4 Key Challenges of EV Software Development — and How to Overcome Them
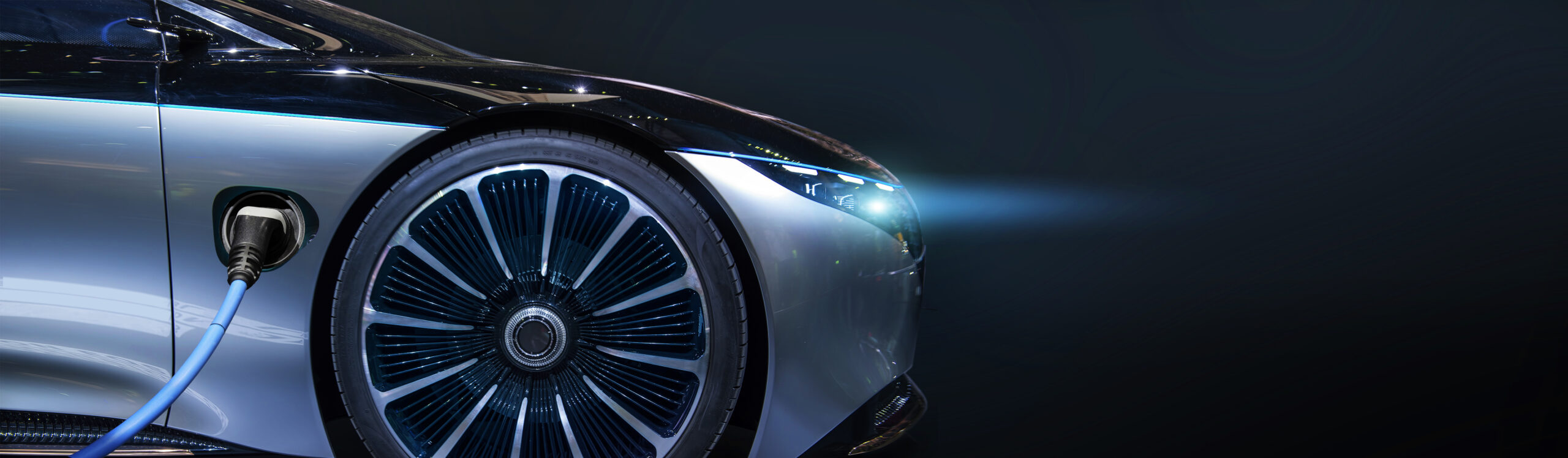
The proliferation of Electric Vehicles (EVs) on roads across the globe has been spurred on by numerous trends. And there’s no sign of it slowing down. Concerns over climate change have added momentum to sustainability issues. The mission to reduce fossil fuels is a top priority for automakers. Additionally, US President Biden signed Executive Order 14057 in December 2021, which, among other things, set a target for the federal government’s fleet of light-duty vehicles to be 100% zero-emission by 2027. Add to that the continuous evolution of EV technology, and you have the ideal environment for accelerated sales.
According to Bloomberg New Energy Finance, EVs will account for 10% of global passenger vehicle sales by 2025. They will account for nearly two thirds of sales by 2040. However, success for automakers in this hot and growing EV market means overcoming the challenges of software development for electric vehicles. What are those challenges? Here are four of the biggest ones — and how software developers can tackle them:
1. Selecting the best system architecture:
Architectural challenges abound in EV software development, because ECU developers must grapple with complexity and integration requirements. Additionally, Automotive Safety Integrity Level (ASIL) qualification is often required for proving the architecture is fail-safe. (ASIL is a risk classification system defined by the ISO 26262 standard for the functional safety of road vehicles.)
Many developers opt to leverage a “combo-box” architecture, where EV functions are combined and integrated into a single ECU. Combining functions — such as the OBC and the DC/DC converter — means you only need one cooling system and one control system. This reduces complexity, vehicle weight and costs. Additionally, using a microcontroller and AUTOSAR stack with multi-core support can help meet ASIL requirements.
2. Ensuring cybersecurity:
Internet connectivity is both a necessity and a curse for EVs, because it opens the door for cyber threats. Connecting to EV architecture such as charging stations or EV supply equipment via USB or WiFi make EVs vulnerable to malware and DDoS attacks. This can put personal data such as payment information at risk. A ransomware attack could result in a hacker causing damage to an EV’s battery pack. Worse yet, it could open the entire grid network to potential attacks.
Developers can mitigate these risks by taking certain precautions and designing ECUs with advanced security features. For instance, a firewall can be used to protect the vehicle network. Transport-layer security (TLS) can be leveraged to protect data in transit between the vehicle, charging station, and the network. Implementing the AUTOSAR BSW secure on-board communication model can protect application data that’s exchanged between peers over the embedded network. Also, a hardware security module can add protection via encryption and authentication.
3. Keeping drivers safe at all times:
Safety regulations for EVs are getting more stringent by the minute. That’s because without proper design precautions, drivers are at risk. For example, the battery management system (BMS), which keeps the EV’s battery functioning properly, must correct issues or isolate malfunctioning battery cells immediately. To that end, fail-safe functions are an imperative. Power inverters must also meet strict functional safety standards. ASIL compliance is key for these components.
4. Accommodating changing protocols:
Along with the evolution of EV technology comes new and evolving protocols for connecting to charging stations that vary depending on the charging station manufacturer, geographic location, and other factors. ECUs must leverage a communication stack to ensure compatibility across all electric vehicle components, to keep drivers moving.
To address these challenges, EV software developers need a platform that provides:
- An AUTOSAR-aware environment for integrating, testing and analyzing software while reducing hardware dependency.
- Support for multi-domain model-based systems engineering (MBSE) that accommodates all the necessary mechanical, electrical, electronics and software components.
- A multicore solution that enables software distribution to address performance and safety challenges of embedded software design.
- Layered, embedded ECU security with features for integrity, authenticity and confidentiality, and support for functional safety use cases for all ISO 26262 defined levels, from ASIL A to ASIL D, and mixed ASIL software partitioning for combo-box implementation.
- Support for the full range of charging communication protocols.
Armed with these capabilities, EV developers can tackle the architectural, safety, security and communication challenges of EV software development with confidence.
Get on the right track with EV development
Siemens Capital VSTAR provides a complete solution that addresses the architectural, functional safety and security challenges of developing a software platform to power high-performing ECUs that drive today’s EVs. Watch our webinar “Electrification: facing challenges and finding solutions for electric vehicle software development,” to learn more about how VSTAR can help you navigate the challenges of EV software development and get on the road to success in the rapidly growing global EV market. You can also learn more about our AUTOSAR embedded software solutions at www.siemens.com/autosar.