Optimize metal fill insertion while protecting critical nets and devices…automatically!
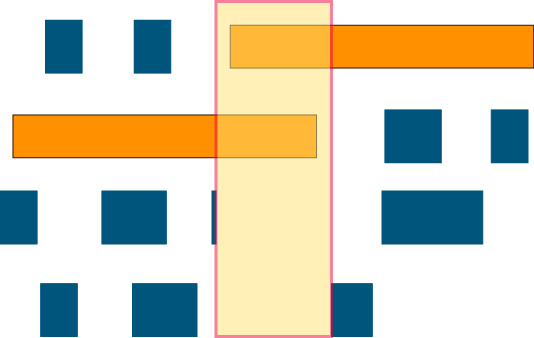
By Dina Medhat
Context-aware physical verification (PV) is a relatively new addition to traditional PV flows, but it has quickly become a critical and essential technology that addresses the increasing complexity of geometrical checks used in both established and emerging integrated circuit (IC) technologies. Traditional verification tools handle either the physical verification of the layout shapes or the electrical verification of the circuits, but not both.
For as long as there have been design rules, there have been design rule checks, and for as long as there have been netlists, there has been electrical verification, but these were historically distinct and separate verification flows. However, designers are facing new verification challenges in today’s tightly-packed designs that cannot be solved by either of these verification techniques in isolation.
Context-aware checks combine the physical layout of a component with its electrical implementation, and analyze that information to evaluate a wide range of design conditions, from advanced design rule compliance to circuit and reliability verification to design optimization and finishing.
One example where context-aware PV can provide significant value is metal fill insertion. Adding metal fill to a layout is an essential step at advanced nodes to ensure high yield and manufacturability. However, inserting metal fill adds capacitance, which affects timing, especially for critical nets in the design. As radio frequency (RF) and analog designs are sensitive to parasitic capacitive coupling between signals and fill, these critical design elements (nets/devices) must be identified for enhanced protection during fill insertion. To ensure both accuracy and speed, design teams need a methodology that automatically links design awareness with metal fill insertion for optimized fill solutions that protect critical design elements.
Combining context-aware analysis capabilities of the Calibre PERC reliability platform with advanced design density analysis and fill solutions of the Calibre YieldEnhancer SmartFill functionality provides fast, accurate, automated identification of critical/sensitive nets and devices for optimized fill insertion. If you’re interested in learning more, download a copy of our technical paper, Automated design-aware optimized fill ensures both timely design closure and design reliability.