Clearing the road ahead for automotive E/E innovation
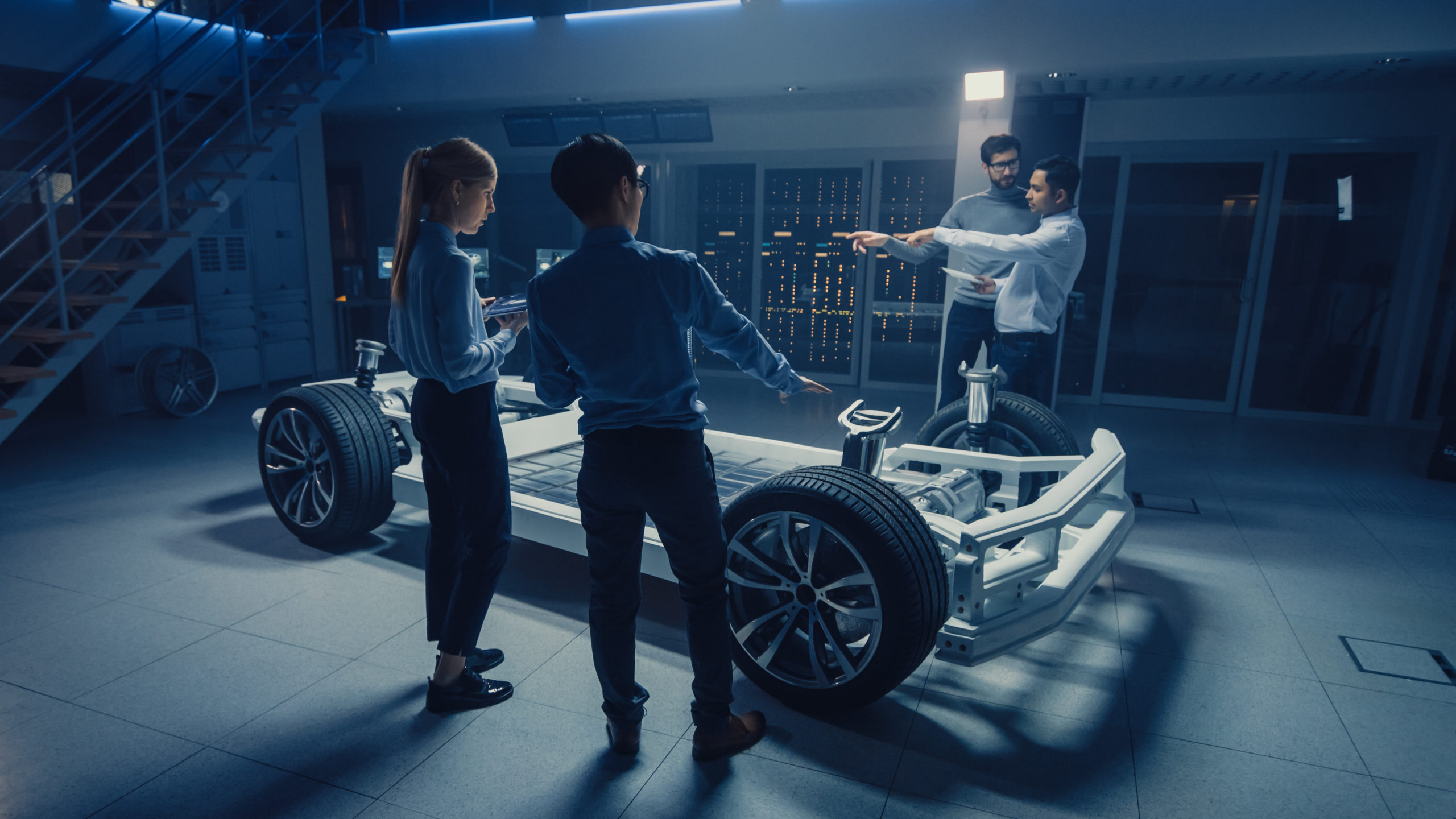
The road forward for automotive OEMs and their suppliers remains lengthy and confusing. While full vehicle autonomy is a popular topic, highly impactful technologies will reach maturity long before true self-driving is achieved. These new technologies will further increase the demands for capability and reliability from the E/E architecture.
The E/E architecture is a convergence of domains: electronics hardware, network communications, software applications, and electrical wiring systems all combine to make up the vehicle architecture. Currently, these domains operate with only limited knowledge of the activities, constraints, and goals of the other domains. Likewise, functional domains, such as powertrain, chassis, infotainment, and others, are often only loosely connected. This can cause significant problems where these domains interact.
For example, several teams within an OEM may be developing software applications for the core ADAS ECU in the vehicle. These teams are organized by feature and work independently. There will be separate teams for the lane departure, active cruise control, and other applications. In order to ensure flexibility for future updates, a constraint caps the processor utilization for this ECU at around 75%. When each of the teams loads their software onto the ECU, they exceed the utilization cap and even the capabilities of the processor. This happened because each of the teams developed their implementations independently and had no ability to understand the totality of the load on the ECU until it was beyond a critical point in the development process.
Automotive manufacturers and suppliers will need to adopt a new, integrated design methodology to handle the interactions between these domains in an environment that is rapidly becoming more complicated. Major automakers are undertaking extensive reorganizations to better align with these needs.
A New E/E Methodology
Establishing an integrated and connected product design, engineering, and manufacturing flow is difficult. These domains have traditionally operated within silos, completing their tasks with minimal external interaction. In addition, the engineering tools in use at many OEMs and suppliers are not built to integrate among domains or share data in a controlled, streamlined fashion. Due to these organizational challenges, engineering decisions in each domain are not being made from a unified set of design data. As a result, errors and incompatibilities are common as cross-domain work is brought together to create the final E/E system design. Some of these may be relatively simple to resolve, but others, such as the ECU example above, result in major re-work efforts, costing time and money.
Many companies have attempted to facilitate collaboration among engineering domains to prevent these errors. Meanwhile, they continue to rely on legacy engineering tools that do not support such collaborative efforts. In particular, these solutions lack a unified data management system, causing engineers to spend time sorting through file systems and manually exchanging information. Design changes, especially those at the system level, are particularly arduous as engineers must propagate these changes to all affected domains and design variants manually.
The adoption of digitalized E/E systems engineering solutions that support the full development flow, from definition through manufacturing and maintenance, will prove critical as automotive manufacturers and suppliers meet the demands of today’s automotive industry while developing the technologies of tomorrow (figure 1). These solutions enable automotive companies to construct comprehensive digital twins of vehicles and subsystems for virtual design and verification. Advanced solutions support data coherency and cross-domain integration throughout the flow while leveraging advanced automation capabilities to improve engineering efficiency. The engineering environment provided by these solutions enables each domain to operate within a system-level context during domain-specific engineering. With a system-level context, engineers can evaluate design alternatives, root out issues, and achieve higher quality designs in less time.

For example, as engineers define the E/E architecture for a new vehicle, they can leverage software models and early ECU abstractions to enrich the vehicle architecture, enabling optimization from the beginning. The robust data model of E/E systems development solutions, such as Capital (part of the Xcelerator portfolio), ensures that each domain has access to the most up-to-date information from the other domains. This helps engineers identify and resolve issues virtually, before they become too costly.
In another example, tight integrations between the E/E systems and mechanical engineering solutions allow the electrical system and wiring harness to be designed with explicit knowledge of the wet, hot, and noisy areas of the mechanical design. Doing so allows the ECAD designer to account for the impact on the electrical performance of these areas when designing the electrical system. On the mechanical side, space reservations can be made and the severity of bends in the harness can be adjusted to account for the wiring bundles that must route through the mechanical structures. With access to this contextual information from the other domain, both electrical and mechanical engineers are able to reconcile incompatibilities between the ECAD and MCAD designs quickly. This integration not only facilitates the development of a product that meets electrical and mechanical requirements, but also accounts for design for manufacturing (DFM) considerations from the onset of the process.
The benefits of digital transformation even extend into the service and maintenance of vehicles. E/E systems development software can automatically create service manuals and signage. These solutions reuse data directly from upstream engineering processes. Engineers no longer need to take data from a spreadsheet and manually redraw wiring diagrams. All the necessary data can be imported and automatically laid out into accurate wiring diagrams. In addition, the generated service manuals are smart, interactive documents that guide technicians through diagnosis and repair processes, and allow technicians to customize schematic views as necessary by VIN.
Change management
Change management is an ever-present challenge in automotive E/E systems development. Changes can be introduced in any functional domain and during any stage of development (figure 2). As changes are identified, they must be communicated to each affected domain, evaluated, integrated, and verified to ensure that vehicle functionality has not been disrupted. The effects of these changes, especially those made at the system level, can be broad. Each change can affect multiple systems, both software and physical, and the unforeseen effects can be very difficult to predict.
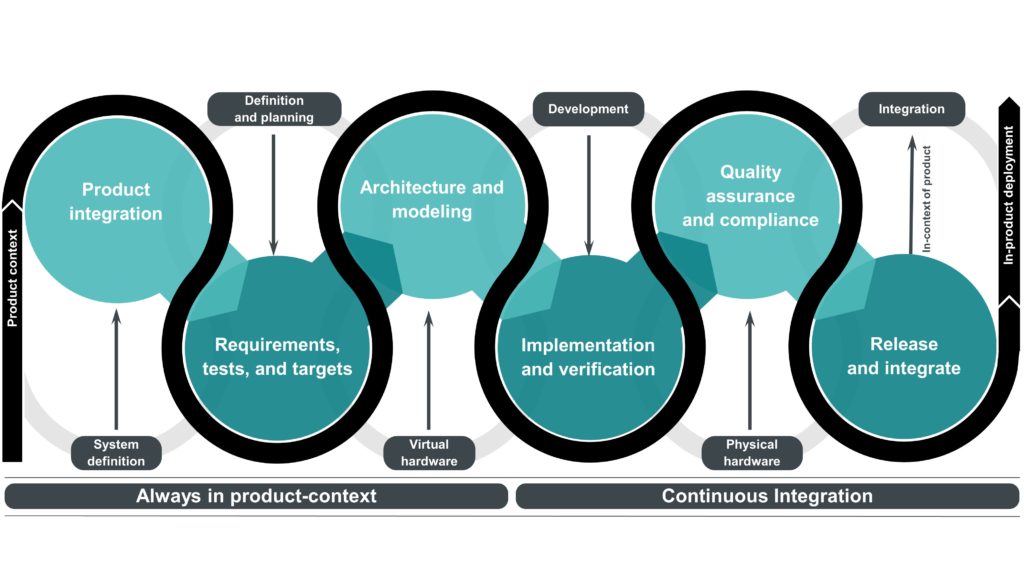
Migrating an ECU to a new location or network in the architecture may affect performance elsewhere in the vehicle. This change in behavior may cascade, causing any number of sub-systems or functions to fail. Such a change can even completely invalidate the technical implementation of the architecture, driving widespread re-design. For example, the type and location of the ECU that governs human-machine interfaces, such as a touchscreen infotainment system, can have dramatic effects on the responsiveness of the user interface. Failing to resolve issues with unresponsive or slow user interfaces can lead to customer complaints and negative brand evaluations from a perceived inconsistency or unreliability of vehicle functions.
Today’s solutions facilitate all aspects of change management from definition, to implementation and review, to effective communication. Detailed change orders can be created within the E/E systems engineering solution, and quickly propagated to all affected designs. Integrated change policies automate control over the flow of changes by determining data ownership and permissions to make changes. The impact of the changes can also be assessed for all buildable configurations of a vehicle, then stored, rejected, or approved and re-applied to any revision in any order. Such capabilities can help companies turn the burden of change management into a competitive advantage by accomplishing it faster and more accurately than the competition.
Read more in our paper: The criticality of the automotive E/E architecture and previous blog post
You also might be interested in: