Consumer Products & Goods Manufacturing Excellence: Top 5 Reasons to Use MOM Versus ERP
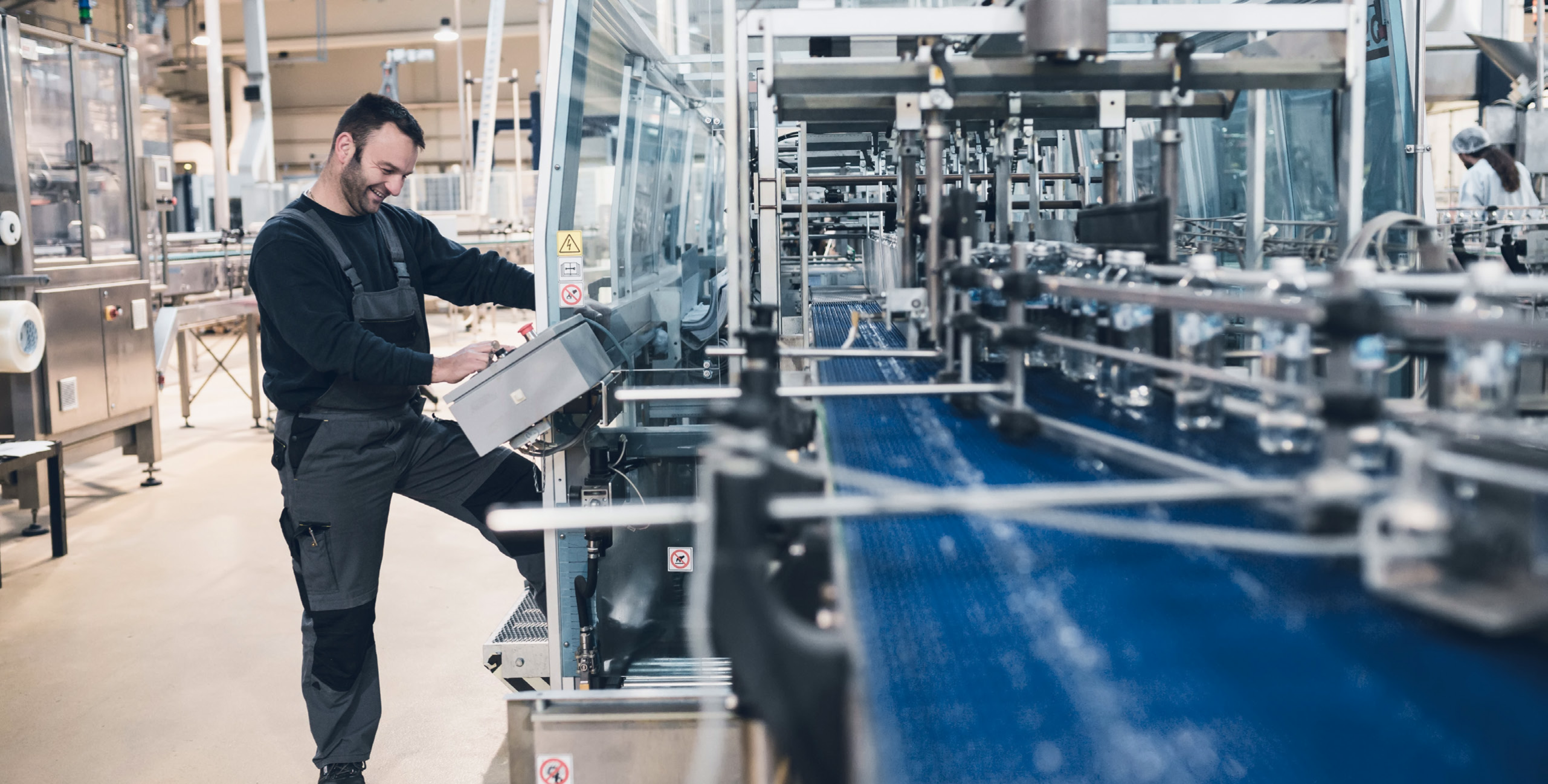
For CPG manufacturers, digital transformation is frequently triggered by a breakdown in how their existing systems support their changing business needs. As a manufacturer, you understand the importance of a well-organized and efficient manufacturing process, with success determined by various factors, including the manufacturing software used to manage the process. An ERP system is insufficient to meet the increasing consumer and competitive pressures on your operations as they become more complex. When attempting to extend your ERP capabilities or develop custom applications to fill gaps, the cost and risk of managing and maintaining those extensions can exacerbate rather than alleviate business challenges.
While Enterprise Resource Planning (ERP) systems have traditionally been the preferred choice for manufacturers, many CPG companies are turning to Manufacturing Operations Management (MOM) systems for a more tailored and effective solution. Manufacturing operations management (MOM) solutions are used to drive operational excellence and bridge gaps that CPG manufacturers face when relying solely on ERP. Connecting the shop floor to sales and demand planning improves resource optimization in various ways, including reduced production costs and time to market. MOM enforces the product design on the shop floor simultaneously, resulting in higher levels of product quality and compliance.
Here are the top 5 reasons why you should consider using MOM for your CPG manufacturing process:
Better Visibility and Traceability: MOM provides real-time visibility into the production process, allowing you to track and trace products from raw materials to finished goods. This helps to ensure that products are manufactured to the correct specifications and helps to identify any issues early on in the production process.
Increased Efficiency: MOM systems are designed specifically for manufacturing, allowing for more efficient use of resources and reducing waste. By automating manual processes, you can reduce the risk of errors and increase productivity. By improving operational efficiency, manufacturers can now accelerate New Product Introduction (NPI), all while ensuring process standardization.
Improved Product Quality: MOM provides advanced tools for quality control, including real-time monitoring of production and automatic quality checks. This helps to ensure that only high-quality products are released to the market, reducing the risk of product recalls and improving customer satisfaction.
Reduced Compliance Risk: A MOM system is designed to ensure product quality throughout its lifecycle. Quality processes are created, enforced, and documented digitally as production proceeds, from formulation to MES to LIMS. Compliance emerges as a natural byproduct of the system. The MES enforces the entire production process based on recipes and packaging design, and the LIMS verifies adherence to critical quality parameters. MES creates complete traceability for all manufactured products as they move through the process, automatically collecting and recording data.
The batch records required by regulation are automatically generated, significantly lowering the cost of compliance compared to manual documentation. Not only are the human resources needed in a manual environment eliminated, but so are the potential errors introduced by manual entry.
Lower Total Cost of Ownership: MOM systems are generally more cost effective than traditional ERP systems, as they are designed specifically for the CPG manufacturing process. This reduces the need for expensive customization and maintenance, resulting in a lower total cost of ownership.
A MOM system is required to achieve manufacturing excellence in CPG
Attempts by CPG manufacturers to use ERP for MOM functions eventually result in inefficiency. Their ERP will become so customized or augmented with spreadsheets and manual processes that maintenance will become unsustainable, causing performance to deteriorate and the inability to move agilely or flexibly in a market that demands it.
When CPG companies embrace digital transformation and use a MOM system to achieve operational excellence, the results can be dramatic. CPG manufacturers, for example, that have implemented Siemens Opcenter have reduced their response times to changes from days to instantaneous and increased operational efficiency by up to 35%.
MOM systems offer better visibility and traceability, increased efficiency, improved quality control, better integration, lower total cost of ownership, and a competitive standpoint for CPG manufacturers aspiring to drive operational excellence.
Find out more about Siemens Opcenter MOM system for CPG by reading this whitepaper.