Five ways to achieve pre-layout simulation with PADS Professional Premium
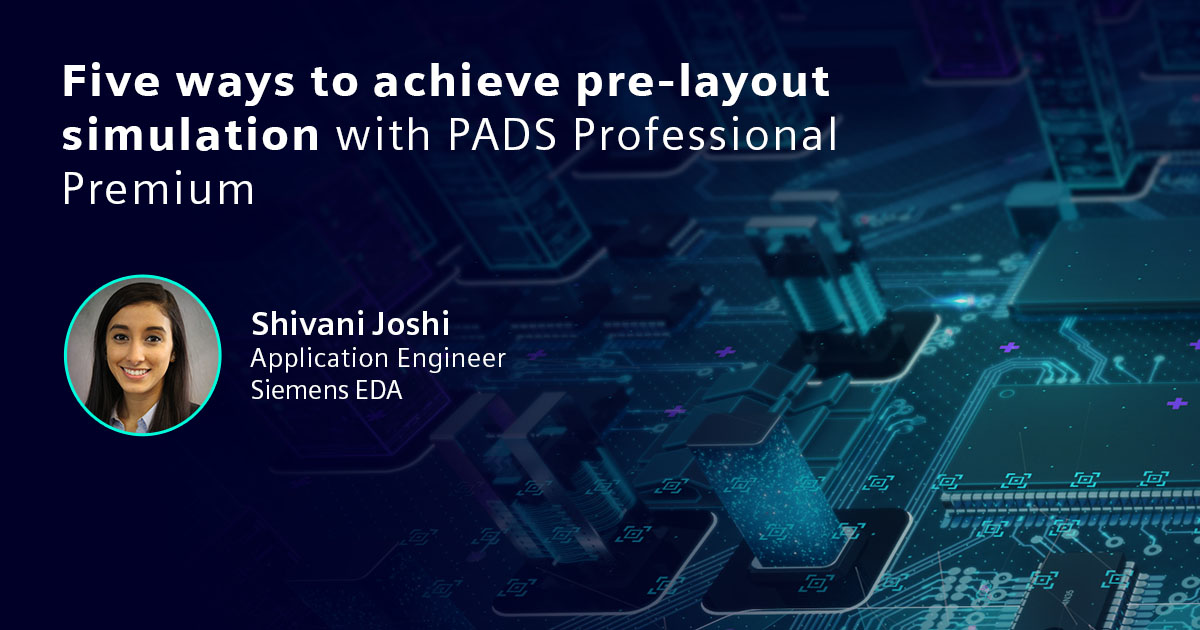
With increasingly advancing technology and faster edge rates in today’s integrated circuits, it’s important to find more efficient ways to keep up with high speed effects. It’s clear that simulation is an important step when designing boards as it saves time and money by performing tests before production, but simulating earlier in the design process allows for even more efficiency. Pre-layout analysis allows for PCB designers to plan and adjust their design to fit requirements before setting a single component or route.
Let’s look at five ways to achieve pre-layout simulation using PADS Professional Premium.
1. Easily export individual nets and set up your transmission line
Starting in Pads Professional Premium Designer, users can export individual nets to simulate in a pre-layout environment. With a quick right-click to export, the net is quickly exported into HyperLynx LineSim. In this LineSim environment, you can set the driver model from an easy-to-use menu. Simply double-clicking will open an “Assign Models” dialog where drivers and receivers for this net are ready for assignment. Simply select the desired library device and signal or pin.
Similarly, reviewing and setting up a transmission line can be done with ease. You can choose from a stackup, microstrip cables, and many more trace types to ensure you’re simulating exactly what you intend on using during your layout. The “Values” tab can aid in layout decisions as well. Choosing the layer you’d like to route on, and the width and length of the trace, you’re able to quickly review the changes and electrical properties to make sure that the requirements are met without any guesswork during layout.
2. Adjust a board stack up
Another factor that can help before layout are adjustments to a board stackup in HyperLynx LineSim. The stackup editor allows for easy planning and shows how changes in physical properties, such as layer thickness and materials, can change electrical properties, like characteristic impedance. Simply plan according to impedance targets for your design, and HyperLynx can calculate the appropriate width for that layer.
3. Plan for differential pairs
Planning for differential pairs can be done during the pre-layout stage as well. Choose to keep the trace separation constant and solve for trace width or vice versa. You can solve for both by producing a width versus separation graph to aid in optimal value selection for your target impedance. This is an ideal tool for SerDes and DDR nets, which can be a little bit more sensitive and need some additional planning.
4. Simulate coupling regions
HyperLynx LineSim also simulates coupling regions. To define how two or more traces are coupled electromagnetically, simply select two nets from the schematic and bring them into LineSim. To visualize and later simulate the coupling region, select two transmission lines and use the right-click menu to couple them. From the Edit Transmission Line window, users can move the trace to different layers in their stack up and adjust parameters. As physical adjustments are made, the characteristic impedance is automatically affected and recalculated right in the same window.
The Field Solver tab calculates the electric and magnetic fields associated with both transmission lines. The propagation can be switched to show differences between common and differential modes to minimize reflection.
5. Use terminator wizard to terminate nets
HyperLynx in Pads Professional Premium provides a convenient way to terminate nets. The terminator wizard is used to improve signal integrity properties for your nets in your schematic design. Along with optimal termination component values, the wizard makes suggestions for improving the performance of a net, including changing the value of existing termination points or adjustments to the net length itself.
Why is pre-layout simulation important?
Running analysis at any point in the PCB design flow is integral to producing quality, high speed boards, but starting in the pre-layout environment gives you the confidence to know you’re meeting design requirements from the beginning.
Interested in diving deeper into this topic? Watch this on-demand webinar: PCB Signal Integrity for small to medium PCB teams.