Ten tips for streamlining PCB thermal design
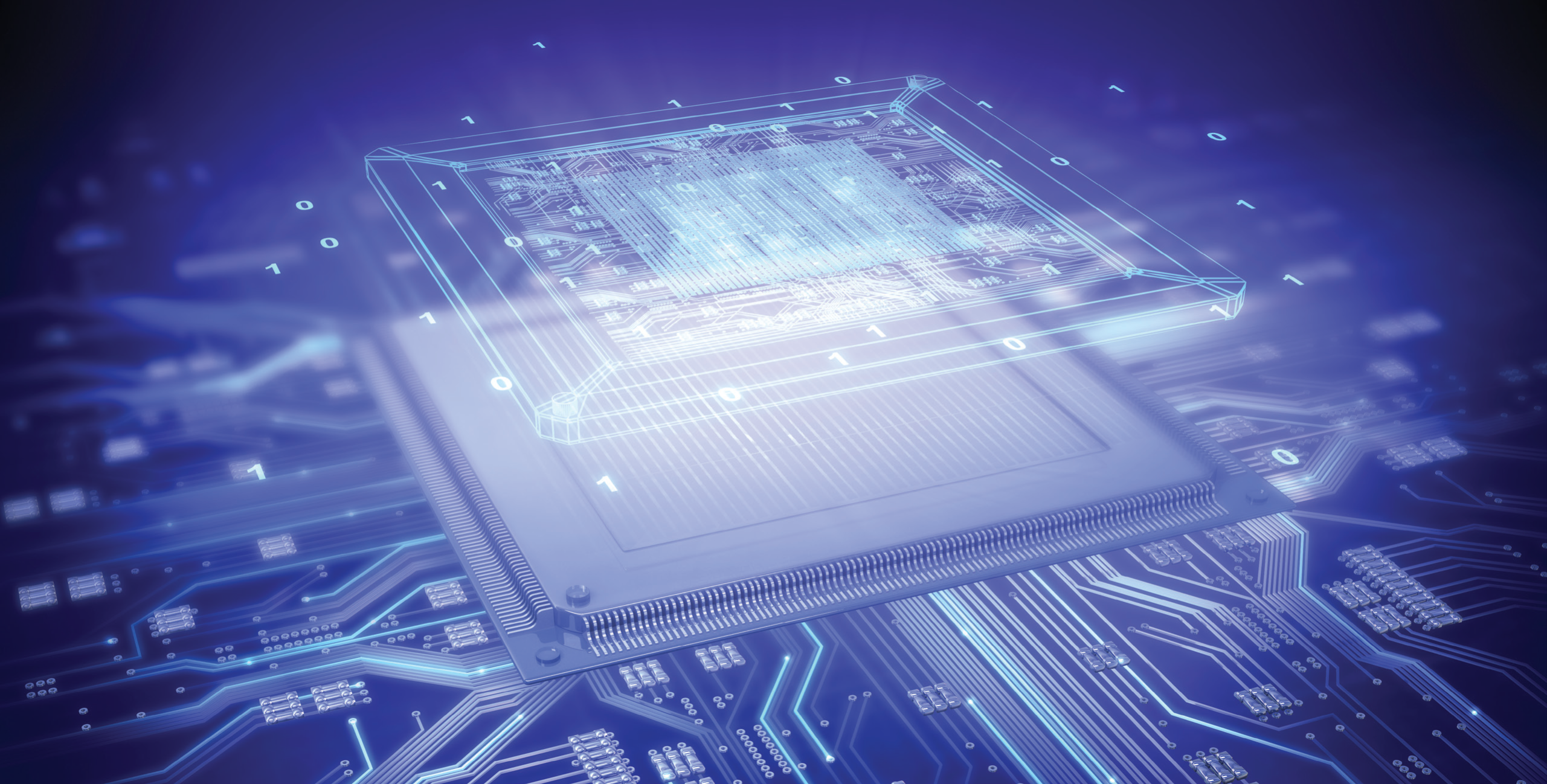
Leveraging a parallel PCB thermal design approach for faster design closure
The detailed design phase determines many aspects of printed circuit board (PCB) performance, for example, making a trace a specific length for timing reasons. Temperature differences between components can impact timing issues. PCB design thermal issues are locked in during the component (chip package) selection and layout phases. After this point, only remedial actions are possible if components run too hot. By starting at the system or enclosure level, designers can understand the flow environment for the electronics, which is critical for air-cooled electronics. Assumptions made about the uniformity of the airflow in early design that subsequently prove unachievable can have a disastrous impact on the product’s commercial viability and meet the market window.
Mechanical engineer’s role in optimizing the PCB thermal layout
The mechanical engineer is primarily responsible for the thermal integrity of the product and should aim to provide as much helpful feedback as possible to the electronic engineers to guide the design about the thermal impact of their choices, especially during early phases. From the mechanical engineer’s perspective, this entails helping with package selection and the best positioning of components to utilize system airflow for cooling at the PCB level. Both layout and package selection are driven primarily by electronic performance and cost considerations. Still, mechanical engineers should share the consequences of those choices on thermal performance, as temperature and cooling also affect performance and cost.
Enable mechanical engineers to share input earlier in the design process to increase thermal performance and prevent costly changes later. Designers can optimize PCB performance during the thermal design phase by starting early collaboration:
- Provide the most relevant thermal metrics to compare the performance of candidate components
- Help with package selection and the best positioning of components to utilize system airflow for cooling
- Leverage a parallel approach for faster design closure, better reliability and a better outcome than a single flow
Optimizing the thermal layout by starting early and simple
Here are ten ways to streamline PCB thermal design:
- Start pre-placement/pre-layout
- Get component power (guesstimate)
- Use 3D component models before package selection
- Share thermal results
- Size heatsinks early
- Represent the component accurately
- Don’t ignore the board detail
- Import data from the EDA system
- Move PCB thermal design up the design flow
- Undertake co-design with the EDA flow
If you’re responsible for PCB-level thermal design and want to know more, download the high-level how-to guide!