Generative Engineering: Automation for Electrical Distribution Systems
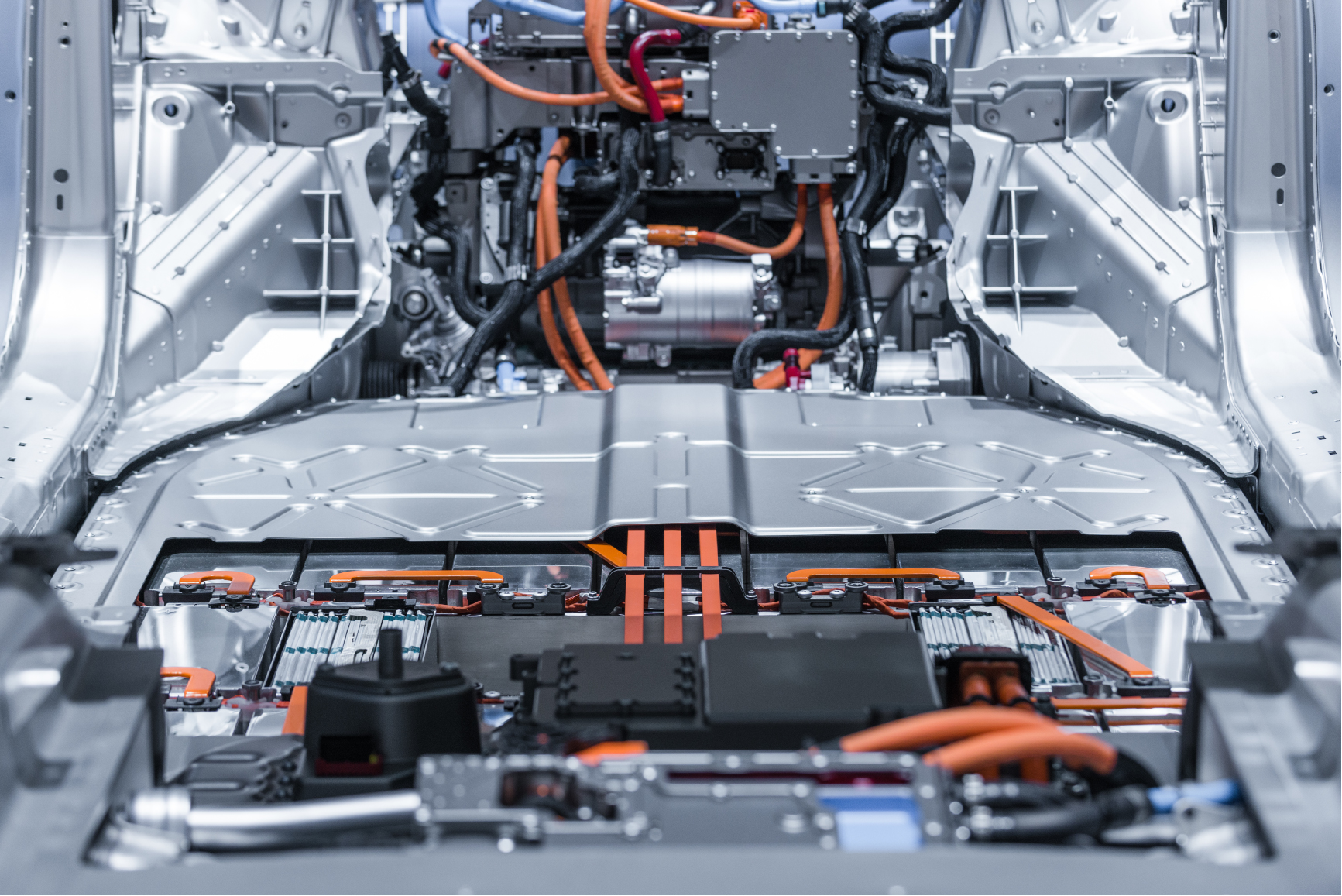
Products are becoming more connected. To address the rising user demands, manufacturers are adding more and more smart features to their platforms. This means that modern products incorporate an increasing number of electronic control units (ECUs), sensors, antennas, and other electronic endpoints and subsystems.
All this means that electrical/electronic (E/E) systems are getting more complex fast. And this trend is only going to accelerate as new technologies like edge computing, ubiquitous connectivity, and Internet 4.0 become more common.
So let’s unpack E/E system complexity. In this post, I’m going to discuss:
- how engineering teams can address the challenges of this trend by harnessing design automation for E/E systems design,
- why the traditional approaches to engineering fall short, and
- how teams are turning to generative engineering solutions to:
- tackle the added workload,
- speed up their processes,
- optimize their architectures, and
- create E/E systems faster and more efficiently than before.
Increasingly Conflicting Requirements
It is not enough for products to be smart and connected. These days, they also have to be higher performing than their predecessors. This can increase design complexity quickly.
So as an electrical engineer, you have to counterbalance many design requirements while developing a new E/E system. And as if that weren’t difficult enough, these requirements are often conflicting. For example, in automotive and aerospace design, weight reduction is a primary concern. Traditionally, design teams could afford to use only a single architecture across the whole platform. These combinations of ECUs, wiring harnesses, and software modules had to be compatible with multiple vehicles and address every E/E need.
As a result, these systems were over-engineered to account for all possible design requirements and configurations, representing a 150% system. This increased the weight of the vehicle substantially without contributing at all to its function.
This isn’t to say that reusing the same E/E system across a product platform doesn’t offer many benefits. It does. Manufacturing costs are lower as you can take advantage of economies of scale. More importantly for the engineering team, the development time is significantly shorter, as you only have to develop and test one E/E system.
But this approach doesn’t work with today’s products. Weight, cost, and other constraints are driving manufacturers to develop E/E systems that meet the exact requirements of each variant.
Manual Approaches Yield Barely Feasible Designs
Today’s products come in a dizzying array of options. And their variants may differ dramatically from one another. In fact, the different functional requirements of each E/E system mean that wiring harnesses can be rarely reused in variants of the same products.
Manually designing a new E/E system for each configuration, which is the traditional approach, is a monumental task. You have to create a new system for each variant, which comes with its own set of design requirements.
Engineers can certainly do this, but it is exceedingly difficult and practically impossible to reach an optimal solution: It could take hours or even days to design the right harness for each use case. This might be acceptable for simple systems, but it is extremely inefficient and unproductive for complex platforms.
Take a car as an example. The engineering team can manually explore many E/E architectures for a single variant pretty easily. But if there are 300 variants to consider, this adds up to a ridiculous amount of work.
Yet, companies have been operating this way because they had no other option.
Employing Generative Engineering Approaches
Enter generative engineering.
The core idea of generative engineering is this: Let the software automatically create feasible architectures and designs of an E/E system based on the specific set of design requirements you’ve provided. This extends further into wiring harnesses, manufacturing drawings, and service documentation.
First, you describe the constraints of each design variant. Then, you let the algorithm generate a configuration of electronics, electrical distribution, and software that meets these constraints. Finally, you review the results. If there is more than one feasible solution, select the best option.
The role of the engineer shifts dramatically in the generative engineering process. In the traditional approach, the engineer had to come up with new possible solutions. In the novel approach, the engineer is freed from that task. He can focus on clearly defining the problem and reviewing, verifying, and selecting the best solution.
This is the promise of generative engineering.
This new approach has a big impact on the way we develop new products. It lets engineers prioritize core design work over manual design tasks. And by incorporating automation, it speeds up the development process. Your engineers can go through 10 design iterations in the time it used to take to complete one. And now, engineering teams can develop tailor-made solutions for each use case and meet their deadlines.
Recap
- To address user demands, companies are integrating smart features into their platforms. On-board processing units, sensors, and antennas are becoming more and more common in consumer and industrial products. As a result, E/E systems are getting more complicated.
- This trend introduces new complexities to the product development process. Engineers have to add yet another design consideration to the already long list of design requirements—some of which conflict. It’s obvious that the manual design processes of the past are too time-consuming and expensive for modern production.
- Generative engineering is an alternative to the traditional approach to E/E system design. Using algorithms, engineering teams can leverage design automation to generate system architectures, wiring harnesses, manufacturing drawings, and service documentation that meet the unique requirement of each application. This allows them to go through 10 times more design iterations in the same amount of time and create products with higher performance.
This is part two of three guest posts by Chad Jackson, who is the Chief Analyst and CEO of Lifecycle Insights. He leads the company’s research and thought leadership programs, attends and speaks at industry events, and reviews emerging technology solutions. Chad’s twenty-five-year career has focused on improving executives’ ability to reap value from technology-led engineering initiatives during the industry’s transition to smart, connected products.
You might also be interested in:
- Part 1 of blog series: An Advanced Approach for E/E Systems Development
- Paper: Re-imagining electrical systems design