Semiconductor Industry Report: Mid-2023 Trends and Insights
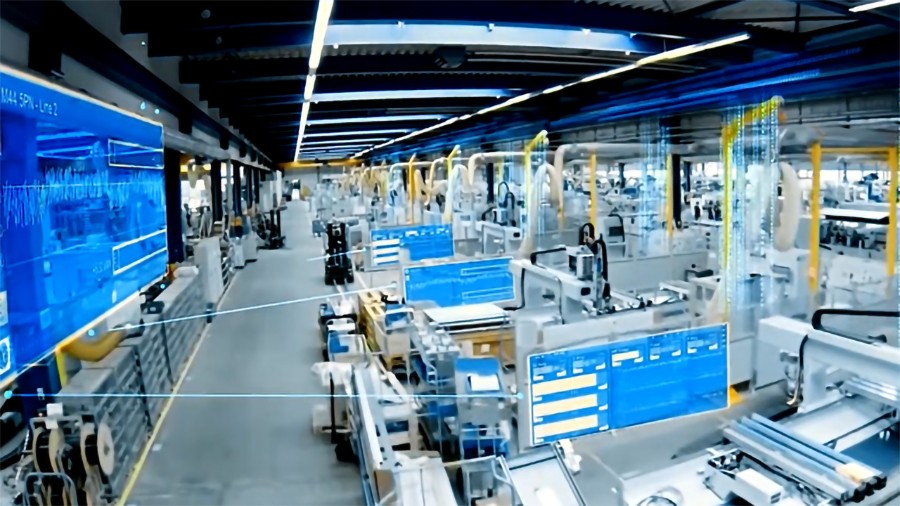
Summary An explosion of complexity is happening in the semiconductor industry. Digital solutions provide a key opportunity to harness this complexity for a competitive advantage by allowing manufacturers to move more quickly, with higher accuracy and deeper insights of knowledge. The stakes are high. Winners will win big, and the losers will be gone – and gone fast.
For most of 2021 and 2022, we heard about semiconductor chip shortages impacting several industries, particularly automotive. Vehicles were being held up for months, waiting for chips so they could be shipped to customers. Over 11B vehicles were not shipped in 2021 due to the chip shortage, costing automotive companies over $ 200B in lost revenue. Now that we are halfway through 2023, let’s look at some key trends for semiconductor manufacturers that are shaping their business strategies – today and into the future
1. The Semiconductor Supply/Demand Roller Coaster
Many of us have seen this movie before – semiconductor cycles have been part of this industry almost from the beginning. At a macro level, we are now 6+ months into an overcapacity situation. At the lower levels – looking at fabs – you see a mixture of both over and undersubscribed loading. And everyone is trying to predict when it will flip again.
This uncertainty puts pressure on two fronts. First, forecasting, demand planning and capacity investments can be very tricky, particularly during inflection points of the cycles. Compounding this is customer’s plan to accelerate new product launches – often in new manufacturing technology nodes – to get or maintain a competitive edge coming out of downcycles. Second, materials planning for items such as chemicals, gases, and rare earth minerals becomes more difficult. Recent global supply chain issues don’t help this situation either. For example, photolithography is an important step in semiconductor manufacturing which allows for patterning of circuits on to a wafer. It requires a special grade of neon gas that up until last year, approximately 50% of the world’s supply came from Ukraine. Since the Russian invasion, manufacturers have had to scramble to stockpile and find alternative sources. Manufacturers will need not only advanced planning and scheduling systems to simulate various market, customer, and supplier scenarios, but a quick, reliable, and efficient manner to convert the scenarios to manufacturing execution plans.
2. What’s Different This Time? The Diversity of Demand!
While some things are the same, there are some things changing in our industry. The profile of demand mix in the industry is different. The industry is still heavily reliant on smartphones and PCs and their demand decline has driven this latest downturn. But demand is increasing in areas emerging industries [FA8] such as automotive, data centers, and aerospace and defense. Many are looking to the diversity of demand to help drive the recovery and even potentially smooth out some of the dips moving forward.

This diversity of demand brings with it some additional challenges. There are stricter technology requirements for things like zero defect reliability and wider operating temperatures. Product lifecycles in industries like automotive look very different – longer to ramp up, but shipping for 10 or even 15 years. Manufacturers will need robust, integrated manufacturing and quality systems to handle functional safety, with high levels of traceability from final product all the way back to design and requirements management.
Even the business engagement models are changing, with many of these emerging industries looking at vertical integration – doing their own chip designs and interacting directly with foundries to better differentiate, save money, and have better control over their supply chains. This direct interaction will also drive closer integration of processes between OEM customers and foundries. Digital transformation will not only be inside companies, but will encompass suppliers and customers as well.
3. Integration Through Advanced Packaging
There are other dynamics shaping our industry today as well. You have a split of manufacturing technology roadmaps. Products like processors and memories continue to drive advanced technologies, although design and manufacturing costs are increasing rapidly as nodes go below 7 nm. But a lot of support chips like RF, power amplifiers, power management, and sensors are still using older technologies. Today’s electronic systems continue to need more and more levels of system integration, which means using a combination of SoC (System-on-Chip) and SiP (System-in-Package).
Putting chips built in different technologies together in a single package has significantly driven up package complexities. These heterogeneous packages now require EDA level software tools for design, simulation and checking. It is also blurring the boundaries between front end (wafers) and back-end (packaging and test). Fabs are investing in packaging technologies and OSATs (Outsourced Semiconductor Assembly and Test) are investing in simple fab processing. Wafer manufacturers will need to actively consider advanced packaging as part of their technology solutions, from design enablement to stronger partnerships with OSATs.
4. Welcome To the World of Geo/Politics and ESG
The semiconductor industry has long benefited from global optimization of its supply chain, from design of products through manufacturing and assembly. With semiconductors playing an increasingly critical role in such sensitive infrastructure areas like AI, 5G, and defense, political pressures and national security concerns have driven countries and regions to think more about onshoring design elements like intellectual property and parts of the supply chain, particularly fab manufacturing.
The U.S. has started the application stage for funding from the $ 52B U.S. Chips Act. Similar activities are going on in Singapore, S. Korea, France, Germany, and elsewhere. This de-globalization will likely have some negative consequences, such as increased costs and countries having to come face to face with some of the sustainability challenges of semiconductor manufacturing – like the need for large amounts of water, energy, and dealing with toxic materials, chemicals, and gases. Manufacturers will need to balance their optimization efforts with the constraints of onshoring pressures.
5. Workforce of The Future
The increased focus on semiconductors is driving a renewed need for skills and talents. By 2030, it is estimated one million additional skilled workers will be needed. Corporations have started to work with universities to develop programs and training to hopefully produce a pipeline of much needed resources for this growth. But it will take time and it will have to adapt for fabs of the future – incorporating AI, analytics, and software skills. Key to accelerating the connection between computer systems and humans will be the usage of techniques such as mixed reality and no code/low code software solutions. Both make it easier and more intuitive for people to tap into the power of industrial automation.