Real-time Concurrent PCB Layout
In part one of this series on concurrent engineering, we reviewed the key features associated with a system that supports collaborative management of design constraints. In part two, we discussed how concurrent schematic design can increase the efficiency of engineering teams. Now we’ll move on to layout and examine how design teams can significantly reduce cycle time through real-time concurrent PCB layout.
The layout stage of new product development can easily be the most time sensitive phase of the overall project. Tasks like optimizing the stackup, satisfying design constraints, and routing high speed signals (to name just a few) can easily consume a significant amount of time and resources. To mitigate the potential for schedule slip, many teams assign multiple designers to work together on the PCB layout. Historically, in order for the designers to collaborate on the layout, a manual partition and reassembly of the PCB was employed. The problem with this approach is that partitioning and reassembling a design object such as the layout can be a complex process, limited in application, and subject to error. As such, the potential to reduce cycle time will vary, depending on the overhead of the approach. In order to truly reduce cycle time during PCB layout, more sophisticated tools are required; ones that allow multiple team members to contribute to the layout design simultaneously. The key features of a real-time concurrent PCB layout system include:
- Multi-user concurrent access – Support for multiple designers concurrently accessing the same layout without the need to partition or divide the board. (Figure 1).
- Real-time restriction of areas under edit – An area or region that is being edited should be restricted in real-time until the edits in the area are completed. The user performing the edits in the area should be displayed to all other users viewing the area.
- Real-time visibility of edits – As design objects such as components and traces are placed/added, moved/edited, or unplaced/deleted, the edits should be visible in real-time to all users.
- Support for concurrent autorouting – When autorouting is required, the process can be distributed across multiple machines thereby using the multiple CPUs to generate faster routing results.
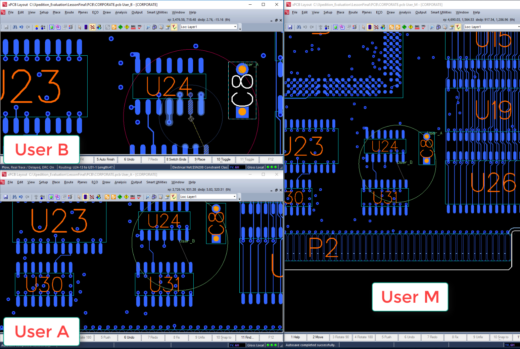
In the real-time concurrency approach supported by Xpedition, multiple PCB designers can work on the same layout simultaneously. There is no need to partition, divide, or define exclusive areas for each designer. Designers can share the entire board to work in a collaborative manner, while a server coordinates the individual transactions. Xpedition force field functionality manages priorities when multiple users are working in the same area. The more work a user performs in an area, the larger that user’s force field. If the user moves to a new area of the board, the size of their force field reduces. When a user is changing an area of the board that user owns that area. Any attempt by other users to perform edits in an area which they do not own are prohibited.
A short video demonstrating real-time concurrency during PCB design along with a PCB layout datasheet are both available for more in-depth information.
We will conclude this concurrent engineering blog series next time with a discussion on concurrency across tools (as opposed to concurrency within tools). Please be sure to check back in a few weeks!