What a PCB designer needs today for schematic definition
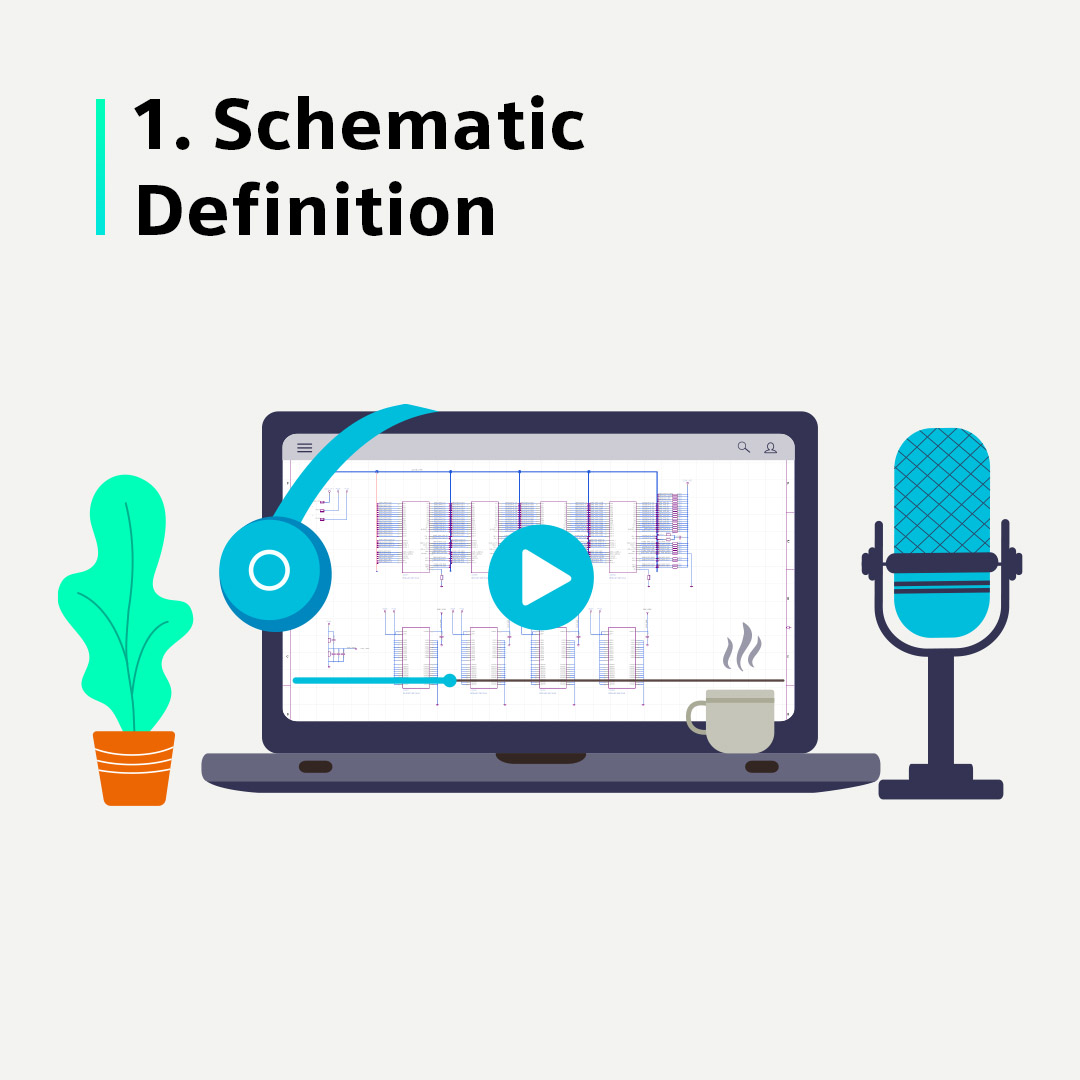
What’s really needed in a PCB design tool for schematic definition?
When I started out as an engineer, it was merely a three-step process: part selection, place the symbol down on a sheet, and connect them together. That said, today we are presented with new challenges, such as:
- IC technologies require more constraints.
- Large designs with thousands of components need to be well organized.
- Supply chain issues make it essential that engineers have insight into component availability.
As technology has gotten more complex, thankfully, our tools have evolved as well.
A schematic capture tool should have everything needed for design capture, but also have the ability to do component research and sourcing from within the tool. Simulation is a necessity on many designs. It may require pre-layout signal integrity planning, or access to other specialized analysis engines for analog/mixed signal, digital, and possibly RF design.
In addition, many designs I’ve seen are just huge – with an incredibly high page count, and multiple levels of hierarchy. Intuitive design navigation with complete hierarchical support is a must to be able to move easily throughout the schematic, both while designing the logic, but also when debugging a design.
All schematic tools should have easy point-and-click for interconnect the net traces to the parts. Interconnect automation can reduce the time to interconnect the design by speeding the connections to not only the components, but to hierarchal blocks as well.
With the complexity of designs increasing, and edge rates of components decreasing, the need to adhere to a complex set of electrical and physical design constraints is required. The most efficient way of capturing and managing these constraints is with a constraint definition tool with a spreadsheet user interface – a UI engineers are very familiar with. Since many designs within an organization and/or product family will have similar constraints, the ability to save and reuse constraints will reduce errors and the time needed to define and enter all constraints required for PCB design. And of course, these constraints must seamlessly propagate to the layout and simulation tools in your full PCB design environment.
PADS Professional Premium offers this and much more. It’s a full PCB design solution with not only schematic definition (with the above capabilities) and PCB layout, but also simulation and analysis, apps for component research, selection, footprints and symbols, and up to date parametric information about your BOM. Capabilities for advanced design are also included: RF, rigid-flex, FPGA/PCB optimization, and Multi-trace HSD routing.
Learn more about PADS Professional Premium and how it can elevate your PCB design process by downloading this eBook.