Capital Asset Lifecycle Management Helps Companies Reduce Costs
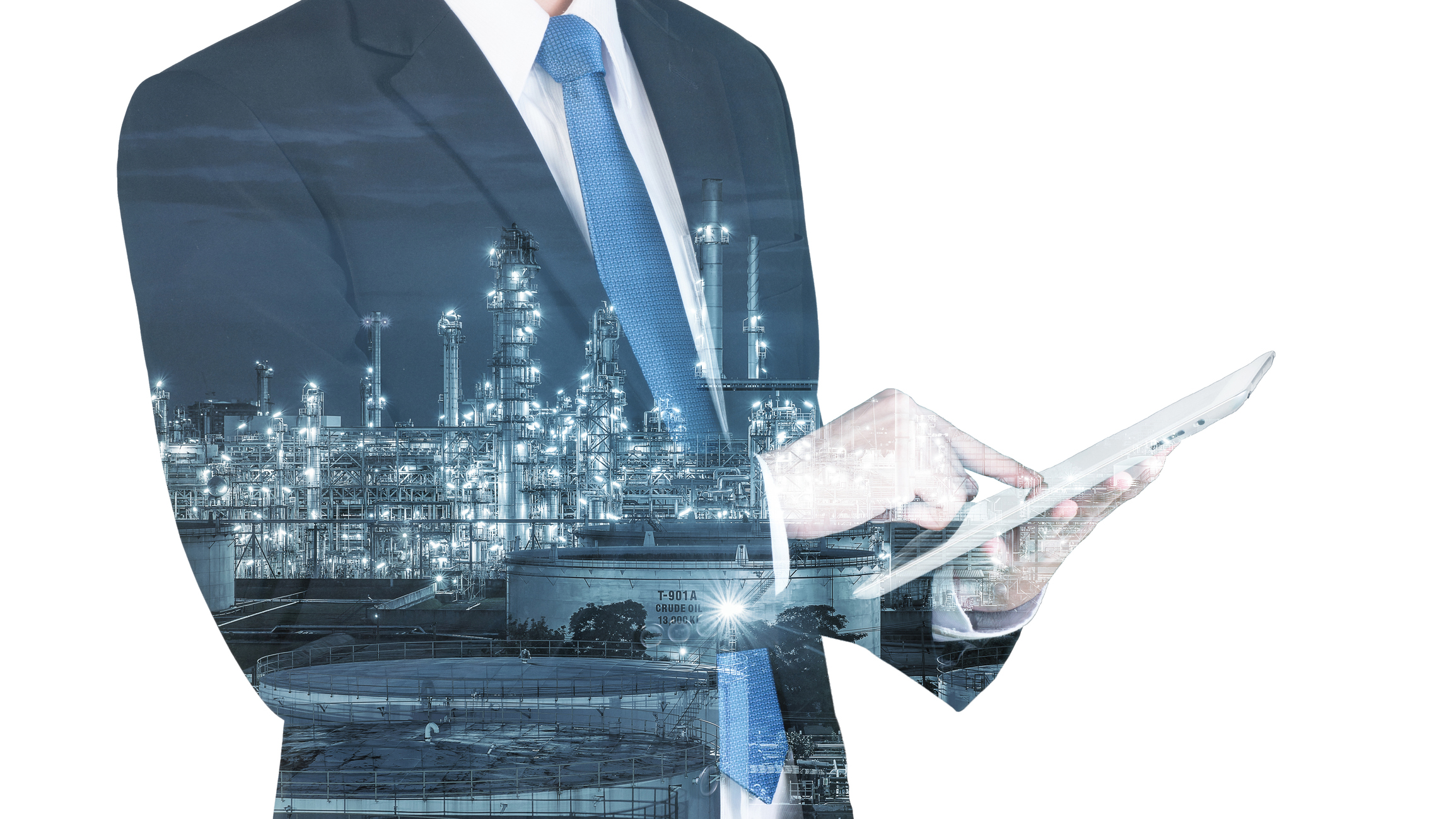
In February 2020, millions of Texans were left without power when a severe winter storm nearly took down the entire state’s electric grid. The power generating capacity in Texas simply could not keep up with demand as thousands turned up their heaters to combat the frigid temperatures. The weaknesses revealed in the storm aftermath have magnified the need for energy and utilities (E&U) companies to improve infrastructure and manage the lifecycle of their assets while remaining cost-effective.
E&U companies can benefit tremendously from improved processes. For example, a nuclear power plant can significantly reduce carbon emissions and energy costs by using cogeneration technology to combine usable heat and electricity into a single process. Additionally, simulation or 2D and 3D design tools can improve a plant’s operations to use fewer capital assets to generate the same amount of electricity.
Now more than ever, E&U companies must be strategic and efficient to survive. By streamlining processes and adopting digital analytics tools, organizations can enhance decision-making and save on maintenance, rework and operational costs. The savings can then get recycled back into the asset to improve production and operations continuously.
E&U companies need an effective capital asset lifecycle management system to maintain safe and dependable operations, meet emissions goals and get the most value from their assets.
Leveraging Capital Asset Lifecycle Management
Organizations pour a large portion of their funds into capital assets. In the E&U industry, gas pipelines, wind turbines, infrastructure, manufacturing equipment and the people running them are all considered capital assets. Unfortunately, many stakeholders involved in the design, construction, and operation of capital assets have been hesitant to adopt digitalization in their management processes.
Without the improved interoperability that digital tools provide, these stakeholders struggle to collect, manage, and trace operational data at an enterprise level. Because of this, most businesses experience efficiency losses in capital project delivery and throughout the entire asset lifecycle. To put this in perspective, a McKinsey & Company report found that 98% of megaprojects incur cost overruns or delays, leading to an average cost increase of 80% and delayed project delivery by 20 months. Without addressing these issues, the inefficiencies get passed down to the operator, where they can exist for years.
Capital asset lifecycle management encompasses a holistic view of all assets used across an entire organization. For example, it can account for all the usage of one piece of equipment, from purchase and implementation to disposal. It also allows businesses to manage buildings, machinery, equipment, projects and data from one central location.
Using one location for data exchanges and collaboration helps E&U companies establish greater efficiencies to save time and improve decision-making. While document-driven processes are capable of handling capital asset lifecycle management requirements, the most productive systems leverage cutting-edge software.
Siemens Capital Asset Lifecycle Management Solutions
In 2019, Siemens Digital Industries Software and Bentley Systems teamed up to develop Capital Asset Lifecycle Management (CALM) for Teamcenter software to help E&U companies face the challenges of today’s energy market. The software offers solutions for the planning, design, construction and operation of a plant or asset.
With a capital asset digitalization strategy, businesses can increase efficiencies across an entire organization and optimize operations using a digital twin. Companies can digitize their capital assets as early in the lifecycle as possible by establishing a data management system. The solution also enables the integrated distribution of project information from plant design, procurement and construction applications, allowing project teams to execute faster and collaborate in a more connected environment. Synchronizing asset design and information from contractors and subcontractors gives E&U companies the insight they need to increase risk management, reduce project delays and cost overruns while enhancing decision-making.
Maximizing Performance in Nuclear Reactor Production
Better decision-making begins with the collection of relevant data. Digital twins, automations and other advanced technology make this easier than ever. Candu Energy Inc., a leading full-service nuclear technology company, discovered just how beneficial this technology was when it implemented Siemens Teamcenter software to connect with outside designers.
Candu supplies nuclear power reactors and nuclear products and services to customers worldwide. They also provide plant management tools and maintenance services to existing nuclear power stations. CANDU reactors can operate for up to 60 years, with an outage at mid-life to replace fuel channels and repair or replace other key reactor components.
Candu began its designs using Solid Edge from Siemens Digital Industries Software. The company ran into problems working with outside suppliers that didn’t use the same design software. When Candu realized it needed a solution that could support various computer-aided design (CAD) systems, it selected Teamcenter solutions.
“Teamcenter provided a controlled and managed data-centric 3D and 2D environment. This allowed live collaboration during design reviews with other joint venture members and gave view access to the Candu manufacturing workgroups,” said Geoff Morgan, Candu Energy’s Chief Draftsperson.
Candu uses Teamcenter throughout its operations to create agility and remain competitive. It’s used in configuration controls to efficiently manage its CAD design files and has been especially beneficial for collaborating with suppliers and partners.
For example, Candu sometimes subcontracts parts of its designs to its vendors and partners to contribute to the overall mechanical design for its life extension projects. Teamcenter enables Candu and its vendors to collaborate and clearly understand each component’s configuration. This helps eliminate potential interferences in the integration of the tools. “We, as the integrator, are responsible at the end for the entire content, and Teamcenter enables us to do that with confidence,” says Eli Fayzenberg, Candu Computer-Aided Application Specialist.
Since implementing Teamcenter, the company has been able to significantly reduce costs associated with design rework and quickly comply with design requirements. This has been critical for meeting the Canadian Nuclear Safety Commission’s (CNSC) strict regulations, which require consistent documentation to the point that even a parameter for a specific water temperature must match—down to the degree—throughout the entire design process.
The company plans to implement even more Teamcenter capabilities in the future. Read more about Candu’s success leveraging today’s digital tools here.
Making the Most of Today’s Technology
An energy transformation is taking place, and E&U companies must evolve to remain competitive. Technology has been the most considerable advantage for organizations that strive to contribute to an efficient, cost-effective and clean energy future. Going forward, E&U companies will need to manage their capital assets to save costs where possible and add value through improved operations.
Siemens Capital asset lifecycle management offers data integrations using digital twins to help E&U companies manage change, streamline work processes, improve quality and safety, and connect to the supply chain. Learn more about Siemens Teamcenter solutions and Capital Asset Lifecycle Management here.