Bringing resilience at the point of design
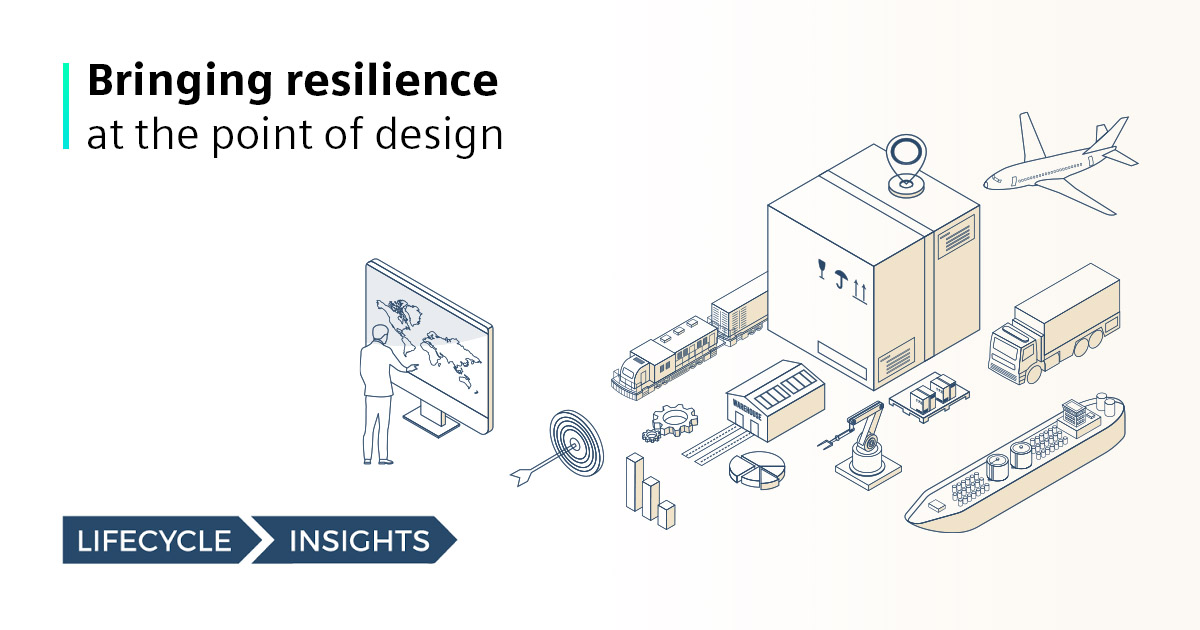
This blog was written by Chad Jackson, Chief Analyst & CEO at Lifecycle Insights, and comments have been provided throughout by Stephen Chavez, one of our own product marketing managers. Check it out and join the conversation below!
Designing complex products with electronic components has never been an easy task. But, a recent Lifecycle Insights study showed that companies are having to replace components more than 25 times per design thanks to a lack of component availability or component lifecycle or compliance issues. That’s why it’s more critical than ever for manufacturers of electronic products to have access to accurate and reliable component supply chain electronics intelligence. When companies have real-time intelligence into the component supply chain, it helps ensure the components they need are available, verified, and within budget when it comes time to fabricate a design.
Why supply chain electronics resilience is necessary
Lifecycle Insights’ 2022 Engineering Design for Resilience (EDfR) Survey sought to shed light on electronic component sourcing and supply chain electronics issues. The findings revealed that traditional supply chain visibility had significant shortcomings, chief of which was real-time sourcing intelligence. A staggering 89% of engineers reported they had to remove or replace electronic components from their printed circuit board (PCB) designs due to unexpected supply chain disruptions.
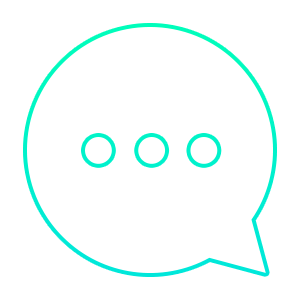
This high percentage of change due to supply-chain electronics disruption does not surprise me. In my recent U2U presentation and white paper, I share my recent experiences that directly relate to the struggles engineering teams are dealing with in today’s supply-chain disruption chaos and how it affects a company’s bottom line.
Stephen V. Chavez, MIT, CPCD, CID+ | Sr. Product Marketing Manager
In light of these findings, it is hardly a surprise that 84% of respondents noted that they are working to strengthen their supply chain intelligence. Those efforts include multi-sourcing, or looking to multiple vendors for a single component, instead of traditional single sourcing, and making targeted improvements to the processes their engineers use to select components. Companies are also having to expand their approved vendor lists (AVLs) to include alternate sources of supply. Their goal is to circumvent component supply shortages while also ensuring pricing targets are met.
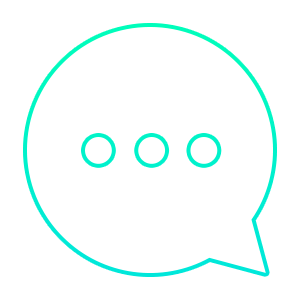
Supply chain intelligence is a term used and seen everywhere and by everyone now. I don’t agree with adding to your existing AVL as a solution to supply-chain resilience. I have major concerns with the thought of companies looking for ways to strengthen their supply-chain intelligence by simply adding to their existing AVLs. It’s not as simple as finding another resource (supplier/broker) to acquire a component from. Most companies have existing stringent supply chain resource requirements in place to filter out or categorize a supplier as they add to their existing AVLs. My hesitations/caution in the thought of expanding existing AVLs covers three specific areas:
1. Qualifications/requirements being reduced just to qualify a new vendor.
2. Lacking insight, background, or history of this unknow variable of a new vendor.
3. Potential of counterfeit parts, reclaimed parts or sub-par quality parts that may have originally been filter out by the manufacture yet makes its way to the black market and somehow makes its way on your CCA because you added a new supplier that magically comes up with stock when no one else in the industry has stock.
Stephen V. Chavez, MIT, CPCD, CID+ | Sr. Product Marketing Manager
Between a global pandemic, geopolitical tensions, and a variety of natural disasters, the electronics supply chain has gone through more than its fair share of disruptions over the past few years. And manufacturers’ reliance on electronic components to design and produce new products is only going to increase. The ongoing supply chain challenges have shown just how vital good intelligence is to mitigating the effects of supply chain disruptions—and reducing delays and costs along the way.
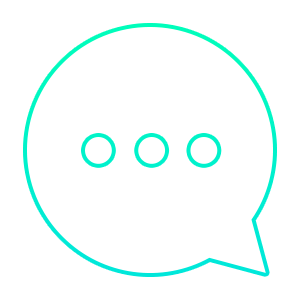
As I stated in the two-part article I wrote in Design007, this supply chain vulnerability had been problematic way before the pandemic, quietly growing, ignored until the pandemic hit with full force. Then, this sleeping dog raised its ugly head and now dominates today’s headlines. We see companies looking to improve legacy methodologies to bring intelligence at the point of design to increase the potential for success in mitigating delays and reducing cost.
Stephen V. Chavez, MIT, CPCD, CID+ | Sr. Product Marketing Manager
Blind spots in traditional supply chain processes
Historically, engineers have selected electronic components using a “throw over the wall” design flow approach. That is, the engineer will manually select specific design components without collaborating with other teams to ensure availability. Still working in isolation, the engineer creates a bill of materials (BOM) and then “throws it over the wall” to get the appropriate parts sourced. To get the necessary insights into availability and cost, engineers would look to Google or search directly on known supplier sites. They might also refer to internal databases from past projects to identify potential sources for the necessary components. From there, the design team and the supplier would use emails and spreadsheets to exchange BOMs.
This approach is woefully inadequate in the face of unprecedented supply chain disruption. Data is disconnected and not accessible to all stakeholders. Design tools and data systems are not integrated, so there is a lack of collaborative intelligence. The lack of integration also means that engineers will not be alerted when components become, or soon will become, unavailable. This disconnected approach also means companies will have difficulty optimizing costs when spot buys are required for alternate parts.
In larger companies, design engineers select components and then create a BOM to pass over to the new product introduction (NPI) engineer for further refinement. In smaller companies, the BOM created by the design engineers is often directly submitted for purchase, without any further input from downstream teams. In both cases, when component decisions can be made early in the design phase, supplier price and availability issues will not be as volatile.
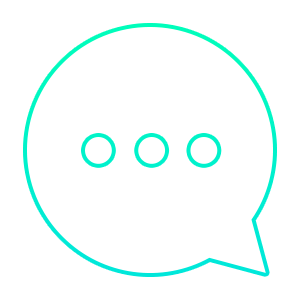
Based on my experience, I can attest to this complex network of communication and functions inherent to both larger corporations and small businesses. While larger corporations are typically a conglomerate of absorbed smaller companies spread across the globe, smaller business tend to function with key individuals wearing many hats to get the job done. In my recent white paper, there are two images that come to mind: Figure one which is an excellent depiction of the spiderweb-like network of the challenges that span functional silos, disparate systems, and fragmented cross-functional decision-making processes, and Figure five which depicts today’s current state of the design and sourcing process that lacks the design for reliance.
Stephen V. Chavez, MIT, CPCD, CID+ | Sr. Product Marketing Manager
How cross-functional supply intelligence works
Traditional component selection processes offer limited insights into the future availability of a part. The design team is the predominant driver of component decisions—and if a part becomes unavailable after design is complete, issues will arise. Today, as manufacturers try to manage the risks inherent to an unpredictable supply chain, taking a cross-functional approach to supply intelligence has become a necessity. In such an approach, all stakeholders have visibility into the component change and the possible implications of that change, which can impact everything from mechanical fit to emissions compliance.
Cross-functional supply chain electronics intelligence provides real-time insights into component availability and cost data. In addition, it also alerts teams when supply issues emerge so they can be addressed when the cost of change is still manageable. Companies that have access to cross-functional supply intelligence can better ensure design teams, suppliers, and manufacturers are aligned and that they have the visibility and insights required to manage the risks involved with component selection.
When there is a lack of cross-functional intelligence, manufacturers will likely experience:
- Delays in design and production, as well as product time-to-market;
- The need to engage in expensive spot buys; and
- Data changes that are more likely to cause errors or fail to satisfy design requirements.
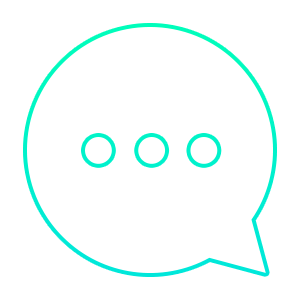
I agree that today’s legacy methodology lacks cross-functional intelligence. Important stake holders and vital intelligence are brought in to late in the process. Bringing both to the table earlier in the process is key for success. This includes both external stake holders and the external intelligence. What has been missing from legacy processes is bringing of that intelligence further upstream in the process… to the point of design so that intelligent decisions can be made upstream while having a positive influence downstream to gain the highest potential for overall success.
Stephen V. Chavez, MIT, CPCD, CID+ | Sr. Product Marketing Manager
Accessing design intelligence to start
When companies have access to real-time supply chain intelligence, they can navigate supply chain issues as they arise all the way through the design flow, from concept through manufacturing. With design-to-source supply chain intelligence across the entire design flow, all engineering disciplines are positioned to react to issues as early as possible. This helps to mitigate the kind of risks that lead to substantial delays and expensive spot buys. When engineers can see what is happening in real-time, they can make changes when costs are lowest.
Companies whose design flow includes integrated supply chain intelligence can identify issues, respond quickly, and better manage risk, even when they are hit with unexpected circumstances during design and production. Supply-chain-connected design flows can also help manufacturers lower costs by eliminating last-minute supply issues and corresponding spot buys, which, in turn, eradicate design cycle time and rework.
Mitigating supply chain electronics risks
The last few years have shown the importance of supply chain resilience. One of the first steps to achieving it involves gaining access to timely and reliable component supply chain intelligence. As products evolve to include more electronic components, engineers need to find ways to avoid design delays and expensive spot buys when those components become unavailable. Progressive manufacturing organizations are looking at new technologies and processes to implement cross-functional supply chain intelligence. In doing so, they can mitigate risks involved with supply chain disruptions, and ensure they can acquire the electronic components they need while still meeting key deadlines and staying within budget.
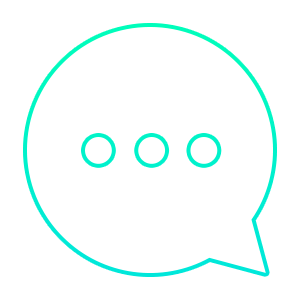
Let’s face it, legacy methodologies have gaps. Prior to the pandemic, we managed to be successful even with these gaps. The pandemic opened our eyes to an issue that has been there all along. It has affected us all, one way or another. Now, we need to be open to adopt new methodologies so that supply-chain resilience is built into our processes to successfully adapt to economic pitfalls that may present themselves and to better manage risk.
Stephen V. Chavez, MIT, CPCD, CID+ | Sr. Product Marketing Manager