9 essential functions for your Manufacturing Execution Software (MES)
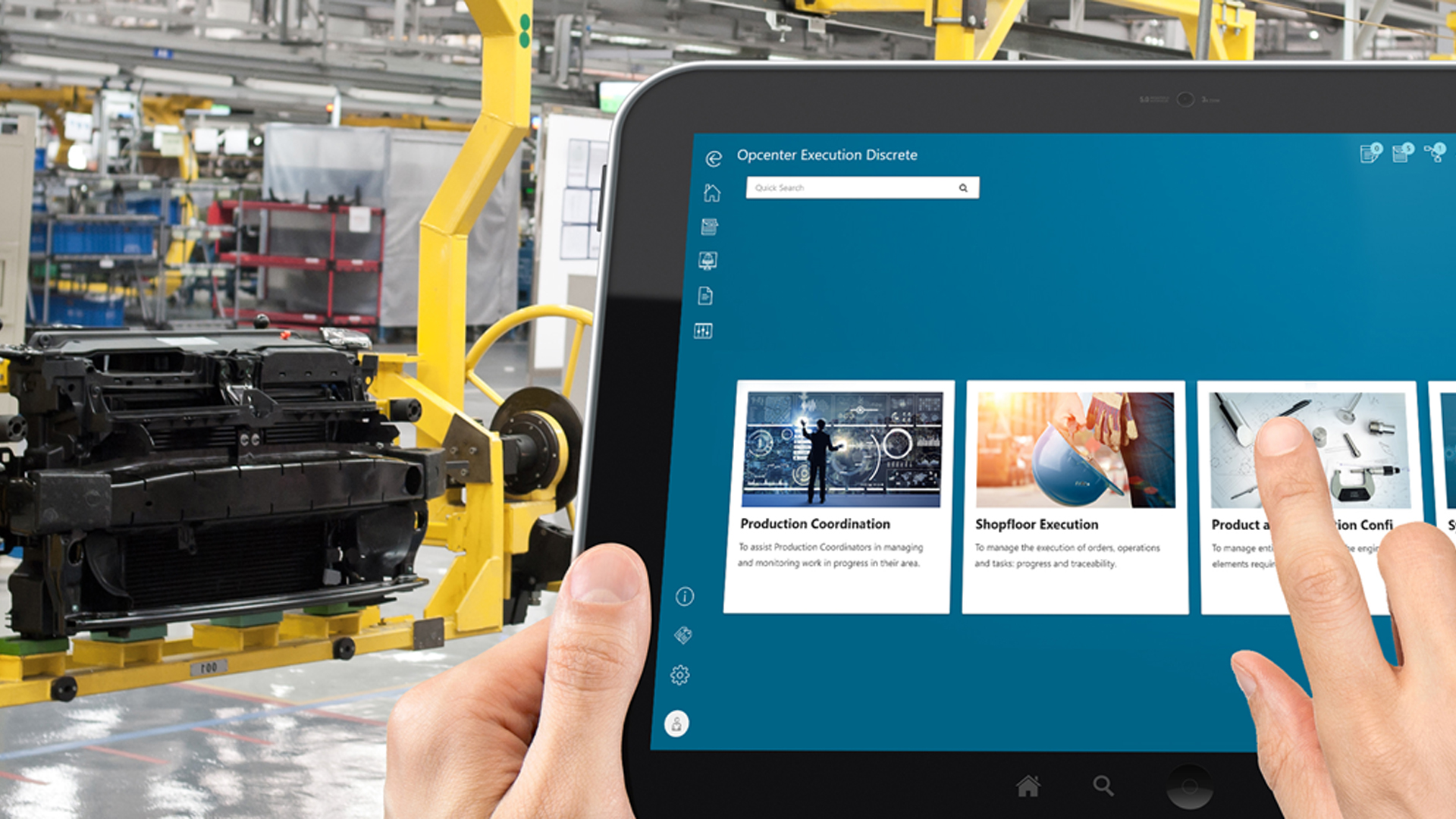
Manufacturing high-technology devices requires managing production complexity, maintaining and improving quality, reducing costs, and decreasing the time-to-market for new products.
Manufacturing Execution Software (MES) should be able to deliver all of this with the right features and integration.
The right MES solution includes at least 9 functions, all tailored to meet the needs of a complex job-shop organized factory:
1. Production process and flow control
An MES considers production operations, steps, material items and resources with accurate work-in-progress management of orders, operations, batches, and serial numbers. Additionally, distributing the workload among operators at shift start while taking their skills into account gives planners the ability to define teams of operators working on the same operations.
2. Manufacturing Execution Software integrated with Product Lifecycle Management PLM
When MES connects to PLM, it gives manufacturers the ability to create configuration-specific work orders based on variant processes, analyze the impact of changes on planned and running work orders, and expose plant resources from MES to PLM to enable manufacturing engineers to address correct data. An MES solution will also send nonconformance feedback to PLM.
3. Production route enforcement
An MES solution can optimize personnel from start to finish. Multiple different operator skillsets, operator time logging, production scheduling, and checking the accuracy of process steps execution can all be managed within the MES.
4. Execution management
Performed activities, part assembly, and tool usage all account for how something is manufactured. The right MES can display and track these things on a granular level to find ways for improvement. Additionally, users can check for part and tool accuracy and interact with external DNC systems for CNC part program transfers. Additionally, separate labor tracking on non-productive activities can give manufacturers a better idea of the true cost of products.
5. Tracking and tracing
Serial numbers, batch identifiers, and product tracking all play key roles for materials and products as they move across the manufacturing floor. An MES solution also centralizes reporting with as-built and genealogy reports in a single location.
6. Defect tracking and nonconformance management
The right MES should provide failure tracking, nonconformance lifecycle management, capabilities to manage and execute rework processes and leverage integration with a PLM to perform quality inspections.
7. Paperless manufacturing and reporting
Minimizing paper waste is made easy with electronic work instructions, data collection points, and support for barcode reading.
8. Electronic data collection
Manufacturing floors produce an enormous amount of data, and that data can be collected and used to provide valuable insights into the manufacturing process. An MES solution can be used to collect, store, and analyze all that information.
9. Additive manufacturing support
As additive manufacturing continues to grow and evolve, it’s important to have an MES in place capable of interacting with CAM systems to inject serial numbers into print file jobs and the ability to interact with 3D printers. Additionally, tracking and displaying powder material batch genealogy and substrate lifecycle are critical to additive manufacturing quality.
Get what you need from the right manufacturing execution software
Manufacturing Execution Software provides a significant return on investment, especially when solutions tackle some of the manufacturing industry’s biggest challenges out of the box.
Begin optimizing your entire value chain and improve efficiency, flexibility, and time-to-market with a holistic approach.
By digitizing their processes, manufacturers are better equipped to initiate or respond to disruptive innovation trends.
And once in place, the right solution begins working to solve common business problems, production challenges, and IT issues.
Read this white paper and learn more about Opcenter, a holistic automation solution covering every major Industry 4.0 requirement.
Frequently asked questions about manufacturing execution software
Q: How does an MES system specifically integrate with existing enterprise resource planning (ERP) systems?
A: MES systems integrate with existing ERP systems by using standardized communication protocols and APIs to ensure seamless data exchange. This allows for real-time synchronization of production data, inventory levels, and order statuses between the MES and ERP systems, enabling better decision-making and streamlined operations.
Q: What are the potential challenges or limitations in implementing MES in different types of manufacturing environments, such as discrete versus process manufacturing?
A: Implementing MES in different manufacturing environments can present challenges like adapting the system to specific production processes and workflows. Discrete manufacturing may require different functionalities and configurations compared to process manufacturing, necessitating tailored solutions to address the unique requirements of each environment.
Q: Can MES be customized to meet the specific needs of different industries, and if so, what customization options are typically available?
A: MES can be customized to meet the specific needs of different industries. Customization options typically include configuring workflows, data collection methods, and reporting formats to align with industry-specific regulations and standards. Additionally, MES vendors often provide industry-specific modules and templates to facilitate faster implementation and better alignment with the unique processes and requirements of various sectors.