Developing AV and EV electrical systems with the digital twin
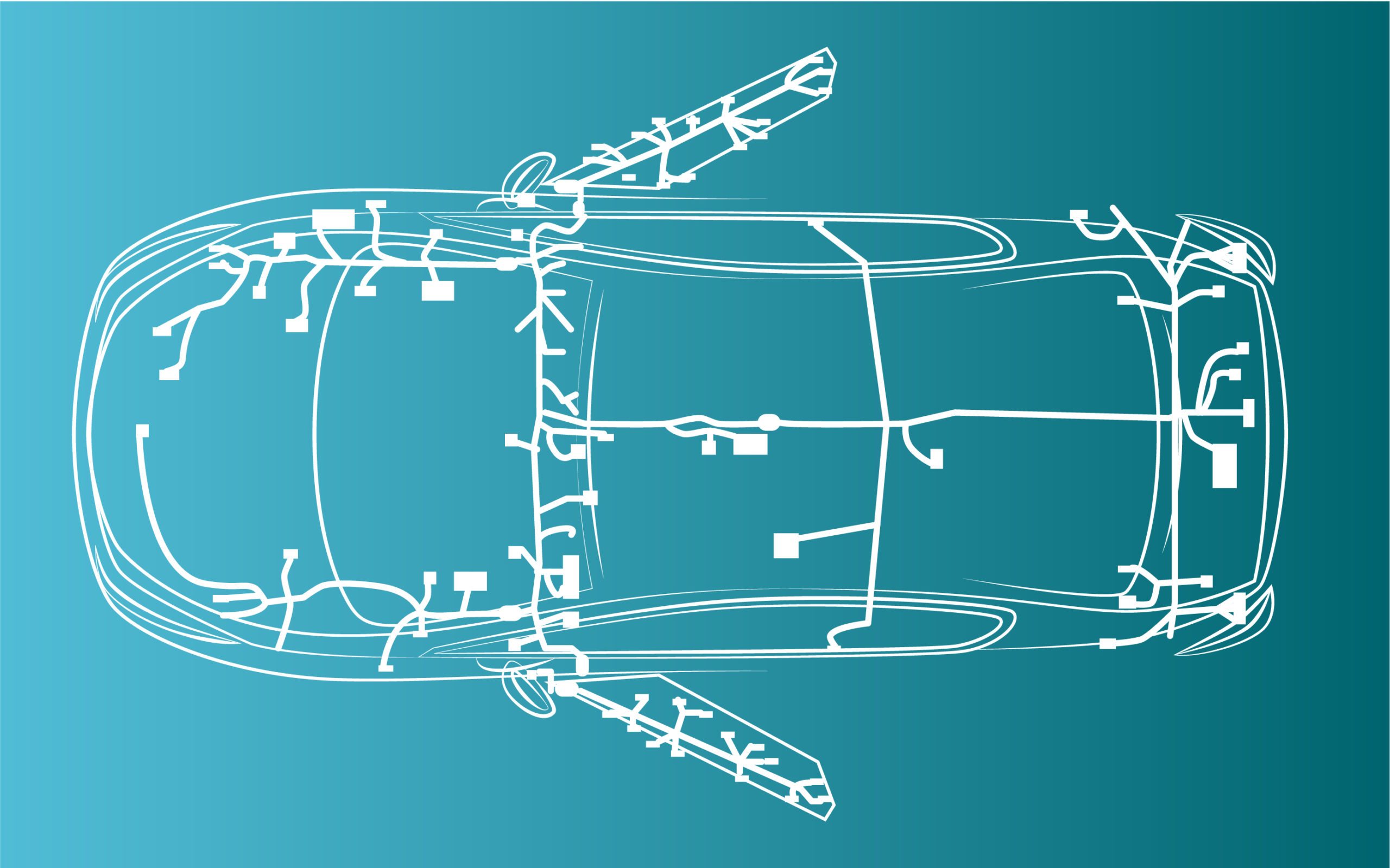
We are living in a time of significant change and disruption in the automotive industry. The amount of electrical and electronic content in today’s vehicles continues to explode as consumers demand greater personalization of products and regular feature updates, and as tomorrow’s technologies such as autonomous and electric drive continue to develop. Meanwhile established carmakers are grappling (and sometimes partnering) with newcomer OEMs and tech companies, while also having to deal with changing ownership preferences, including in my home country of England.
Indeed all firms in the auto supply chain, from the old guard nameplates to Silicon Valley and Chinese start-ups, are facing an unprecedented level of competitive pressure – coupled with new opportunities to gain customers and market share. And all this churn has some very real effects when it comes to how electrical and electronic (E/E) vehicle architectures, which are more complex than ever, are designed today (figure 1).
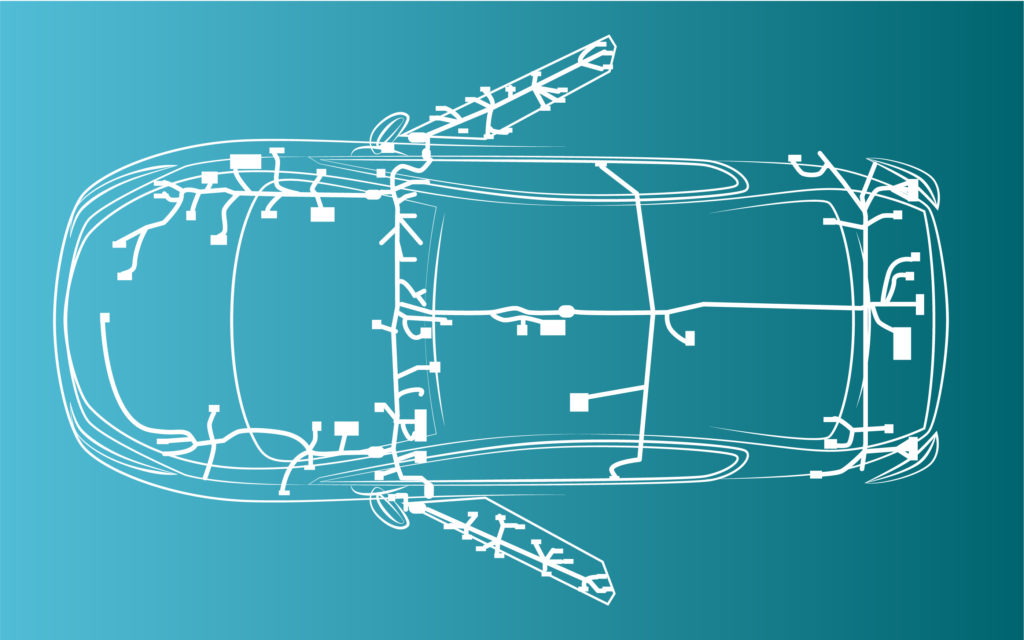
E/E complexity is manifested in the changing nature of network and architecture design. Across a wide spectrum of technical requirements — bandwidth, weight, cost, CPU utilization and so on — manual design processes are giving way to an automated, metric-driven approach. Advanced design tools encourage iteration, building in configurable metrics to help engineers refine the network architecture or design rule checks as they go. Such tools also allow for visualizing the network subnets and overriding parameters such as node-IDs, priority or value tables, which in turn enables further refinement of messages and signals early on in the design process.
Another driving force behind the explosion of E/E complexity is the growing importance of automotive embedded software. The average vehicle today contains around 150 million software lines of code (SLOC), more than double what some experts predicted even just a few years ago. Software has become a critical piece of not only passenger comfort and entertainment features, but also safety systems and basic vehicle functionalities. The ongoing development of autonomous and electric vehicles will only reinforce the importance of embedded software to vehicle functionality, making it a crucial aspect of future vehicle development.
The digital twin of electrical systems
Though software and services matter more than ever, the global auto industry remains a manufacturing juggernaut. Nearly 100 million vehicles are produced annually by an industry that, despite the rise of automation, still directly employs around 9 million people and indirectly creates many times that number of jobs. The process of building cars (and indeed building almost everything else) has been transformed by digital twin tools which mirror the entire value chain, from design and testing through to manufacturing and even service. Siemens has emerged as a digital twin leader, especially for overall product lifecycle management, also simulation and testing of mechanical systems. As just one example of the power of the methodology: Siemens tools helped Maserati put its Ghibli sports car into production in just 16 months, nearly half the usual design cycle, largely by slashing the need for many physical prototypes.
The Capital tool portfolio, with its strength in E/E architecture, systems and network design, complements Siemens established expertise in industrial and mechanical domains. The combined set of offerings enables true multi- domain systems engineering with a comprehensive digital twin, which is an absolute necessity to effectively develop today’s highly integrated automotive products. In particular, the Capital product portfolio, which supports the electrical systems, software, and domains, is an example of how we can transform design capabilities across organizations.
Capital can define system architectures and then, using built-in metrics and design rule checks, compare and contrast multiple potential architectures to ensure the platform design meets the original intent. Using an advanced generative engineering approach, Capital can then automatically synthesize the wiring schematics from the logical connectivity design, taking into account the mechanical constraints. Systems devices are automatically placed, interconnected and the entire wiring system automatically generated using rules and constraints embedded by the OEM into the software. The result is the completion of design tasks that once took months in mere hours or days. Also, critically, the designs can be verified as they are created to ensure they are correct on delivery. Data can be reused across vehicle programs and in the downstream processes of manufacturing and service.
Powerful design tools, like Capital, paint digitized, data-rich pictures of nuanced functional designs that give data on signal, message, part definitions and other attributes. Once this data is captured, it’s that much easier to build robust network, software and platform topologies, apply design rule checks and ultimately create the logical and physical topologies that are the last step before actually generating a physical harness.
To learn more about Capital’s advanced capabilities, and how it can help prepare you for the vehicles of tomorrow, read our whitepaper, Autonomy, Electrification and the Rise of Model-Based EE Design.
You might also be interested in this blog post: Clearing the road ahead for automotive EE innovation