Why EV manufactures turn to Siemens Capital software for E/E systems development
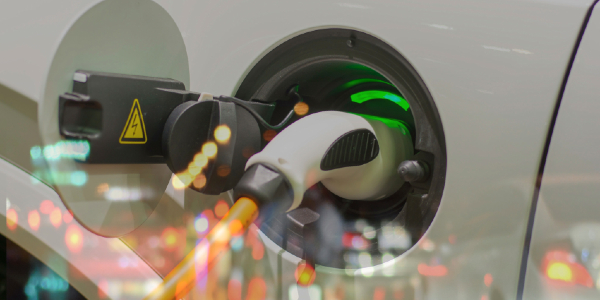
At any given moment demand for Electric Vehicles (EVs) continues to grow globally. According to Strategy Analytics, 3 million units of plug-in light EVs were sold in 2020. Europe nearly doubled its market share to 26% in the first quarter of that year, making it the leading region for EV sales growth. EV sales sit at around $800 billion today and are projected to outpace traditional vehicle sales over the coming decade.
Download our infographic for more market statistics.
Not only is EV adoption up, electric/electronic (E/E) complexity is also skyrocketing. Today’s EVs have, on average, more than 3,000 wires to support a plethora of new features and functionality. That’s more than 2.5 miles of electrical harnesses with about 750 connectors, weighing roughly 60kg. Keeping pace with such complexity creates significant challenges for automotive manufacturers and suppliers in terms of cost, performance, and weight management.
The need for speed, safety and cybersecurity
The trend toward software-defined vehicles opens the door for innovation and market differentiation, and automakers are racing to beat each other to the punch with features that delight customers and trump competitors. Software now dominates and defines the way the modern vehicle is configured and characterized, enabling a wide variety of features that are scalable and updatable via over-the-air updates.
And although time to market for next-generation features and functionality is a top concern in the highly competitive automotive industry, that’s not all automakers worry about. Other key considerations include ensuring functional safety, as well as keeping the vehicle’s weight down and its performance high. As vehicles become increasingly network-connected, rock-solid cybersecurity is essential, and interdependent systems must work in sync, despite different voltage requirements and dependencies.
Meeting these requirements calls for clean-sheet E/E architectures – in other words, starting with a clean slate and devising new ways to meet evolving integration, safety assurance, simulation, and verification needs:
- Integration: Key considerations include space reservation and packaging, and the ability to manage changes and releases effectively.
- Safety assurance: Teams must implement requirements traceability, while ensuring signal routing, separation as well as redundancy. They must also provide extensive diagnostics, maintenance, and repair support to ensure driver protection.
- Simulation and verification: These practices enable correct-by-construction design. Electrical simulation is now essential to ensure vehicles operate as intended.
With all this top of mind, many leading auto manufacturers are looking to innovative E/E development solutions like Siemens Capital for help.
Capital simplifies E/E systems development for the modern EV
Siemens approaches E/E system development differently by enabling engineers to integrate requirements and system models cohesively into comprehensive E/E architecture. This model-based approach encompasses software and network communication, integration, verification, and visualization, and enables proper electrical distribution across harness design, manufacturing, and services. Collaboration throughout the design lifecycle and full traceability are also enabled via the digital thread. Using Capital Teamwork, teams can safely and efficiently share data with people across an organization throughout the E/E design process.
With a platform-level view of all electrical, electronic, software, and network components, Capital can generate downstream implementation proposals that connect the E/E design to the digital thread. In this way, teams can explore various options for implementations and optimize the E/E architecture accordingly. They can also link the architecture to the mechanical data for accurate results in the physical implementation.
Using Capital, companies of all sizes can benefit from enhanced margins and faster time to market. They can expand their range of product offerings, compete more effectively and enhance their brand’s perception with high-quality EVs that meet and even exceed consumers’ needs.
Auto manufacturers using Capital have reduced per-vehicle costs by $50 and per-vehicle weight by 6.5 KG. They’ve cut electrical design time in half, and quote-to-production cycle time by 30%. What’s more, they’ve been able to meet safety and compliance requirements while reducing service documentation time by 80% and fault diagnosis time by 40%.
“We needed a development environment to visualize the entire vehicle…Capital provides the environment to make Mazda’s electric development much more efficient.”
– Kazuichi Fujisaka, Technical Leader, Mazda
Download our infographic to learn more about the state of the EV market and what Siemens’ customers have to say about using Capital for E/E systems development.