Printed Circuit Podcast: Siemens’ Erica Van Berkum Explores E/E co-design best practices for automotive & aerospace cables and harnesses
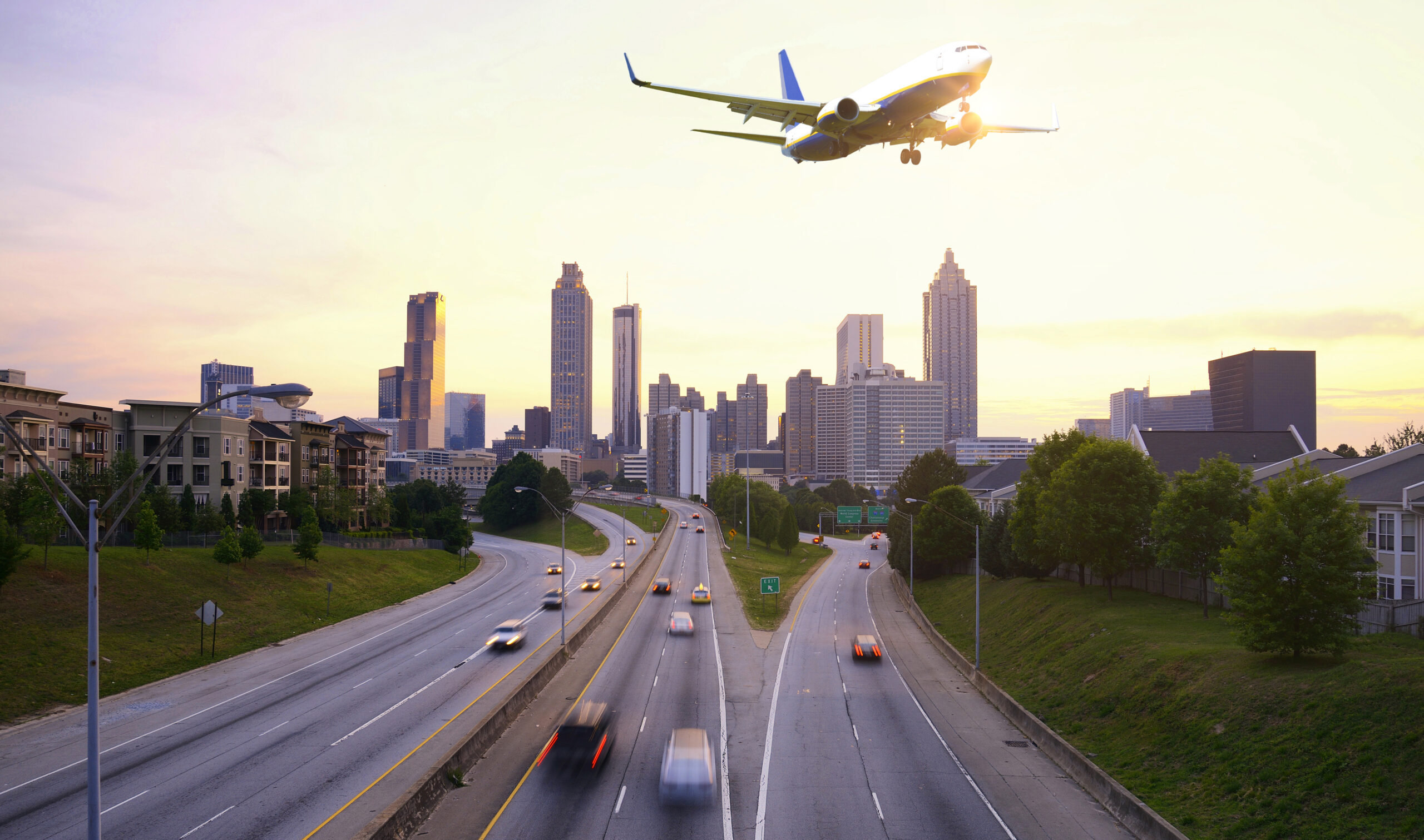
Meeting new challenges in the automotive and aerospace harness industry requires innovative design approaches that rely heavily on effective E/E co-design and collaboration, and the ability to share and access data quickly and securely. Designers of cables and harnesses need to manage increasingly complex systems, limited space and the growing demand for lighter materials to improve fuel efficiency. They must also ensure high reliability and performance in extreme conditions. Meanwhile, time-to-market pressures and rapidly evolving technology means designs must be highly adaptable, while complying with stringent regulations and const constraints.
During a recent episode of the “Printed Circuit,” the podcast that explores trends, challenges and opportunities across the printed circuit engineering industry, host Steph Chavez took on the topic of electrical/electronic or E/E co-design for cables and harnesses. He invited Erica Van Berkum, Technical Product Manager for Siemens Capital electrical connectivity, to join in the discussion and shed some light on best practices that will help design teams take collaboration to the next level.
Breaking down silos with E/E co-design
Van Berkum began her career over 20 years ago in wire harness design at Yazaki, the world’s largest harness supplier. She also worked at Nissan in various roles in electrical and vehicle program management. Van Berkum has been with Siemens for over five years, helping customers execute large scale deployments of Capital, Siemens’ integrated electrical software system. Most recently, she’s been part of the Capital product management team representing the connectivity domain.
According to Van Berkum, one of the key challenges for electrical or electronic designers is that teams must work in silos. “This causes a lack of visibility of changes, both upstream and downstream in the design,” she said.
For example, if a mechanical engineer makes a change to a component or moves a connection point to a harness, it impacts routing, wire length, voltage drop and other variables. “The information isn’t coming as consistently or as frequently as it should, and it’s difficult to understand how requirements are implemented across different domains such as electrical, mechanical or software,” she said. “How do you get those teams to communicate effectively with each other? What’s the overall performance look like, and how do we break down those cycles?”
Overcoming the challenges created by working in silos is critical for accelerating design cycles, minimizing error, improving quality and delivering innovative products to market at the speed of business. The first step, said Van Berkum, is using the right tools. “You really need to visualize and understand the implication of requirement changes on downstream designs like electrical and electronics,” she said. “That traceability is vital for safe and secure E/E systems designs.”
Performing architectural trade studies is also really important, because it enables teams to understand the system implications of change. “When implementations are done at the design level, how do you propagate and feed those back into the architectural design?” asked Van Berkum. “And how do you do that sooner in the design process?”
Welcoming change
Unfortunately, legacy approaches to systems design inhibit the speed and effectiveness of such communication between engineering domains – and change isn’t easy. Engineers have grown comfortable with the systems they have in place and are reluctant to adopt new ways of doing things. “They don’t want to pay for it, and they don’t want to be the guinea pig,” Van Berkum said. “Nobody wants to go first.”
However, Van Berkum believes that change is possible when the value proposition is clear. “If leaders are communicating that change will result in 5-10% growth, and if they communicate they’ll be patient with their team if productivity dips as they adopt a new solution, then success is possible,” she said, adding that Siemens’ customers who are doing proactive training and pilot programs are making progress.
The digital thread changes the game
Van Berkum said that whether the industry is automotive, aerospace or another, everyone is trying to do the same thing: Shorten design cycles. “When I first started my career in automotive, our design development cycle was maybe four to six years for a vehicle design, and now we’re at about a year and a half to two year,” she said. How did that happen? “You have to have a digital twin and a shorter feedback cycle.”
With a digital thread, it’s possible to lock in requirements from customers and facilitate co-collaboration between disciplines and domains, and that’s what Siemens brings to the table. “Siemens Capital has a great solution, and what I like about Capital is that it does exist really well and integrate well with our tools in the Siemens Accelerator, with other MCAD, or ECAD or PLM systems,” Van Berkum said. “We have a lot of tight data integrations and bridges to other tools, as well. Our solution enables teams to eliminate manual entry and reuse data, so they spend less time in the tool and make fewer errors.”
Chavez pointed out that Siemens Capital enables all stakeholders to see changes to the design – or the potential for change – instantly, and address those changes on the fly. “You can conduct ‘what if’ scenarios and allow the full team to react instantaneously,” he said – and that encourages all of the teams to think not just about their components but about the system as a whole. It also improves traceability, enabling teams to understand why certain changes were made and keep a digital record of those decisions.
When it comes to applying these best practices, Van Berkum said are only subtle differences between aerospace and automotive E/E design. “Aerospace designers work with massive, super long cables, whereas automotive design is more compartmentalized,” she said. “Both are leaning toward a generative design approach. What can they do that’s more automatic, more intelligent, and less manual? And how can they reuse data? These are the key challenges in both industries.”