Managing orders via AX4
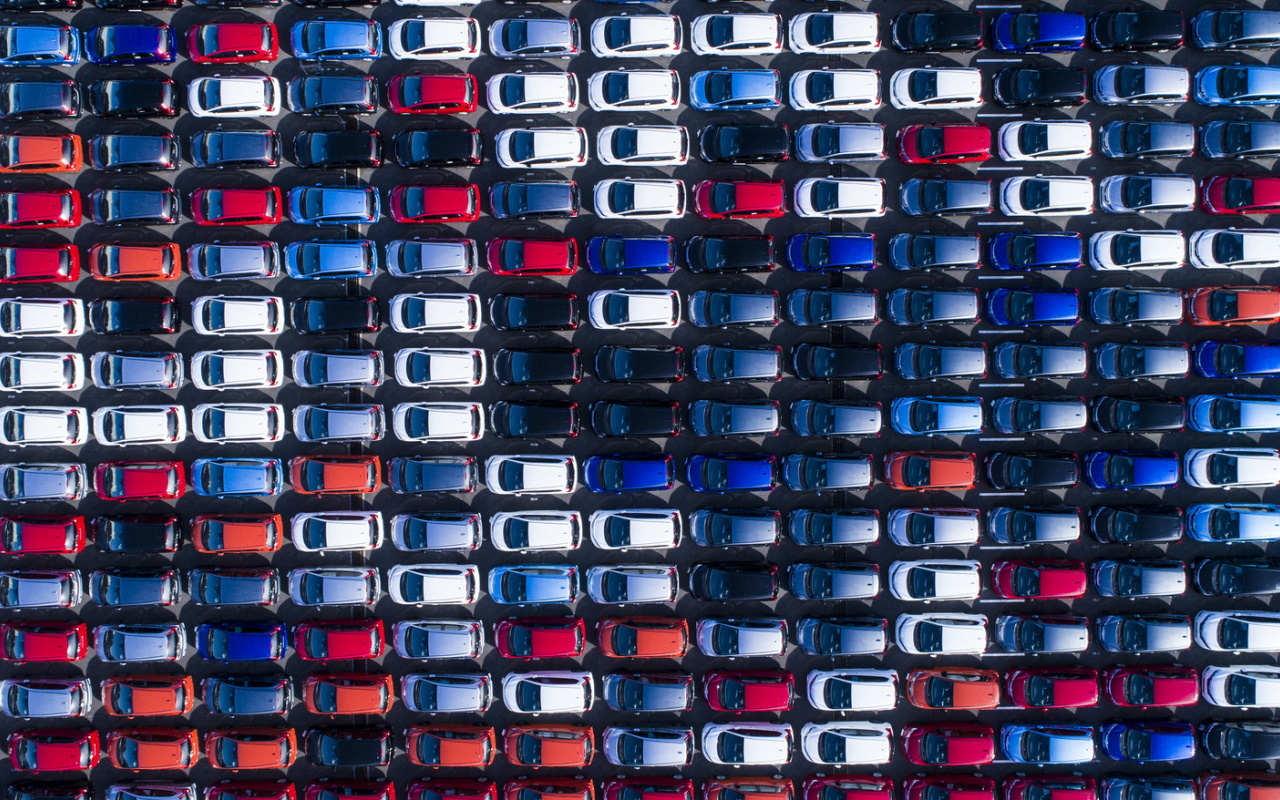
Ford optimizes inbound supply chain
Ford of Europe supports more than 3,300 dealers in over 100 markets from its three spare parts centers in Germany, Great Britain and Spain. With 230,000 parts in the Euro- pean spare parts program, 1,600 suppliers, 24 regional carriers, a material synchroniza- tion center, and 43 inbound consolidation centers around the world, this calls for precise coordination of procurement. The IT platform AX4 serves here as the engine of an automated supply chain from the supplier to one of the spare parts warehouses. The solution makes the internal supply chain transparent to all parties and delivers reli- able, predictable spare parts procurement.
“A transparent, smoothly functioning supply chain is an absolute must in spare parts logistics. The cloud- based logistics platform AX4 delivers end-to-end optimization of spare parts procurement and the easy integration of all essential partners.”
Paul Dennemarck, Manager Transportation, Planning & Process Optimisation Ford-Werke GmbH
Challenge
It used to take a lot of time to calculate prices and freight options for transporting a specific shipment. The problem was that Siemens employees often had to sift through the rate tables of the various freight forwarders, each in its own format and many not even digitized. This made it extremely difficult to find the fastest, cheapest, or most sustainable shipping option. It also meant that many transports were assigned incorrectly or to “mavericks” with whom Siemens had no contract in place.
The idea was to create a smart solution that centralized all key information and could be integrated into the existing Siemens system environment for use by all Group companies around the world. What users wanted was a user-friendly solution that would find the right freight price with a few clicks and could also calculate the carbon footprint of each shipment.
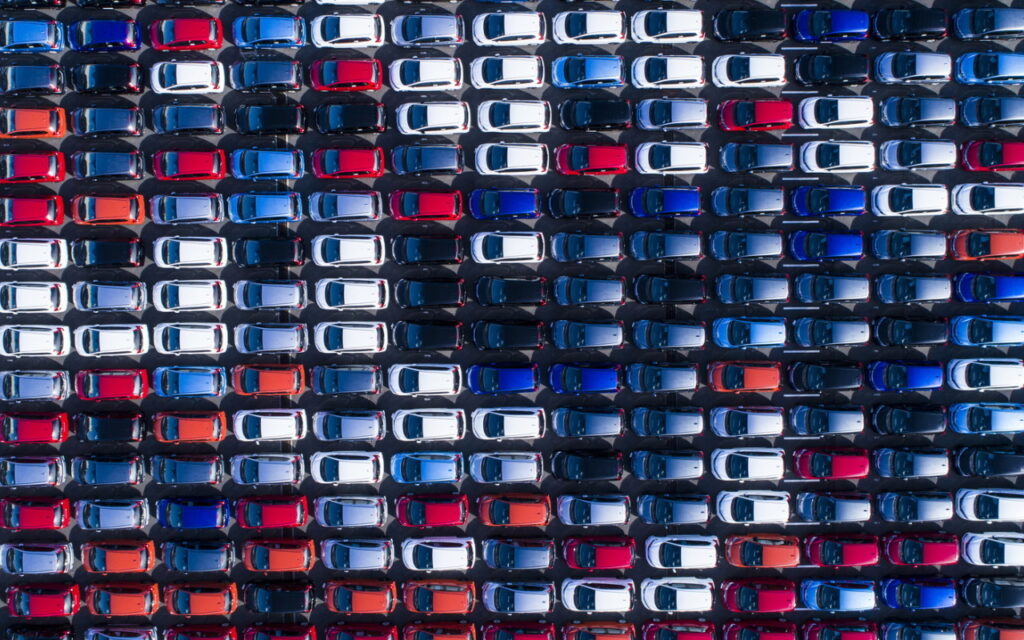
Solution
AX4 integrates all parties into a single network and brings transparency to the spare parts procurement process, including all its various transport options. On the platform, the parties can now use the existing shipment request data and ASNs (advanced shipping notifications) to create barcodes. This ensures that the package is routed correctly in the transport chain and everything goes smoothly when it is received and automatically scanned in at Ford’s spare parts warehouse. In addition, Ford is given a “control tower” with which it can monitor all the processes and zoom in on any particular location if necessary. AX4 also processes the shipping and tracking data that allows Ford to monitor the transport at all times and the supply chain event management feature alerts if any deviations or delays occur.
Success
Ford has a network of some 1,200 AX4 users that handles more than 162,000 inbound spare parts shipments annually. The cloudbased platform offers round-the-clock availability, which in turn improves communications for all parties along the supply chain. The carriers are promptly notified of shipping requests, which improves the pickup process. The transparency in the supply chain and the ability to track goods at any point in the transport chain have led to shortened lead times. Third-party packers and Ford parts warehouses have the opportunity to better plan and prepare for inbound shipments. Rollouts are quick and easy without the need for complex integration projects, since all it takes is the click of a mouse to give supply chain participants access to the solution.