Factoring in the supply chain from the outset
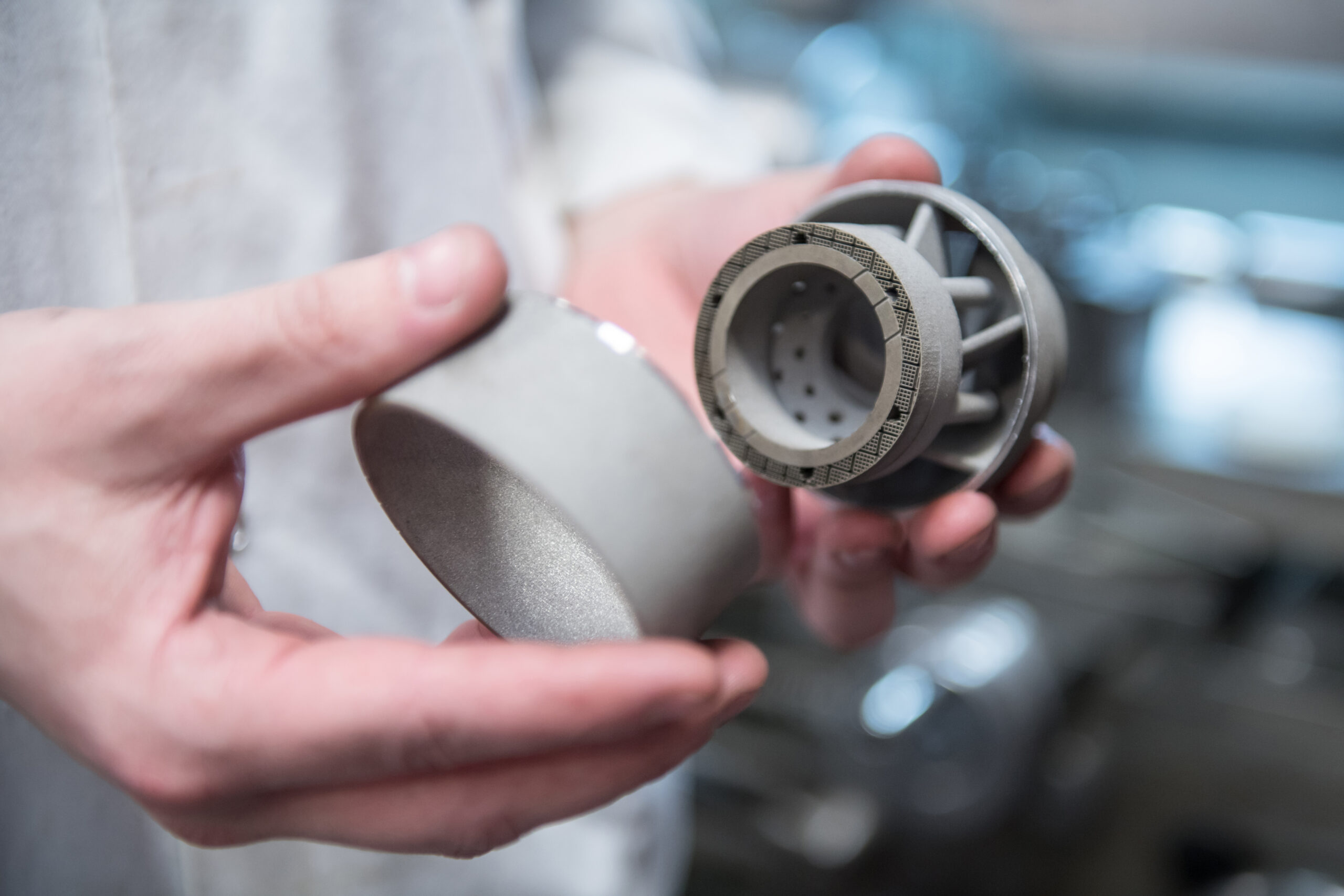
Linking product design and logistics in the complex supply chains of today’s global production networks offers opportunities to combat climate change.
Every product design is, upon closer examination, a blueprint for logistics. It consists of components that have to be replaced after a certain lifecycle. It involves parts that only certain suppliers can provide. It highlights the distance between the supplier and the production line.
Do the semiconductor chips come from halfway around the world or just around the corner? Which components will need to be replaced, and when? What are the possible transport routes? And what are the current options for procuring such parts on the world market?
Design-to-source intelligence renders this blueprint transparent. It makes it possible for supply chain managers to plan capacities long before products are manufactured or parts need to be replaced so they can configure their transportation network and assess how the parts procurement will impact the climate.
At the start of the production chain

Normally, the supply chain begins with the order of a ready-to-ship product, but in this model, the supply chain undergoes a “shift left” to the start of the manufacturing process, right on the heels of the product engineering phase.
The key benefit of this model is that it liberates supply chain managers from simply reacting to unforeseen or unforeseeable events. Instead, they can base their planning on fixed parameters such as the service life of an electronic component or the fact that certain parts can only be sourced from specific suppliers.
This perspective makes it possible to adapt the supply chain design to the product design and plan proactively—even factoring in the sustainability of the transport chain. This could mean drawing on solid product data to develop scenarios that lead to resilient, climate-friendly supply strategies, provide a foundation for new price models, or facilitate the design of network structures that ensure supply chain performance even in times of crisis.
One way to tap into detailed information on electronic components is through the design-to-source intelligence platform Supplyframe. A member of the Siemens family since 2021, Supplyframe offers one of the largest platforms for global electronic component value chains, featuring some 600 million manufacturer part numbers.
The environment benefits greatly from this kind of extensive real-time product information: Are the required components available? What route should they take? And what are the associated costs? The parameters taken into account here extend beyond the term and target delivery date to include the carbon (cost) impact.
Taking material selection, transport route optimization, and waste reduction into account right from the design phase helps businesses make real progress in their shrinking environmental footprint. Integrating environmental indicators into their decision-making processes also empowers them to make informed decisions that help their bottom line and the planet at the same time.
Estimating climate impacts

Digital tools such as Rate Card Management automate administrative busywork. Ideally, they not only enable automated pricing on the basis of existing contracts and offers, they also incorporate carbon costs into the process of awarding contracts, drawing on internationally standardized data such as the calculations from the Global Logistics Emissions Council (GLEC). All key data is maintained, archived, analyzed, documented, and compared—and with the click of a mouse, it can be leveraged to book the right carrier for any shipment.
Simulation tools such as the Digital Twin and software solutions such as the Supply Chain Suite, which pool data from various sources for predictive supply chain planning, can also be used to accurately assess the climate impact of the shift left in logistics. The circular economy, which takes into account the lifecycle and recyclable components of a product, is particularly suited to planning and aligning processes sustainably from start to finish—and back to the start.
Every component a source of information
The results provided by such planning tools not only show the cheapest or fastest route, they also illustrate which route has the lowest carbon emissions and is thus the most sustainable. You can see the detailed shipping process for each option, including every leg, with a distribution of costs and all surcharges.

The shift-left principle brings production and logistics even closer together. Product design itself becomes the key planning factor for ensuring supply chain performance and the sustainability of logistics processes.
Each component becomes a source of information that can be mined to optimize transport and storage processes, and evaluated with an eye on alternative supply structures. Optimizing supply chains and taking environmental factors into account as early as the design phase empowers businesses to not only reduce their environmental footprint but also boost their competitiveness and ensure long-term success.
It’s important to emphasize, however, that design-to-source intelligence is not a static concept. It is a process of ongoing evolution. Future developments in data analysis, artificial intelligence, and digital twin technology will open the door to even more precise forecasting and sustainable decision-making.
If you would like to find out more about “The shift-left logistics imperative”, you should take a look at our white paper https://resources.sw.siemens.com/en-US/white-paper-the-shift-left-logistics-imperative.