The dawn of the gigafactory
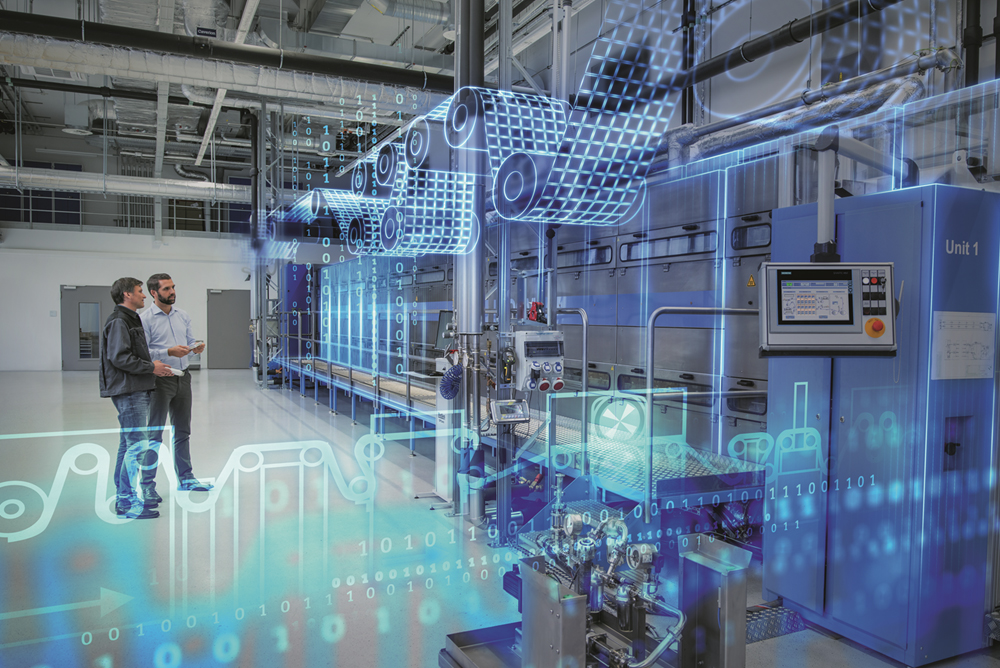
As the world shifts towards sustainable energy, the electric vehicle market is booming. Central to this growth are gigafactories, enormous manufacturing facilities dedicated to producing batteries on a massive scale. These facilities are designed to produce gigawatt-hours (GWh) of battery capacity, underscoring their enormous impact. According to Benchmark Mineral Intelligence (BMI), there are 30 gigafactories planned for continental Europe by 2030, reflecting the rapid development of the industry. Siemens Digital Logistics is at the forefront, providing crucial support to shape the future of this vital sector.
Emerging battery manufacturers face a unique set of challenges, from scaling production to ensuring sustainability. Effective logistics and supply chain management are essential to overcome these obstacles. Siemens Digital Logistics offers expertise and innovative solutions to navigate these complexities and seize the opportunities ahead.
Gigafactory logistics: Siemens makes an impact
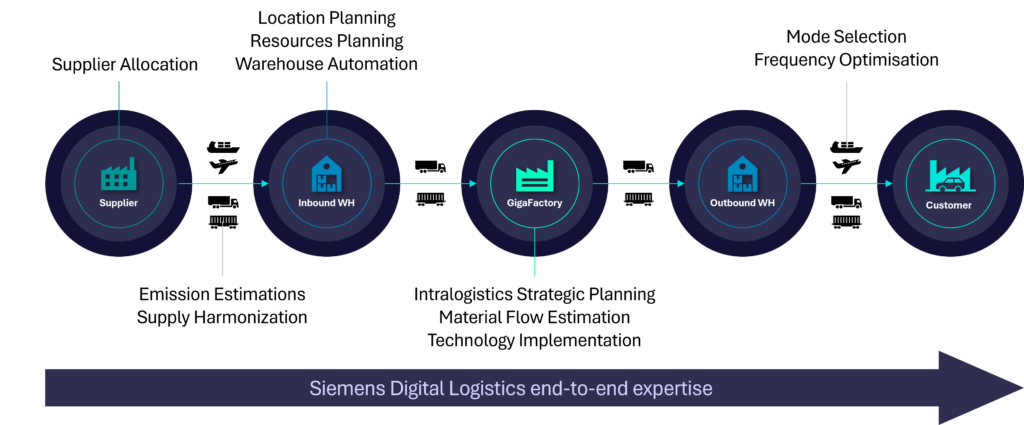
Before delving into our project spotlights, let’s explore Siemens role in supporting the emerging landscape of gigafactories. In the graphic above, you will find a simplified illustration of a battery manufacturer’s supply chain. At each stage of this chain, you will notice areas where Siemens’ portfolio has added significant value to battery manufacturers.
From designing efficient supply chain networks to optimizing intralogistics processes, we provide end-to-end support to ensure the success of gigafactory operations. In the following sections, we will showcase two examples of our contributions in action, highlighting the benefits we bring to our clients.
Project spotlight: Designing a state-of-the-art factory
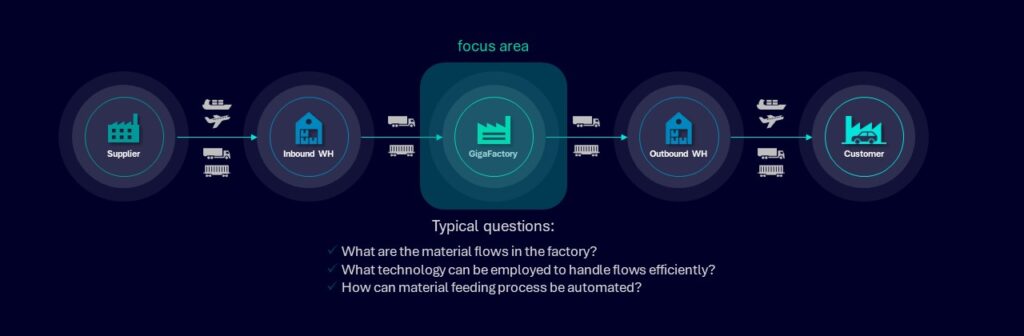
In one of our most recent projects, Siemens Digital Logistics partnered with a future battery manufacturer to optimise intralogistics of a cutting-edge gigafactory. This project exemplified our integrated approach within Siemens; our expertise in logistics was complemented by contributions of two other Siemens divisions: Factory Automation (FA) and Plant Simulation (Plant Sim).
The primary focus was on creating detailed material flow plans specific to the client’s requirements and production roadmap. We used our expertise in strategic planning and optimization to achieve effective integration plan of logistics processes within the factory. This involved anticipating and quantifying material flows thoroughly, including raw material preparation, handover points, and internal transportation logistics. Serving as the main point of contact for the customer, we coordinated with other Siemens experts to provide a cohesive approach.
The Factory Automation team brought their technical expertise in material handling and equipment, such as stacker cranes and AGVs, ensuring that we utilized the latest technologies in planning intralogistics. Our FA colleagues were able to calculate costs of the developed system and offer a turnkey solution, meaning that the client would receive a fully operational set-up ready for implementation.
Meanwhile, the Plant Sim experts played a vital role by creating a digital twin of the plant processes. This digital twin allowed us to validate assumptions, conduct statistical experiments, and ensure that the planned operations would run smoothly.
Together, we successfully answered numerous questions our client needed solutions for. These are a few examples:
- How to quantify material flows in the factory?
- What technology can be employed to handle these flows efficiently?
- How can material supply process be automated?
- How will waste be removed from all areas of gigafactory?
- Can you size the resources needed?
- How can assumed factory processes be validated?
This sort of planning approach offers several tangible benefits for our client. For instance, using our digital twin technology, we anticipate and address logistics requirements before factory construction commences. This minimizes the need for costly changes during the build phase.
The collaboration of experts from different Siemens departments added tremendous value to the project, allowing us to offer a comprehensive planning solution. The integrated Siemens services and software offering provided in this project is not easy to find elsewhere on the market.
Project spotlight: Building a sustainable supply chain network
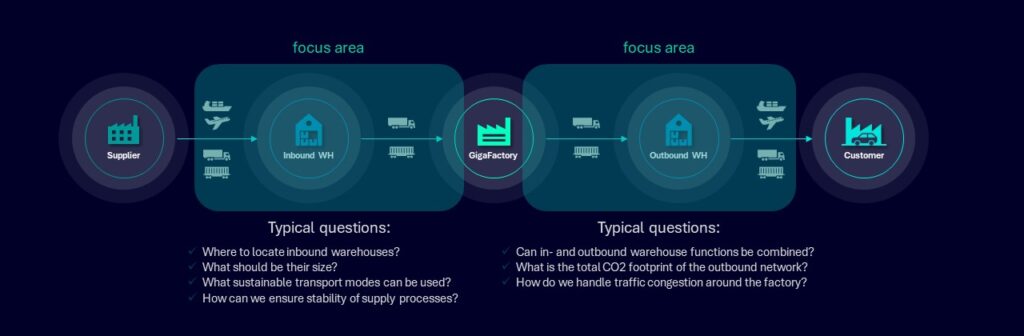
Another unique project involved developing a European supply chain network from scratch for operations of future gigafactories. Starting from a blank slate gave us increased flexibility compared to optimizing existing networks. However, this also meant high uncertainty due to the lack of historical data. To address this, we developed a future volume structure based on the client’s ramp-up plan and derived the logistic flows from it. This approach demonstrates our skill in data analysis and forecasting, resulting in a supply chain aligned with the client’s needs and future growth plans.
We provided our client with answers to the following questions:
- What is the optimal number and location of inbound and outbound warehouses?
- What is their required size and what are the resources (employees, equipment) needed?
- What is the total cost of running an external warehouse and operating required transports?
- What is the optimal shipment frequency?
- What are the consolidation possibilities to reduce costs and CO2 emissions?
- What is the total CO2 footprint of the network depending on warehouse locations and transportation mode used?
Gigafactories, by their nature, require large volumes of materials due to their large-scale production capabilities. This characteristic unlocks the potential for using more sustainable transport modes, such as trains or barges, which we studied and recommended as greener alternatives to road transportation. By leveraging these sustainable transport options, we helped our client significantly reduce their future carbon footprint.
In addition, we created transparency of the network’s carbon footprint, providing detailed insights into the environmental impact of different supply chain scenarios. This transparency enabled our client to make informed decisions that aligned with their sustainability goals while maintaining operational efficiency.
Empowering the Future
As the battery industry continues to evolve, so will the technologies and logistics solutions that support it. Siemens Digital Logistics is committed to staying ahead of the curve and driving innovation, as demonstrated in our spotlights.
While we are excited to share two standout stories, our commitment extends far beyond optimizing factory intralogistics and designing supply chain networks. We are dedicated to tailoring solutions to our clients’ unique needs, empowering them to navigate market complexities with confidence. Each project serves as a valuable learning opportunity, enabling us to expand our capabilities and better serve future clients.
With our expertise and innovative solutions, Siemens Digital Logistics is the ideal partner for seizing opportunities of the future.
The Experts

Junior Consultant
Siemens Digital Logistics
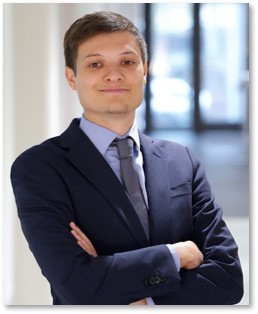
Senior Project Manager
Siemens Digital Logistics
Want to learn more?
Contact Siemens Digital Logistics today to discuss how our solutions can help your business thrive in the face of these new regulations. Learn more about our Consulting services.
More information
Contact us (select “Digital Logistics” as Product)