern CAD, computer-aided manufacturing (CAM), and simulation tools, engineering teams don’t have to wait for physical testing to gain insights.
They can quickly and efficiently explore the design space. In addition, model-based systems engineering (MBSE) solutionssupport extensive experimentation so engineers can gain a thorough understanding of how each vehicle requirement might be affected by different features or design changes.
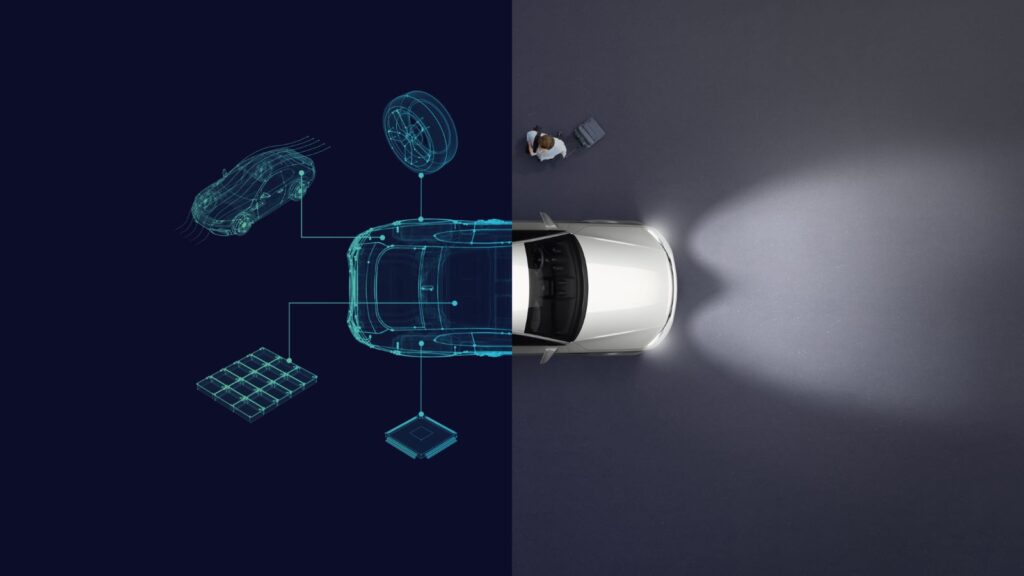
Virtual environment testing for software-defined vehicles
They can explore how different software systems, and the features they power, work in various scenarios.
The ability to conduct a greater number of design iterations with quick turnaround times and better data analysis means that engineers can easily verify the feasibility of each feature and understand how it works in the larger whole of the product. This accelerates the development process and reduces time to market for new automobiles.
Automotive manufacturers can also see significant cost efficiencies in the product development cycle by leveraging simulation tools. They no longer have to wait on physical prototypes. They can virtually test different features across a wide variety of real-world scenarios—and see immediate feedback on the impact of different design decisions. They can then feed that data back into the design process.
This is especially helpful as engineers seek to optimize software and hardware features. They can use the MBSE models and simulation to examine the implementation of different features—and understand how different design edits affect the different hardware and software components, as well as the greater product as a whole.
Simulating for vehicle development resource streamlining
Given the growing prevalence of over-the-air updates, engineers can rest assured that all software-driven features are both functional and safe even in the absence of a physical test. When automotive OEMs use MBSE and simulation, they put themselves at a strong competitive advantage.
They can save significant resources associated with physical prototyping and testing, including material expenses and testing equipment. Engineering teams can work in a virtual environment, extending their capabilities to design and develop bolder new features to spur innovation—and meet consumer demands.
In addition, digital models and simulation tools support more detailed documentation, which is then readily accessible for different stakeholders throughout the development process. This improves collaboration and traceability across the different domain-specific engineering teams.
Accelerate software-defined vehicle feature implementation
As automotive OEMs look to accelerate feature implementation as part of the transition to
software-defined vehicles, they should explore adopting digital modeling and simulation to support the product development process. Then they will be better positioned to manage the increased number of
sensors, onboard network traffic, lines of software code, and more.
They can more quickly experiment, iterate, and innovate to support modern safety capabilities, more sustainable power consumption, and the latest consumer-driven automotive features. By leveraging this faster design iteration cycle, they can design the kind of modern vehicles that consumers want—while
meeting all design, sustainability, and safety requirements.
Comments
Leave a Reply
You must be logged in to post a comment.
I like the way you explained this topic overall. Great effort, Appreciated.
https://libgenis.net