Automotive and heavy equipment industries’ role in achieving viable sustainability
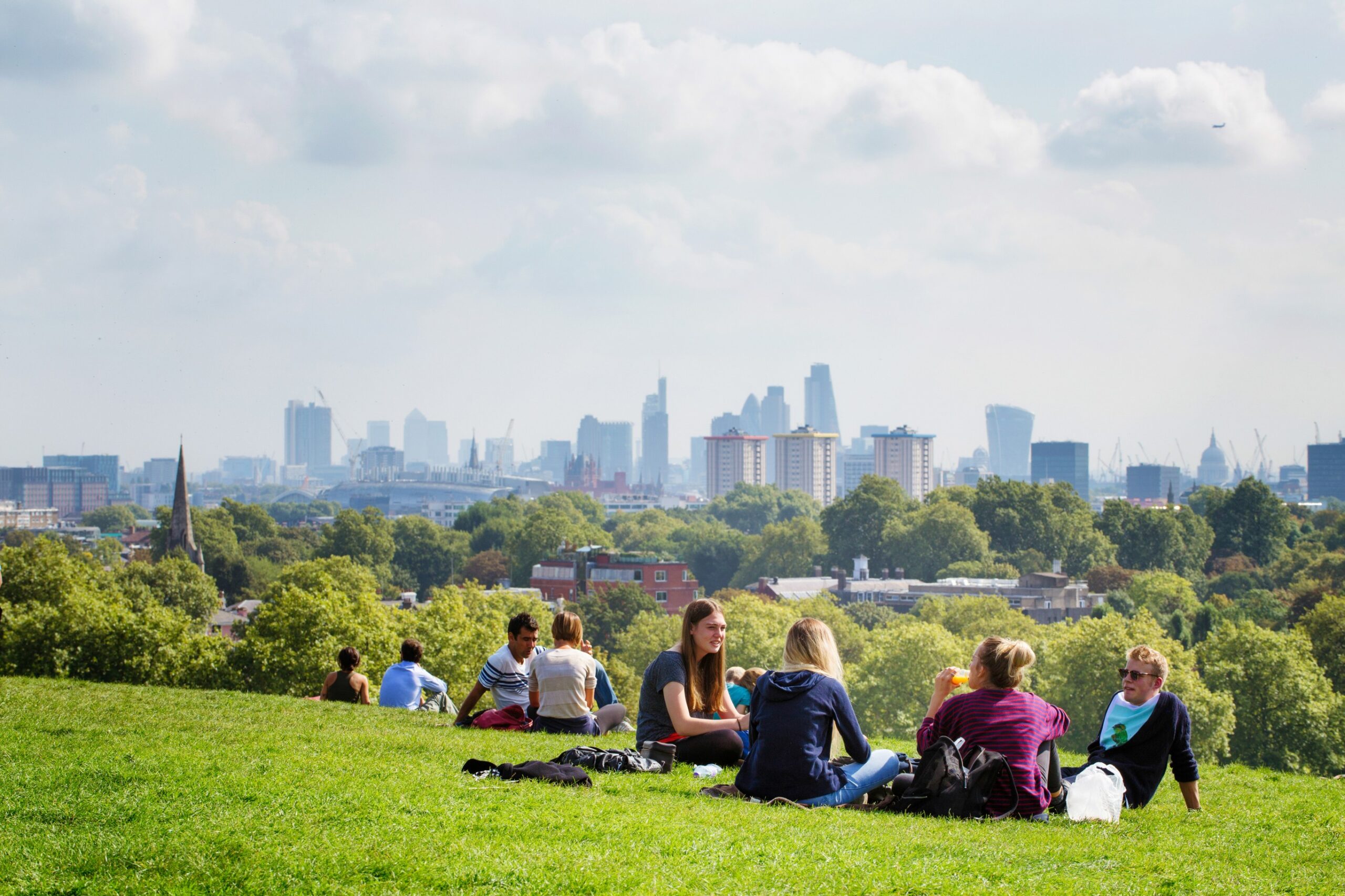
Read what sustainability challenges the automotive and heavy equipment industry face and how the Xcelerator portfolio can enable solutions.
At the Chip to City event in Sweden some of the best industry experts – customers, professors, and Siemens leaders – came together and shared global insights into the challenges that OEMs and suppliers face while transforming our mobility and transportation. One of these experts was Doug Burcicki, Senior Director of Automotive and Heavy Equipment at DISW. With his presentation on the “Industries’ role in achieving viable sustainability,” he showed what sustainability challenges are concerning the industry and how they can be addressed.
Sustainability along the value chain
It is no secret the global mobility sector owns a large share of global emissions. Decarbonizing that sector is only one of many challenges the industry is facing to achieve a more sustainable future. In the focus of that transition stands electrification, digitization and new business models.
The decarbonization of the use phase is addressed by building more efficient electric cars or using alternative fuels. Industry’s role in achieving sustainability, however, goes far beyond only reducing CO2 emissions during the use phase of cars and heavy equipment.
In this post we will discuss two examples of solutions enabled by digital twin technology:
- Designing products and production processes more sustainably and circular
- Operating agricultural equipment more efficiently
Enabling design for sustainability
While the use phase of vehicles accounts for the largest share of emissions, the production phase is the second biggest cause. In sustainability reports like the one shown below (figure 1) by VW from 2021, this is documented under purchased goods and services, which includes all components that were acquired from suppliers and thus their production emissions.
To achieve transparency despite the complexity of upstream value chains, impact data first must be reliably quantified, documented, and shared. While digital twin technology already enables companies to digitally represent product requirements, production and assembly processes; it can also create a holistic overview of the impact that the product has on the environment during its lifecycle. Thus, enabling companies to integrate impact data like the CO2 footprint into their decision-making process and find effective ways to design sustainable products.
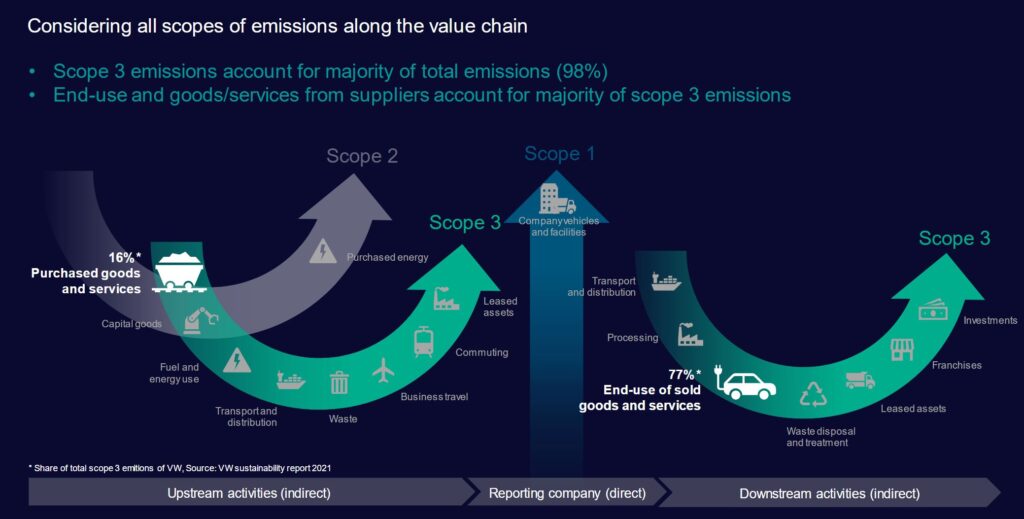
Design for sustainability, like Design for X, is a generic term to describe a design that aims to fulfill a specific purpose. It is important to differentiate between different design goals since a product designed for recyclability must fulfill different aspects than a product designed for cost efficiency or longevity.
CO2 footprint data is needed to simulate the effect, design changes would have on the impact of the product and its processes. Using the example of a car battery, data is generated at each lifecycle stage and can be utilized. Applying digital twin technology to the impact of batteries, enables producers to integrate that data into the design stage of their products and therefore operate more circularly. For instance, data from the use phase could help to create more efficient and long-lasting batteries.
Additionally, performance data can be used to assess the best way to manage a batteries’ end of life (EOL). Depending on their condition, batteries are given a second life. They, for example, are utilized as energy storage. One example being the BMW storage farm in Leipzig. There, second life batteries help with the transition to renewable energy for production plants and decentralize the energy supply for charging stations (figure 2).
Besides the potential to design more sustainable batteries, transparency itself is another driver for a digital “impact” twin. From 2026 on EU regulation will call for a digital battery passport, which requires, among other things, the declaration of a carbon footprint.
As of today, the Xcelerator portfolio enables customers to create digital twins of almost every lifecycle stage of their products. To realize a digital twin of the CO2 footprint, the BOM and BOP , associated with the design is imported into Teamcenter from Capital. There, a database that contains CO2 Footprint data for materials, machines, and production processes creates a CO2 Footprint for a product before it is produced or prototyped.
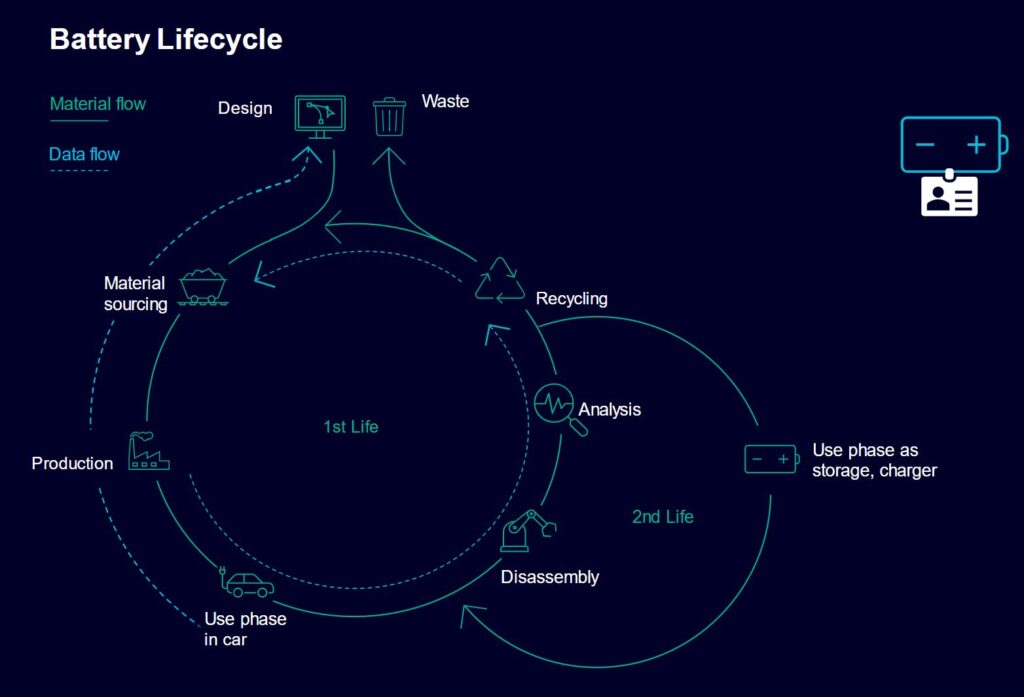
Enabling Smart Heavy Equipment in Agriculture
Agricultural production accounts for 39% of food-related emissions and faces the great challenge of having to reduce emissions while becoming more productive to feed a continuously growing population with limited land and water resources. With digital twin technology, farmers can create a holistic digital overview of their farming equipment as well as their land to increase their yields, reduce water and pesticide usage and prevent damage to crops. Monarch tractor, for example, is increasing flexibility and efficiency through autonomously operating farming equipment and utilizes IoT and data collection to make farming processes smarter.
Learn more:
- Check out the Chip to city event homepage here
- Read the article A simulation approach for autonomous heavy equipment safety which describes more in detail how Simcenter enables Monarch tractor to build their autonomous trucks.
- Stay tuned for our upcoming whitepaper on sustainability. It will closely look at the importance of digital twin technology in enabling an impact digital twin. Reliably quantifying and tracing the environmental impact products and processes have, to make better design decisions throughout the value chain.
Monarch Tractor blog post: