How to improve wiring harness manufacturing efficiency? Let me count the ways
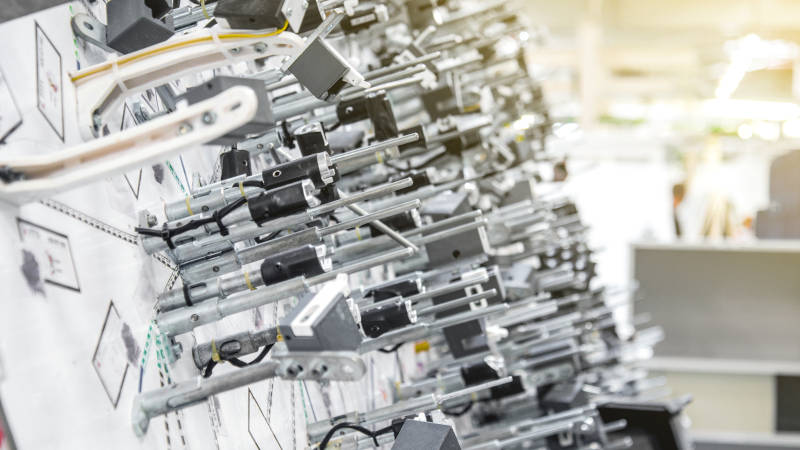
Wiring harness manufacturing is complex, time-consuming and often inefficient. Part of the reason is that traditional electrical and electronic (E/E) system wiring harness design processes create silos, inhibit collaboration and block data sharing. Harness manufacturers also work under tight time and budget constraints from OEMs looking to reduce their own manufacturing expenses. After all that, Covid-related supply chain shortages drive up prices. Did we mention that 80-85 percent of a wiring harness is still handmade?
But there’s some good news. A new generation of automated E/E system design tools is helping engineers tackle these challenges much more effectively. This is resulting in streamlined harness design cycles, improved product quality and optimized formboard layouts. Let’s take a look at three.
1. Reducing harness design cycle time and cost
Product subassembly design is a manual process that can be extremely frustrating. New E/E system and wiring harness engineering solutions feature production module assignment algorithms that identify and configure manufacturing subassembly modules. The algorithms use predefined best-practice rules to allocate production modules, so they increase manufacturing efficiency and reduce cost. At the same time, these new tools simplify the creation of bill-of-materials (BOM) by automating the calculation of wire lengths. Also, it can include splice positions and taping quantities. It then applies appropriate wire types, multicores, terminals and other elements based on engineer-defined rules.
2. Improving product and process quality
Managing change is a constant battle during E/E system and wiring harness engineering. Modern software tools use robust data integrity and automation to make change management faster, easier and less prone to errors. Engineers can create multiple policies to control how the tools respond to changes and ensure that manufacturing data added to early design iterations is retained throughout the design process. The software assesses the design change impact and provides intuitive outputs that can be used to validate that changes were implemented as expected. The rich data models also support digital continuity within each design and manufacturing process (see Figure 1). Data from the design environment flows directly into the harness production environment with no duplicated data entry.
3. Optimizing formboard layout and design
Well-designed formboards are critical to engineering efficiency, reducing the time and effort needed to place each component in the appropriate zone. But discrepancies between design intent and physical parts often occur due to outdated manufacturing diagrams. These discrepancies waste materials, increase costs and delay production. Automated wiring harness software solutions enable engineers to generate full-scale diagrams directly from the engineering environment. Changes made in one diagram are updated in related diagrams, eliminating a common source of errors. To ensure best-practice manufacturing engineering, fixtures and other manufacturing elements can be selected and placed interactively or with rules-based automation. Formboards can be merged or combined, as well as split and organized to show only the relevant subassemblies for any given part of the production line. The results are better shop floor decisions and increased profitability, with some users reporting an 85% improvement in formboard design time.
Clearly, legacy methods of wiring harness manufacturing are proving insufficient in today’s competitive engineering environment. Fortunately, a new class of automated E/E system and wiring harness engineering solutions, including Capital from Siemens Digital Industries Software, is driving improvements in design processes, data integrity and collaboration throughout the development cycle. This digital transformation is vital to grow revenue, increase profitability and ensure your future success. To learn more, download our new whitepaper 10 ways to improve wiring harness manufacturing.
Looking for even more?
- Learn about one of the most desired solution to complex harness design in out our white paper Tackling harness complexity with KSK!
- Also, check out how to manage unexpected costs of wire harness manufacturing including rework, obsolescence, premium freight and manufacturing inefficiency – otherwise known as 4 Horsemen of wire harness manufacturing!