Creating supply chain resilience for small and medium PCB design teams
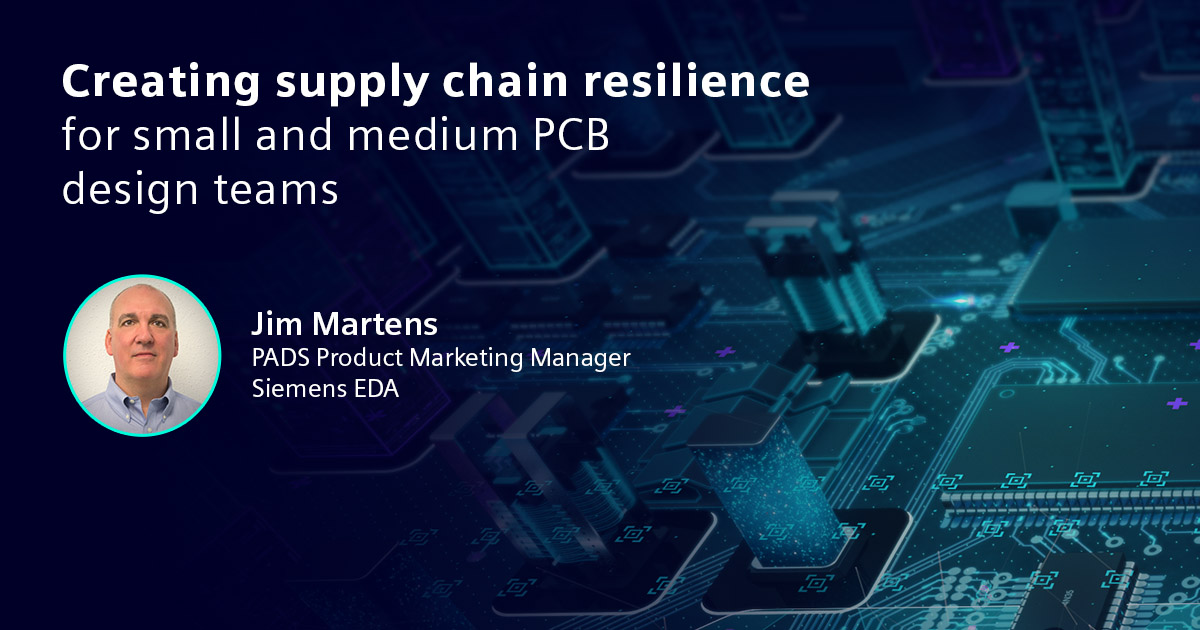
PCB supply chain disruptions
Disruptions in the PCB supply chain have caused problems for product development teams within most companies. These disruptions started several years ago but were exacerbated by COVID-19:
- The electrification across all vertical markets increased the demand for components and the need for new products and designs.
- The supply chain has become more complex, with suppliers spread across the globe, meaning geo-politics impacts trade with several countries.
- Due to several reasons, such as intense competition and the need to be first to market, engineering teams are seeing more pressure to reduce their design cycles.
- And lastly, increased supply chain market volatility – supply shortages are everywhere, and you usually have no insight on whether a part is available or not, or how long a backlog may be.
Also, a lack of collaboration across the PCB supply chain makes identifying issues difficult and is costly to your company. In a study by Dimensional Research, major issues are consistently being reported by respondents:
- 91% say sourcing issues have caused product delays.
- 81% state commodity availability has forced their companies to overpay for parts.
Truly, it only takes one part to derail and delay your product launch! Making the right decision in part selection early in the design process is critical to success or failure.
What is supply chain resilience?
Supply chain resilience is defined as “the capacity of a supply chain to persist, adapt, or transform in the face of change.” And of course, this really means how well do you and your company persist, adapt, and transform in the face of these supply chain challenges?
You’ve probably heard a message of “shifting left” over the last several years. This usually refers to doing more planning, or simulation and analysis earlier in the design process. Now we need to shift-left supply chain insights, so they are visible when engineers are selecting parts for their designs.
By shifting left sourcing insights, the engineer can design in the best parts for cost, availability and performance. By streamlining the collaboration between sourcing and engineering, the linear process is now concurrent with integrated cost information as the Bill of Material is being built with real time pricing and availability, and push-button BoM analysis delivering reports on risks from obsolescence , lifecycle, compliance, lead-times and more.
Creating supply chain resilience for small and medium PCB design teams
The Supply Chain application, included with PADS Professional Premium, allows users to access real time component sourcing data from over 133 component suppliers and distributors, and this list continues to grow. It is available for any PADS Designer user, no matter what flow you use. All you need is an active subscription.
The component sourcing data for this application is powered by Supplyframe. Data such as pricing, availability, compliance, and lifecycle data, is presented in a tab of the Search window in Designer. Additional information such as links to datasheets for components are easily accessible by using the links provided. The tool even shows status indicators for components to alert the user to any potential risks, for instance if a component is out of stock at the supplier selected.
Watch our webinar!
To see a demonstration of the Supply Chain application, watch our on demand webinar.