A model solution to managing harness complexity costs
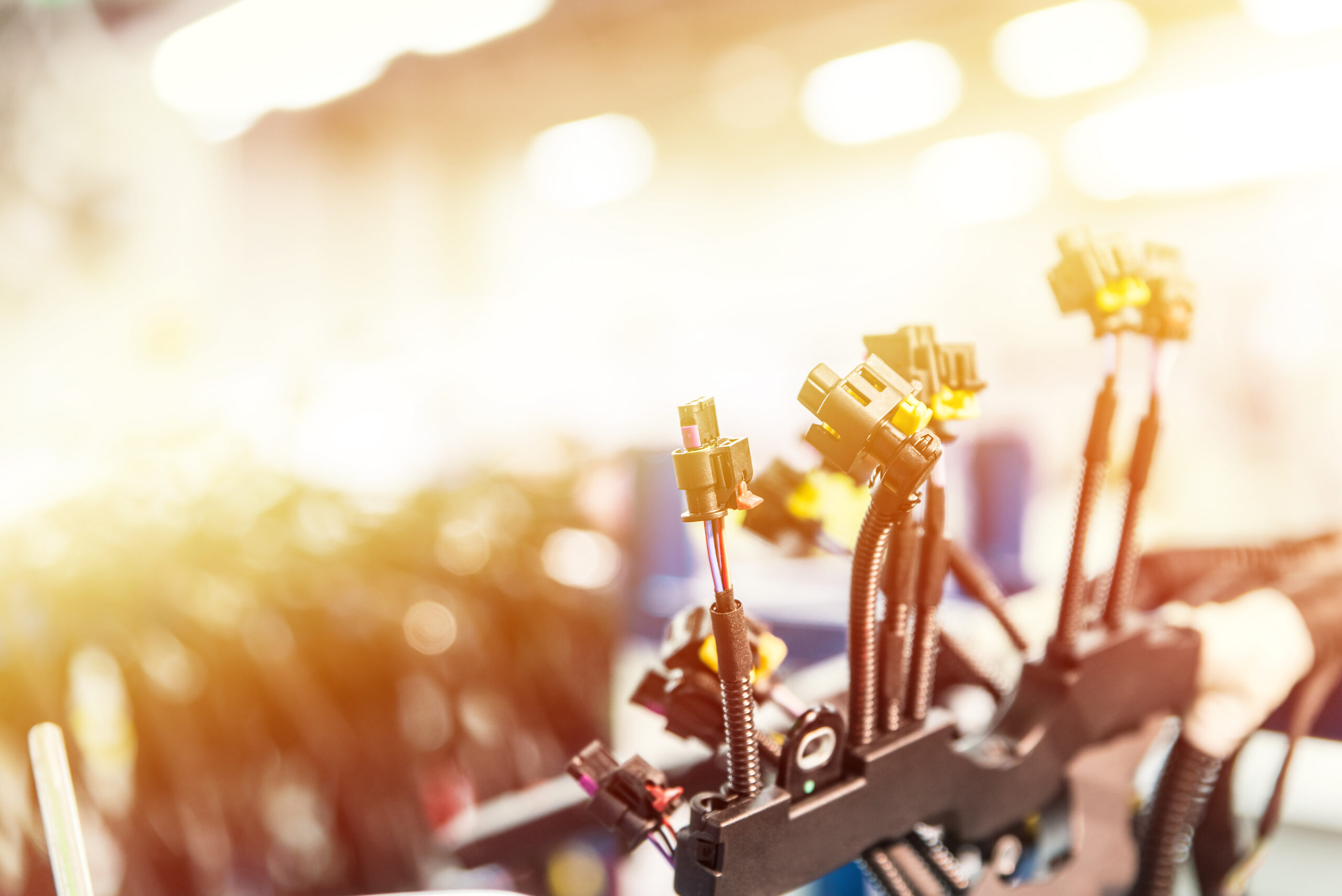
Complexity can have a significant impact on the cost of manufacturing wiring harnesses. But quantifying the cost is difficult, especially when manual methods are used to derive and cost complexity solutions. Traditionally, automotive manufacturers have focused on understanding the piece costs of a wiring harness, and ignored the impact of variation complexity (i.e., the number of harness levels) on the overall costs absorbed by the company. In our previous post, we explored the factors that can drive up harness complexity management costs. Here, we provide a methodology for quantifying and modeling these costs, so engineers can make better decisions to optimize their harness designs.
Characterizing costs: Five questions to answer
Managing harness complexity costs is essential in today’s highly competitive manufacturing environment, where many companies operate under razor-thin margins. The goal in modeling complexity costs, therefore, is to optimize those costs and enable the organization to make better design and engineering decisions. The first step is to characterize costs so that a mathematical model can be applied. Here are five questions that will help jumpstart that process:
1. Penalty or bounding factor?
Costs can either be modeled as a penalty that is affected by harness complexity or as a bounding factor based on some physical reality or business contract. For example, engineering and development costs that grow as the number of harness levels increase are treated as a penalty. On the other hand, a contract between the OEM and sequencing facility that caps the maximum number of harness levels at 20 is a bounding factor, because the contract limits the number of harness levels.
2. What triggers the penalty?
Most commonly, a cost characterized as a penalty will be triggered by the number of harness levels. For example, production costs, sequencing, and engineering and development costs. A penalty cost could also result from the volume of any specific level, which is common for obsolescence costs. Therefore, as the volume of the levels decrease, it becomes more likely that a portion of those levels will have obsolete parts by the end of the year.
3. What is being penalized?
What object or aspect of the harness design is absorbing the cost? Typically, the answer is either the harness itself or individual harness levels. Often, this question is closely tied to the penalty trigger: if the trigger is low volume levels, the harness level will be penalized.
4. What is the math used?
There are two mathematical concepts used to model the relationship between harness complexity variables and costs. The first is “continuous versus step,” which distinguishes between ongoing functions and those that might have steps. For example, inventory costs might have a tipping point or step that will require an additional storage facility. The second concept is “scaling,” which quantifies how costs scale based on the change in the variable. In a direct linear relationship, each new harness level will add a set amount to the overall cost. If it’s an exponential relationship, each new harness level could double or triple the overall cost.
5. What is the risk?
Some costs aren’t guaranteed to actually occur. A mistake is a common example. It’s difficult, if not impossible, to predict when a mistake will happen or the severity of the consequence. A risk assessment calculation is the best method of quantifying costs that will be incurred and spread the cost across each unit built throughout the year (see Table 1).
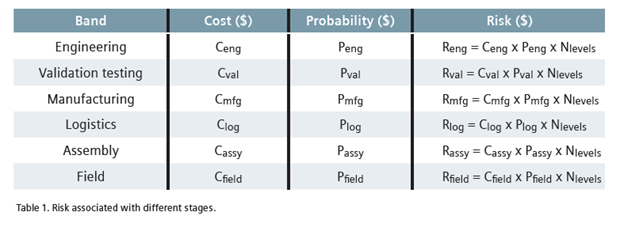
Leverage automation to improve modeling effectiveness
Once complexity management costs have been characterized through the lens of a mathematical model, it’s time to create the model. Some human judgment is valuable to balance model simplicity with model robustness. But it’s unlikely that a human could repeatedly arrive at a complexity solution as optimally as software can.
Automating the process with a solution such as the Capital suite, which is part of the Xcelerator portfolio, the comprehensive and integrated portfolio of software and services from Siemens Digital Industries Software provides the most value. Only a computer algorithm can quickly balance the variables described with testing such a large solution space. Only a digital tool will allow an engineer to adjust a few variables in the model to swiftly arrive at a new complexity solution to fully understand the impact of all of the costs.
To learn more, download our whitepaper, Optimizing the cost of variety in wiring harnesses.
Like what you just read? Check our our recent series of wiring harness blog posts!
- How to improve wiring harness manufacturing efficiency? Let me count the ways
- A tale of two formboards: How to improve merged formboard efficiency
- Building blocks for better wiring harness manufacturing engineering
- Fast and accurate wire harness costing.
- Six factors that impact complexity-related costs, and how to automate for success