How existing organizational infrastructure puts you at a disadvantage – supply chain resilience is not built into the design process
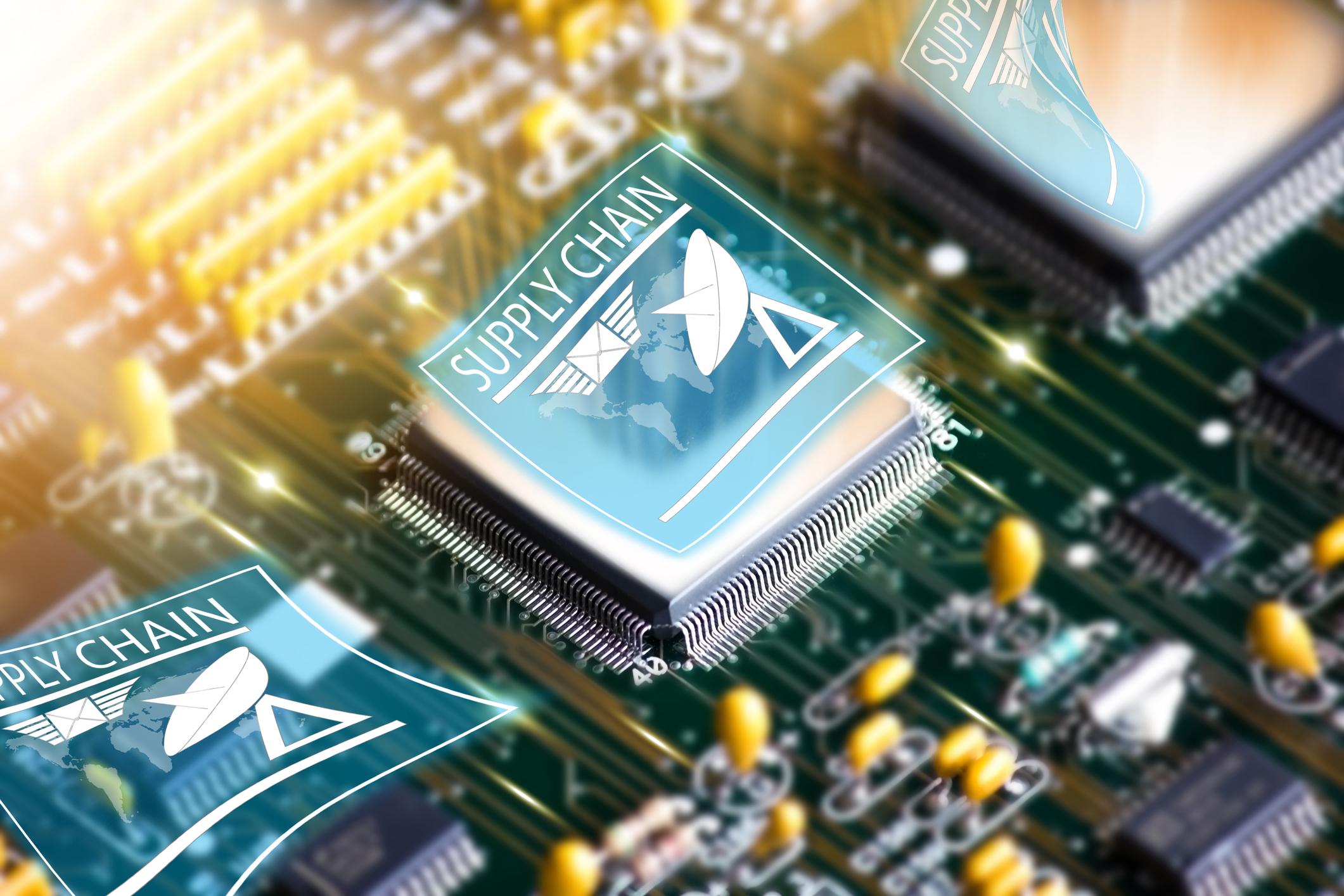
In our second episode of the Printed Circuit Podcast, we talk about existing infrastructure within organizations and why it’s adding to the supply chain problem overall.
The problem with silos
In many organizations you will still see silos when it comes to PCB design and supply chain functions. Even as massive digital transformation has occurred in other areas of the business, this area has been left behind. Let’s break this down.
There are a set of competencies within an engineering team that often includes:
- Design
- Engineering
- Component engineering
- Test
- Quality assurance
- Design for manufacturing
These teams are typically fragmented. Each has a high degree of autonomy to make design decisions to achieve the top-level goals for that product or that design, but they don’t necessarily have the power to get the product to manufacture on time, to ramp up the volume on time, or to hit revenue and margin goals.
The most difficult hurdle to overcome is internal organizational resistance to change. Designing for supply chain resilience is about bringing external content and knowledge right to the point of design. The problem is that there are internal battles that go on, where people say, “That’s my job,” or “That’s not my job.” So, they stay in their silos. You have got to adapt and evolve to survive and be successful.
An opportunity to break down silos: new product introductions
NPI teams provide an opportunity to build and extend cross-functional decision-making because NPI stakeholders typically are cross-functional already; you generally need to have the right representation of program or project management across engineering teams that then extends into release management into manufacturing. So, you typically will have some form of manufacturing, supply chain or procurement representation, finance, and then even commercial teams.
We can build on this.
We just need to change our thinking to:
- How are we driving more intelligent decision-making?
- How are we improving the agility and speed of these decision-making cycles?
- How do we make sure decision making is more cross-functionally visible with all key stakeholders?
Asking these questions launches a process of continual improvement. Then, as market conditions evolve, the team can go back and realign to new solutions as needed, whether that’s selecting alternate parts, bringing in alternate suppliers, or choosing an alternate manufacturing location.
The approved parts problem
Oftentimes there’s a reuse of key components or design elements from an earlier version or generation of a PCB board design. And sometimes that design goes back two or three years, because these product lifecycles can be multiple years.
That occasional reuse of components has worked for the most part, until now. However, in this new market, making component decisions and then pushing them forward in a linear manner has created a huge problem. Organizations have been surprised by parts and components being designed in that are unavailable. There may be no available supply worldwide for that component, or the component that was used in an earlier design that used to have a six-week lead time, now has one up to 45 weeks.
We’ve seen this problem around almost every commodity category. This isn’t just affecting the most expensive, most critical parts; this is really across the board, including “popcorn parts” which are typically very low cost and assumed to be highly available, for example, passives, ceramic capacitors, transistors, and diodes.
The missing link: digital thread intelligence
Traditionally, part component libraries have a shared environment for a product lifecycle management where there’s a repository of bill of materials and designs. Much of that stored information has been static, updated infrequently, and only covers the parametric or technical details of that part or component. Traditionally, the big focus was on the years to end of life or the obsolescence status of those parts or components. But what’s been missing is the same intelligence extended into:
- What does the supply market look like?
- What is the actual current and projected lead time?
- What is the current demand for those similar components?
All of this now is becoming incredibly important. To design products and make decisions at the lowest cost of change, this information is needed as early in the design process as possible.
Shifting left
Where does the lowest cost of change occur in the product’s lifecycle? It starts with design engineering, and that’s the whole point of shifting left. We don’t just want to put more pressure on design engineers, who are already overworked, burned out, and under pressure, but we want to empower them with new information so that they feel like they’re not flying blind.
Empowered engineers
Siemens has already been investing to empower engineers with more intelligence at their fingertips, especially through the Supplyframe acquisition. Today we can empower engineers with the right intelligence around supply market conditions so their work is informed and autonomous.
They don’t have to be an expert at every supplier, and they don’t have to know all the supply market dynamics. But there’s a view of red, yellow, green, of component availability. This is a huge start to filter out availability based on supply, market, feasibility, etc. We can empower those teams to operate the same way that they’ve done before, but with more intelligence. It starts there; it’s about empowerment, it’s about the same source of intelligence.
Want to learn more about the impact of supply chain systems on PCB design? Listen to the podcast now, available on your favorite podcast platform.
Expand to see the Transcript
[00:12] Steph Chavez: Hi, everyone, and thanks for tuning in to the second episode of the Printed Circuit podcast, where we’ll discuss trends, challenges, and opportunities across the printed circuit engineering industry. I’m your host, Steph Chavez. And as a refresher, I’m a Senior Product Marketing Manager with Siemens with three decades of experience as a Printed Circuit Engineer, and currently the Chairman of the Printed Circuit Engineering Association. So, joining me today is Richard Barnett, Chief Marketing Officer with Supplyframe. Richard, thanks for joining and being here.
[00:39] Richard Barnett: It’s always a pleasure, Steph. Thanks for having me.
[00:44] Steph Chavez: On our last episode, I talked with Chad Jackson, who is the Chief Analyst and CEO with Lifecycle Insights, about the new normal that we’re living in now, especially with what’s unfolding in the industry and how things have just been totally chaotic with a pandemic and geopolitical issues going on in the world. I’d like to take a deeper dive into the topic and really focus on existing organizational infrastructure and why it’s adding to the problem. What is your take on that?
[01:11] Richard Barnett: There’s an interesting pattern you can look at. Most organizations have design engineering teams that create or design hardware that’s a part of their products or services to their customers, and it really spans multiple industries. It’s the same pattern in issue, even though it plays out slightly differently with companies that are early in their growth period in high-tech startups, there’s 20-50-year-old industrial equipment or aerospace and defense organizations. What’s interesting over the last few years is that we’ve seen it be very consistent, but it’s a significant challenge and problem that essentially is really faced a significant turning point for many organizations where, characteristically, you would have these organizational silos that really haven’t evolved that much where we’ve seen massive digital transformation, oftentimes a lot more cross functional, integrated processes or collaboration inside the organization or across an ecosystem outside. We’ve seen this as an area that’s been left behind. And what we mean by this is typically an organization that has an engineering-oriented team that has a set of engineering competencies within that team; it often includes design, engineering component engineering specialists that are kind of a shared service across different programs or projects that are going on where they’re revealing obsolescence of critical parts and components or they’re making sure that there’s compliance or governance around the AVL, or the Approved Vendor List, for key suppliers when those new design cycles are kicking off. Obviously, it includes other functions, oftentimes, within engineering as well that includes test, quality assurance, and other related activities, maybe designed for manufacturing as well. But when we look at the core electronic design components and the process of designing, selecting key components, and building that into a design bill of material, what traditional organizations have, given their engineering teams, a high degree of autonomy to make those design decisions, to achieve the top level goals for that product or that design.
[03:16] Richard Barnett: Oftentimes there’s a reuse of key components or design elements that were used in an earlier version or earlier generation of a PCB board design or another product. And sometimes that goes back to two or three years because these design or product life cycles, depending on the industry, can be as short as 18 months, but can be as long as three to five years. That reuse, that kind of “Let’s build on what we knew before, and then let’s try to pick the best design-to-quality decisions, but let’s just pay attention to the parametric information, let’s make sure that it’s built for design, that it has the appropriate attributes for that application,” has been totally fine and good enough. It’s been a very stable set of “authority domain” around decision making. The challenge has been, in this new market, is that model, kind of good enough, the good old days — sort of making those design decisions and then pushing them forward in typically a linear process where there may be a checkpoint review with component engineering, and then it’s kind of thrown over the wall to sourcing procurement to either buy and select the early volumes of maybe the early build quantities or the first test quantities all the way up through that true new product introduction that’s going to be on a path or a roadmap and a schedule for ramping to volume. All of that’s occurring really to the right, if you will, of that core initial process. And there’s not really been a lot of common feedback loops or collaboration. It’s created a huge problem where organizations have been surprised and caught off guard by parts components being designed in, which in this market really a reality over the last two to three years may be dead on arrival; there may be no available supply worldwide for that component, or the component that was used in an earlier design, just 18 months ago, particularly during the startup COVID, that had a six-week lead time, now is up to 45 weeks. We’ve seen that all over the place, around almost every commodity category. This isn’t just your most expensive, most critical design, IC or custom ASIC or something; this is really across the board, including “popcorn parts” — typically very low costs and typically assumed to be highly available. Passives, for example, ceramic capacitors, transistors, and diodes. The root of this is process, but it’s also incentive management.
[05:43] Richard Barnett: These organization design teams have generally been held accountable to new design, new product or project being released on time to top-level target design goals, but not necessarily on the commercial feasibility of either the ability to manufacture on time, the ability to ramp the volume on time, or the ability to hit revenue and margin goals even though there’s a plan and there’s a notional target that’s established typically early on. It’s not really the engineering team’s full responsibility or accountability to hit those goals that are further downstream. The other real common issue is what I call the digital thread of intelligence around what’s going on with those components. So, traditionally, the part component libraries have a CAD environment or an engineering shared environment for a product lifecycle management where there’s a repository of passed bill of materials and design, a lot of that information has been static, updated infrequently, and only covers the parametric or technical details of that part or component. Traditionally, the big focus was on the years to end of life or the obsolescence status of those parts or components, particularly in industries that are building products or services that have a very long lifecycle with the customer. And that’s very true in industrial, very true in aerospace and defense, pretty true in automotive, five to seven year kind of program life cycles. But what’s been missing is the same intelligence extended into, what’s the supply market look like? What is the actual current and projected lead time? What is the current demand for those similar components? How popular are those engineering design decisions that a company might be making in a silo? How’s it playing out in the broader ecosystem, in the broader community of similar design engineers that are working in similar application areas? All of this now is becoming incredibly important in order to design products and make decisions at the lowest cost of change, which is as early in the design process as possible, that have more intelligence. And that’s that shared intelligence that is connected or extended. So, everyone’s working off the same single source of truth, everyone’s making trade-off decisions that they’re trying to balance, design quality goals, feasibility of design alternatives, maybe the cost of onboarding alternate suppliers, the overall cost of those components, and then the overall success of that product over its lifecycle has now become the critical shared decision-making that needs to happen.
[08:10] Richard Barnett: But in most organizations that we work with today have collapsed those silos but not in a structured, coordinated, top-down-lead alignment way. It is react, firefighting mode, it is emails, it’s Excel spreadsheets with BOMs, it’s calling suppliers, it’s getting a quote, it’s scrambling to find out who found the latest on what last week on those 15 key components that we had a critical power shortage in. And they can design, go back and redesign potentially either a sub-portion of that overall design or even complete products almost from scratch. I mean, a fundamental redesign cycle is now consuming anywhere between 10% to we’ve seen up to 60% of an existing engineering team completely cannibalized with just trying to redesign existing products that are already released to the market in manufacturing, so that they can feasibly just make more of it equivalents to meet customer demand or to meet the same product design requirements, just playing catch up, and everyone across the board is just burned out. So, these conversations, this collaboration is happening in a highly constrained way, a lot of finger-pointing going on. And the last element I would say that really shocks me is that at the C-level leadership, there’s obviously an awareness of the problem. There is a significant eye on the problem. But the idea of what is a better answer, what’s a better approach? There’s no clear consensus. Most of the executive teams that we start bumping into, we start to the CFO, we’ll talk to a COO, we’ll talk to a general manager of a business unit, obviously, talk to the supply chain — very different views. I feel like it’s a bunch of the blind folks touching the elephant in the room; “Oh, it feels like the tusk, it feels like the tail, it feels like this big leg. That’s where we need to anchor our focus.” One of the design engineers at an aerospace and defense supplier was telling me that the best response he’s getting from his C-level teams last few months has been, “Well, what do you need? Do you just need more headcount? I’ll approve more headcount for you to hire.” And we go through just laughing at that going, “Throwing bodies at this problem is not the answer.” So, we’re kind of in a crisis moment, but there’s so much silver lining. This is a crisis that if we take the right steps, not just these organizations will be more resilient, but their success in the market will be better, their customers will benefit. And there’s an ecosystem effect here too where we’re getting better intelligence, more collaboration, more agility built into the way we’re going to market with resigned products, and we’re thinking about collaborating all the way through its lifecycle. And that it really is exciting to me, but boy, the cost, challenge, and the pain that everyone’s been going through is just mind-numbingly painful to me.
[11:01] Steph Chavez: You mentioned so many golden nuggets in the last 10 minutes of what you just shared with us. And I will tell you, the first thing that jumps out at me is when I think about the infrastructure and how companies are organized, from my last 13 years or 12 years within the Mil-Aero, but in my decade of consulting and working, whether it’s commercial, medical, military, aerospace; it’s amazing how people stay in their swim lanes and their inherent walls built up, and the resistance to change is typically just what I see as internal culture within a company. And that becomes the most difficult hurdle to overcome. And when we talk about design for resilience, you’re talking about bringing external content and knowledge to the point of design. The problem is that there are internal battles that go on, where people say, “That’s my job,” or “That’s not my job.” So they stay in their silos. And the sad thing is that the way we’ve been producing in the past or functioning in the past is a just-in-time approach. Well, guess what? That does not work anymore. I shouldn’t say “it doesn’t work,” but you will not be able to sustain and survive if you maintain the status quo. You have got to adapt and evolve with what we’re seeing with the supply chain resilience. And now we know, it’s there and it’s in our face, we need to move on. And the companies that embrace this and adapt to it, they’ll survive and be extremely successful; those that don’t, will slowly fade away. It’s sad. I’ve witnessed this firsthand, I refer to it as feeling the supply chain pain. And believe me, as a board layout designer, it’s brutal. I’ve seen it on projects. Reiterations, like you talked about, the spiderweb-like networks; the way our communication, whether it’s stand-up meetings, emails, or verbal communication — we have so many opportunities to be optimized and better. But the problem is that companies are not willing to change it on the fly because a customer is not willing to pay for you to design their widget and pay for you to optimize your process to make their widget; they just want their widget. That’s the trade-off, that’s the challenge. So, how do companies change and adapt? They’re going to have to find a way. Many companies are doing this and are killing it. And they’re either killing it or they’re getting there. When we talk about this linear approach, this is the other play that’s an issue, and it’s with our current processes. These linear procedures, as we observe, how many companies operate today? We’re very complex, and like you said, it’s a spiderweb-like network from these informal processes. Can you expand on that even more? Especially when we talk about how we’re functioning or lack of cohesive function and optimization.
[13:44] Richard Barnett: Well, like I said a little bit earlier before, part of this requires a systems mindset, where you’re thinking about the digital aspects, knowledge, and intelligence that we can apply to the part component, to the PC board, to the product itself. And then thinking about, “Okay, how do we collaborate with intelligence internally?” So, some of this is about extending the scope of the intelligence. So we’ve already been investing significantly to empower engineers with more intelligence at their fingertips. So, if they have a need for autonomy or if there’s a design cycle that’s kicking off and they want to be empowered to look at all the trade-offs and considerations, part of the move is to empower them with the right intelligence around supply market conditions. They don’t have to be an expert at every supplier, they don’t have to be able to know all the supply market dynamics. But there’s a bridge there, right where you started introducing risk ranking, for example, or a view of red, yellow, green, even just as a huge start to simply try to filter out first-level pass quality mindset around supply, market, feasibility, etc., because it’s additive, we’re asking those teams to do more, but we can do this. Without breaking glass, we can empower those teams to operate the same way that they’ve done before, but with more intelligence. And you change the scope of what the outcomes they’re trying to drive towards. And that becomes a new concept of how do we think about risk and risk of the product or risk trade-offs in design cycles. So, I think it starts there; it’s about empowerment, it’s about the same source of intelligence. But as soon as we step outside of that core design engineering area, you’re right, we need to be thinking about the new product introduction process in a different way. And the reason why I call the NPI process out is that many organizations will have relative levels of maturity, fairly repeatable, somewhat formalized, and maybe overly formalized, bureaucratic approach, somewhat ad hoc in some cases. But generally, these NPI teams are really where there’s an opportunity to build and extend cross-functional decision-making that’s better than what most companies are doing because really, NPI stakeholders typically are cross-functional; you generally need to have the right representation of program or project management across engineering teams that then extends into release management into manufacturing. So, you typically will have some form of manufacturing, supply chain or procurement representation, finance, and then even commercial teams. They’re looking at and understanding, “Okay, we have an initial design, but let’s iterate and make additional trade-offs either for the assurance of supply or for cost optimization, designed for manufacturing, or just from the time-to-market perspective,” because some of the ramped up volume limitations are one of the guiding most critical factors right now.
[16:35] Richard Barnett: So, many organizations, particularly in regulated industries, if you look at medical device, automotive, and Mil-Aero have what I would call NPI processes — on face, highly formal, but based upon a very bureaucratic procedural checklist-based approach to ensure that there’s documentation, that there’s compliance, that there’s a review process that’s meeting the regulatory mindset of either to quality or to external regulation. And that takes many different forms, whether it’s FDA regulations, whether it’s within Mil-Aero itself. We can build on that though. And it needs to look a lot less bureaucratic and checklist-oriented and much more empowered around dynamic trade-off analysis, so that you can iterate and see what’s the net change of the sum of all the changes that we’re looking at making on an overall risk score, on the overall target costing model on terms of accuracy, on even demand forecast changes — incorporating those scenarios now more dynamically in rather than just having that artificial one number that no one ever believes is going to be achieved. All of that needs to come in together. And I would argue it’s the NPI process, which is the starting point. But then the other aspect of this is you want to look organizationally at where’s the NPI process housed inside that organization. And companies that have a stronger, center-led supply chain services organization are good holders of the flame—keepers of the flame, so to speak—of that NPI process. Sometimes organizations are a little bit more P&L-focused, traditionally, by a business unit function or maybe a manufacturing plant location. It’s engineering coming directly in manufacturing or contained within a business unit. So, it’ll vary a little bit around how that organizational model needs to evolve. But generally speaking, it’s about thinking: How do we drive more intelligent decision-making? How do we improve the agility and speed of these decision-making cycles? And how do we make sure it’s more cross-functionally visible with all key stakeholders so that as market conditions change or as the evolution of the product evolves, everyone’s awareness is down to why decisions were made? And as the market conditions change, they can go back to a digital model of that product and those assumptions and make those changes very quickly, and then realign to whatever they need to do, whether that’s alternate parts selection, whether that’s bringing in alternate suppliers choosing an alternate manufacturing location.
[19:03] Richard Barnett: That’s really, at the core, a digital enablement of a process that might be existing today but needs to be superpowered way beyond where it is today. We need to lean in on that aspect because information, technology, and intelligence is really all there. This is really about organizations’ leadership challenges and change management challenges. This is about reapplying those capabilities in the right way. And you can start in different areas. It’s not a big-bang change, you can start by empowering engineers or you can start by empowering sourcing procurement teams to work better. But we need to invest in this area, this is an area that’s been left behind. In almost every other digital transformation within the enterprise, we’ve had years of iterations and experience, almost two or three generations worth of thinking around redefining customer experience or redefining and thinking about global finance consolidation and managing in a dynamic market, treasury management, and cash management. All of this is leapfrogged, but we have not moved an inch in this area, in this zone, since the beginning of the first wave of digital transformation. So, there’s no excuse for this, we have to lean in and we have to move.
[20:12] C: I couldn’t agree more. As we’re diving even deeper into how enterprises leverage operations today, we clearly see that the touch points of the external data source, not surprisingly, the external to the spiderweb-like network of operations, that these touch points range from the part and pricing demand, parametric search of alternates, supplier-ramp availability, part availability, lead time, supplier geo risk, alternative suppliers regarding popularity, financial health and capacity, then you have these touch points that are external to the enterprise that were initially dealt with downstream. We’ve now got to move them upstream. And I think you commented that, basically, by saying “we’re shifting left,” can you give me your insight as to “the shift left” or your thought on that as well?
[20:57] Richard Barnett: We’ve heard “shift left” used in other contexts, but it’s very relevant now because I think the idea here is that we need to have a systems mindset and we need to be thinking about root cause. We think about quality management, we think about root cause remediation, and productive action. The same mindset here. But if you really think about it from a systems perspective, where does resilience, where’s the lowest cost of change, and where does the potential risk of locking in risk occur in the product’s lifecycle, it starts with design engineering, and that’s the whole point of shifting left. All we have to do there is not just process why you shift left and just put more pressure on design engineers, which are already been overworked and burned out and under pressure, but we need to empower new information so that those design engineers feel like they’re looking at the same trade-offs as early as possible, they’re not flying blind. As part of this is you’re going to get sub-optimal decisions with very, very smart team members in design engineering and component engineering even if they just simply don’t know what they don’t know. So we’ve got to start solving that problem. Take the blinders off and provide the right outside intelligence like you just said. The other aspect of this is that we also need a concept that is moving into more of an awareness that the information that’s actually needed to make these trade-off decisions does not exist inside the enterprise. And that’s a really important paradigm shift. Most organizations, still today, think, “Well, if it’s in my part component library, if it was on my approved vendor list.”
[22:24] Richard Barnett: We have, in our new ERP system, the last PO for the cost that we had for that part, aren’t we good? Don’t we know cost? Don’t we know it’s safe to select? Don’t we know who our best vendors are? The answer is no. One customer, I challenge them with this thought, I said, “Do you realize that 95% of the information that you have about your suppliers, your parts, and components in your ERP system is inaccurate, that your MRP lead times are actually completely inaccurate?” And they came in and said, “What do you mean?” Just think about it for a second, you have lead times that were set three years ago as your standard lead time for a part or component by a supplier. None of that is accurate today. That means all your enterprise systems that you’ve invested millions and millions of dollars or euros into over 20 or 30 years, they don’t serve you here. So, if you start with that presumption, then change happens and it happens pretty quickly. But the other dimension of this is this mindset of “If I’m only checking for obsolescence and the AVL, I’m good.” And I would argue that it’s table stakes — that doesn’t move you down solving this problem at all anymore. It doesn’t help you make any value-added decision, it will reduce some risk, and you don’t absolutely want to select a part or components that’s obsolescence. But the default lead times, we move into 45 weeks, 52 weeks, or 60 weeks. That’s exceeding the obsolescence risk of any available part or component you’re trying to protect. That’s the issue that we need to solve.
[23:55] Steph Chavez: I agree. I can tell you most EEs, when they are selecting their parts at the point of design, are picking from a library that is static library of information that was done whenever that part was released into the system. They have no idea of availability or price, all they know is it’s a released part in the library system. I think you nailed over the last 15-20 minutes that you shared with us your thoughts, you’ve hit everything on the head, you’ve nailed it. Now that we’ve established the problem, where it lies, which is in the process, we need to get to the solution. And the solution is supply chain resilience — the capacity of a supply chain to persist, adapt, and transform in the face of change. This leads to the question though: How can businesses manage risk and plan for a resilient future? That’s what companies need to look at internally and figure out for themselves what they need to do. You and I, and many others, we are publicly addressing this, but ultimately, like we talked about, company leadership, they’re the ones who’ve got to implement the change and they’re the ones who got to do this because I know that the engineers down in the trenches want to adapt and change but they’re locked in the swim lanes or in these inherent legacy processes that were designed for resilience is not inherent to it. At a high level, it’s clear that supply chain resilience is not inherent to the processes; therefore, many organizations are highly vulnerable to supply chain volatility since the engineering sourcing handoffs are highly linear, as we talked about, and they’re just not built with supply chain resilience in mind. So, on our next episode, I’ll dive into the first pillar of the three-phase approach to creating supply chain resilience at the point of design. Richard, I can’t thank you enough for joining us and being here today, and sharing your amazing golden nuggets with us. We look forward to the next Kool Aid you’re serving because we’re all drinking it and you’re bringing it. So, thanks again, for joining me on today’s podcast.
[25:48] Richard Barnett: Thanks, Steph. This conversation, I think, is so absolutely critical, we’re both very passionate about it, but I think we need to sing from the mountaintops a little bit because there needs to be this active conversation with every single customer we’re talking to. It’ll play out differently, but these insights and the guidance that we can provide and learn from, those that are leading the way, are absolutely critical right now. So, thank you so much for having me and I look forward to the next opportunity to join the conversation.
[26:12] Steph Chavez: The pleasure is mine. I hope this discussion has been insightful in understanding how existing infrastructures put you or your company at a disadvantage where resilience is not built into the design process while we adapt to move on to better supply chain resilience. So, tune in next time for a deep dive into how knowledge enables supply chain resilience. Thank you and I hope you continue to tune in and follow me on this Printed Circuit podcast.