The electronic manufacturer’s guide to mastering material flow using intralogistics
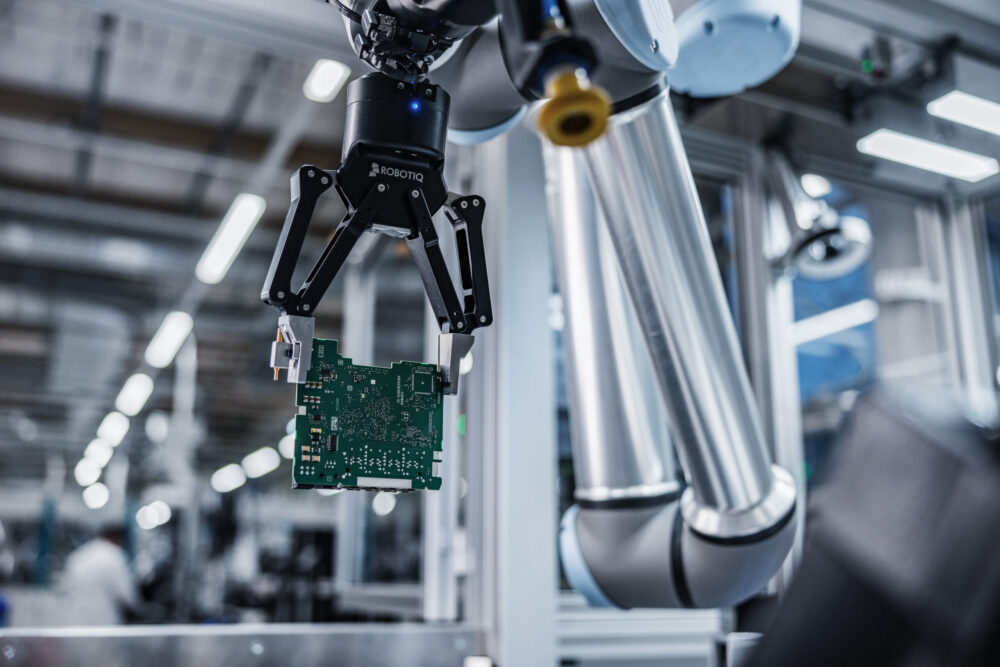
In electronics manufacturing, efficiency is critical to competitiveness. Optimized intra plant logistics or intralogistics can revolutionize how manufacturers handle materials, streamline processes, and help them unlock new levels of efficiency.
What’s intralogistics or intra plant logistics?
Intralogistics is the management of material movement and handling within a manufacturing facility. It involves material storage, transportation, picking, and delivery, to ensure a smooth and seamless flow of materials from one production area to another. By leveraging real-time visibility, efficient resource allocation, and accurate order fulfillment, companies can streamline their material flow, reduce costs, minimize bottlenecks, and enhance overall productivity. Let’s review four use cases for better intralogistics.
#1 Right place, right material and at the right time
Real-time visibility gives manufacturers instant access to material availability, location, and status information. Real-time visibility allows for better decision-making, efficient resource allocation, and proactive management of material flow. Manufacturers can prevent delays, streamline processes, and respond swiftly to changing production demands.
#2 Reduce side inventory and delivery only what is needed
Without the excess inventory on the shop floor, manufacturing teams can deliver production material quantity based on work-in-progress (WIP) or with just in time (JIT) replenishment. They can also plan logistics along the production plan and according to capacity, using shopfloor WIP updates from the machines or manufacturing execution system (MES).
#3 Increased production efficiency and product quality
Increased production efficiency and product quality reduces the risk of errors, returns, and rework, ultimately saving time and costs. Teams can optimize the changeover time, eliminate material counting and shuffling materials to and from the warehouse.
#4 Optimize logistic resource utilization
Optimized logistic resource utilization provides manufacturers with a clear understanding of material requirements and availability, enabling them to optimize the allocation of resources, such as workforce, equipment, and storage space. This optimization ensures that the right resources are deployed at the right time and quantity, eliminating unnecessary waste and reducing costs. Manufacturers can also better plan their production schedules, minimize idle time, and improve overall operational efficiency (OOE).
With the right intra plant logistics or intralogistics technologies, best practices, and industry expertise, electronics manufacturers can unlock the full potential of their operations and pave the way for sustainable growth and success.
Want to learn more about intralogistics? Watch the full Intralogistics solutions give electronics manufacturers the tools to master material logistics throughout the plant webinar.
About Siemens Opcenter IntraPlant Logistics
With the Opcenter Intra Plant Logistics solution, you can increase line performance, maintain inventory accuracy and ensure seamless material flow between the warehouse and the shop floor. Learn how to revolutionize your electronics manufacturing operations with Opcenter IPL.