Electrification, autonomy and electrical system design
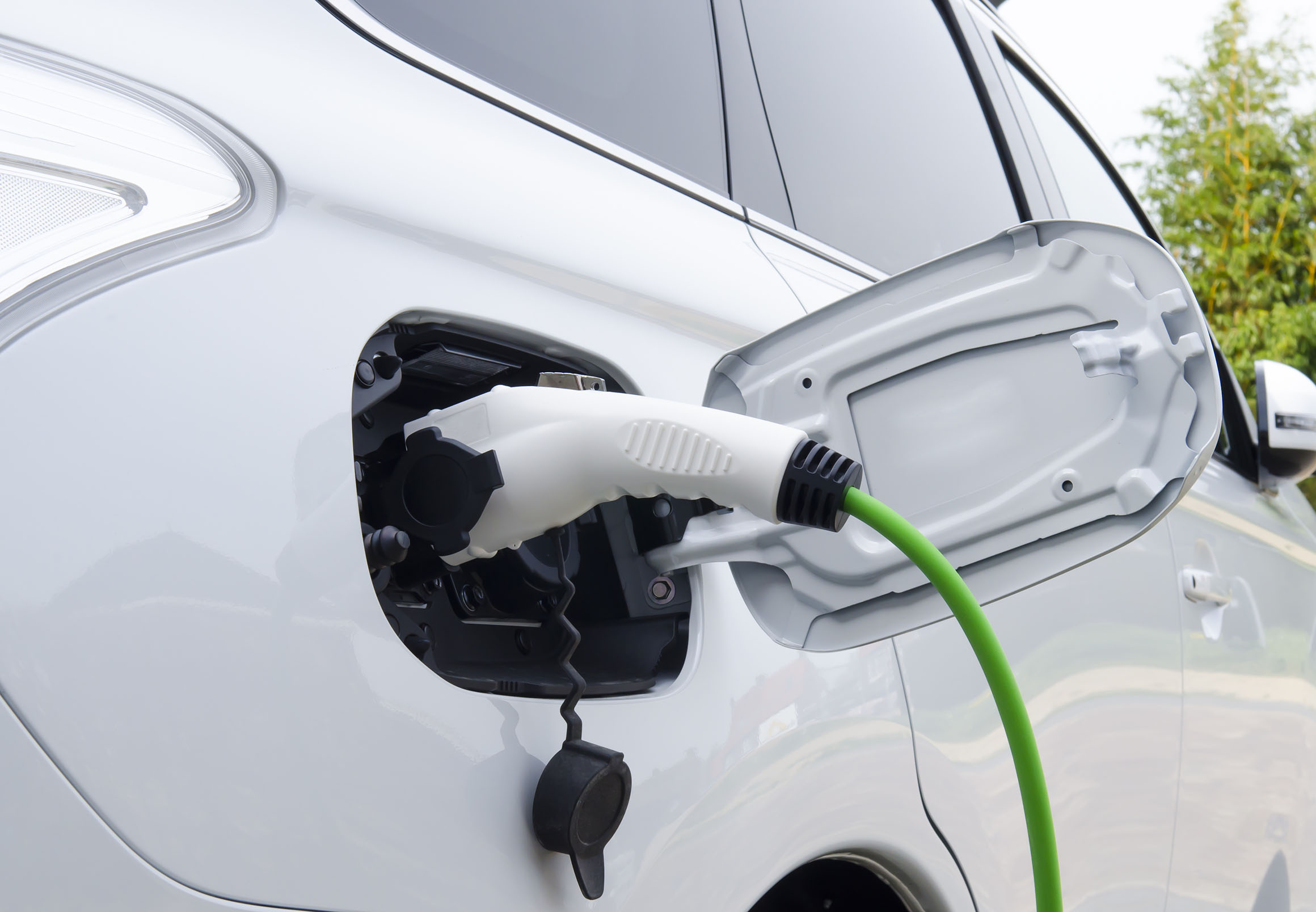
Conventional wisdom has it that over the last decade or two, the global auto industry has undergone waves of disruption, each larger than the last. First was the rise of China as a major vehicle market (now the world’s largest in terms of both demand and supply), second was the introduction of mainstream hybrid-electric vehicles and last was the rise of autonomy and mobility services.
Still, autonomy, especially full Level 4/5 mostly hands-off driving, remains a number of years away. Despite ample marketing noise and news coverage, autonomy has entered the well-known “trough of disillusionment” as described by Gartner. Indeed of late, self-driving stories have seemed to focus on more modest applications like shuttles operating at relatively low speeds in geo-fenced areas.
This is not the case when it comes to electrification. If anything, vehicle electrification is accelerating, impacting product development and the work of EDS design teams today (figure 1). Much of this rush to market and consequent pressure on product development times is now driven by fear of being left behind rather than by trying to be a first mover.

Given the accelerating trends of vehicle electrification and autonomy, carmakers and suppliers are evaluating their EDS processes and tools with renewed scrutiny. Old interactive processes are inadequate to move as quickly as is now needed, which is leading organizations to invest in high levels of design automation and virtual validation. Furthermore, traditional methods and tools are poor at facilitating collaboration between domains, an increasingly critical facet of vehicle development.
Multi-domain design and safety
In particular, electric vehicles require a greater focus on true multi-domain system level design. A simple example is regenerative braking. The addition of high power electric motors, power electronics and high-capacity battery storage means that braking systems now have to consider the dynamics of high-power electronics, motor characteristics, battery electrical safety and cell chemistry to understand and manage the capturing of braking energy.
The design of this system requires a new level of close integration between mechanical, electrical and thermal domains. It is therefore necessary to have true multi-domain data exchange between engineering software tools to inform the system design from an early concept stage. At the most progressive automotive OEMs, thermal, electrical and mechanical designers work increasingly closely together when designing vehicle systems, including electric powertrains, as each of their ‘independent’ decisions significantly impacts the others (figure 2). (You can read more about that in our whitepaper, titled “Automotive ECAD-MCAD Co-Design Leads to First-Pass Success.”)
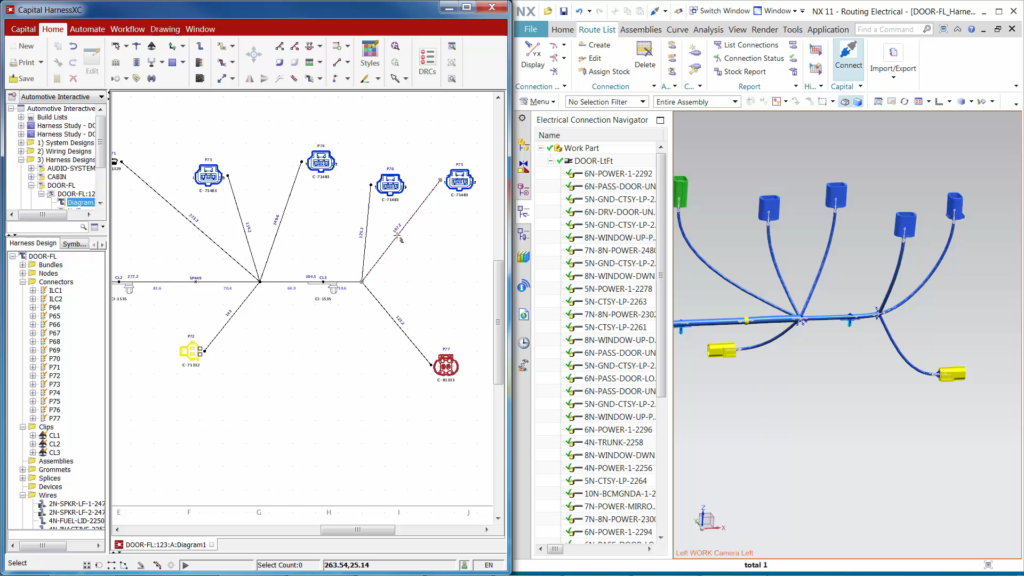
Siemens’ Capital product portfolio, which supports the electrical systems and network domains, is an example of how we can transform design capabilities across organizations. Using a model-based design paradigm, Capital can define system architectures and then, using in-built metrics and design rule checks, compare and contrast multiple potential architectures to ensure the platform design meets the original intent. The tools can then automatically integrate the electrical systems to be incorporated into a representative topological layout of that vehicle. Systems devices are automatically placed and interconnected, and the entire wiring system is automatically generated using rules and constraints embedded by the company into the software. The result is design tasks that once took months can now be achieved in hours or days. Critically, these designs can also be verified as they are created.
Forward-looking automotive manufacturers and suppliers are adopting these approaches to give them a competitive advantage in this increasingly competitive world. The capabilities provided by an integrated electrical systems engineering solution such as Capital will enable companies to take the lead when dealing with the interwoven technical and business challenges of tomorrow. As part of the Xcelerator portfolio, Capital can also integrate with industry-leading simulation and lifecycle management solutions, helping companies create comprehensive digital twins of their products.
Learn more in our whitepaper How vehicle electrification impacts electrical system design. Or, you can visit https://www.sw.siemens.com/portfolio/ to read more about Xcelerator.