New machinery isn’t the only way to meet high-mix, low volume PCB demand
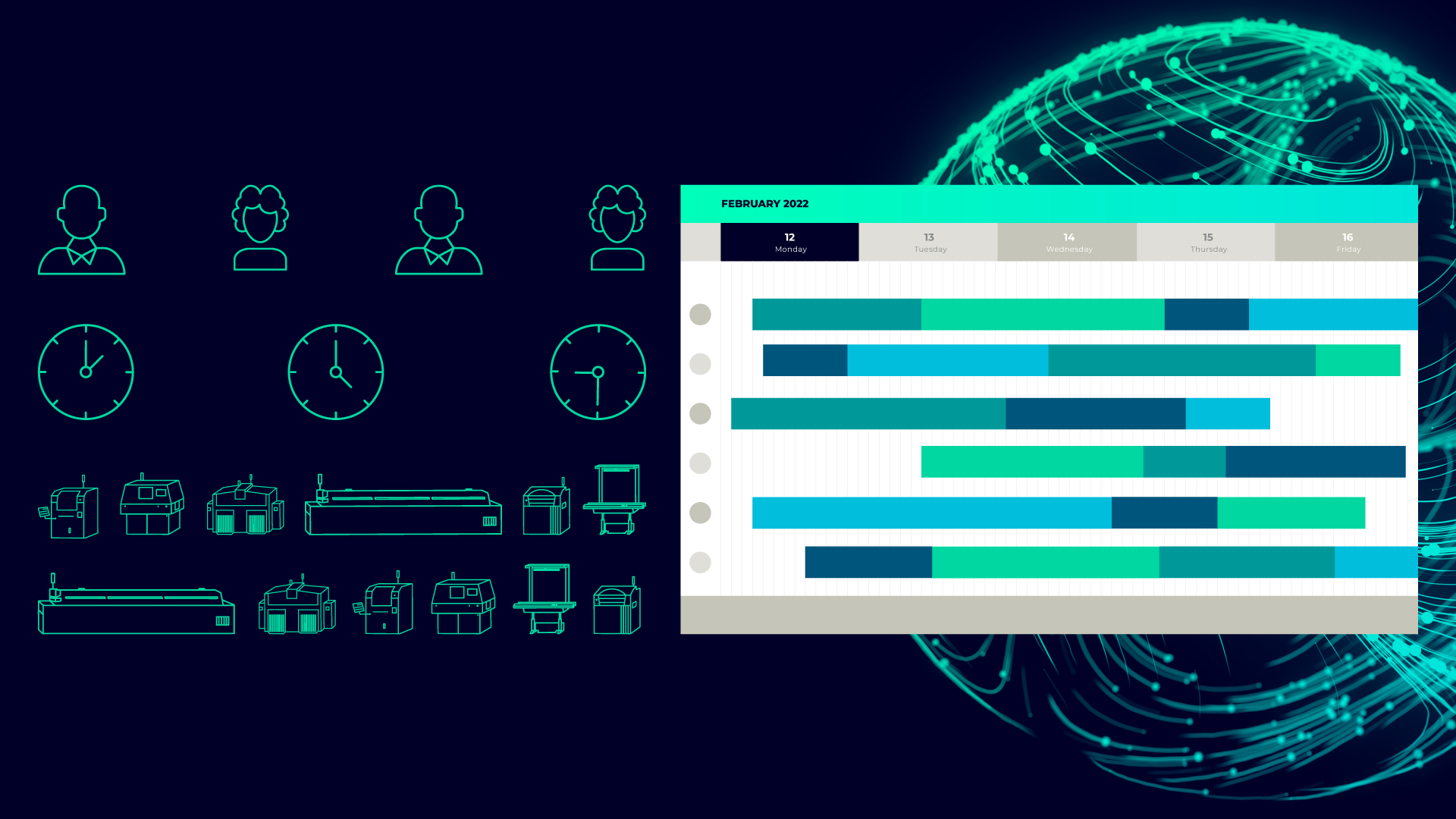
PCB manufacturers face market demands for a high mix of products, low volumes, low costs and fast delivery, leaving them feeling like there’s not an option but to invest in new production machines. But, before investing in expensive new machinery, manufacturers should evaluate whether they can make better use of their current production infrastructure to improve yield. In many cases, a dynamic scheduling solution for electronics manufacturing can help improve resource use and unnecessary machine purchases.
Learn more about four methods to increase the use of existing machinery and infrastructure:
1. Know how your current scheduling process reacts to changing variables
With high-mix, low volume production, long-term planning can be challenging. Constantly introducing new variables into the equation impacts how and when to produce work orders. Manufacturing production planners need to consider all of these variables to get a clear picture of the production schedule.
To better manage these variables, capacity planners need to define the constraints: factory layout, machines, feeder setup changeover policy, operators, work orders allocation and production sequencing. But, managing variability and limitations using a whiteboard or spreadsheet is challenging due to the number of combinations possible. Because it is challenging to optimize production, manufacturers often assume overall capacity is the limitation, forcing possibly premature investments in plant expansions and new machinery.
2. Use a scheduling solution for PCB production to improve resource use
Electronics manufacturers can leverage software explicitly designed for scheduling PCB production to improve resource management. These solutions create optimized manufacturing schedules based on customer orders (variables) while considering production constraints such as line capacity and operator availability.
For these software programs to be effective, they must be able to receive critical parameters and consider the unique requirements of surface mount manufacturing (SMT) lines. At a minimum, systems should include automatic input of work orders, constraint definitions, material management, and ERP interfaces.
3. Remove unnecessary, manual error-prone processes
Production schedules constantly change, so electronics manufacturers need to control data flow. Ideally, manufacturers handle the data exchange automatically and avoid manual updates. For example, the bill of materials (BOMs), work orders, and material availability status change frequently. Constant updates between the ERP system and the production scheduling software are needed to keep up with these changes. Without integrated software solutions, the process requires manual updates—an error-prone process that costs time and money.
4. Reduce changeover times in PCB production
One of the simplest and most effective ways to improve productivity is to reduce changeover times. Reduce setup counts in the schedule and refine processes to minimize the time needed to prepare setups. Powerful algorithms can optimize planning and enable the production of different products without changing the materials currently mounted on the machines.
Learn how dynamic scheduling can significantly improve production yields with existing infrastructure.