Manufacturing process improvement: An introduction to smart manufacturing for industrial machinery
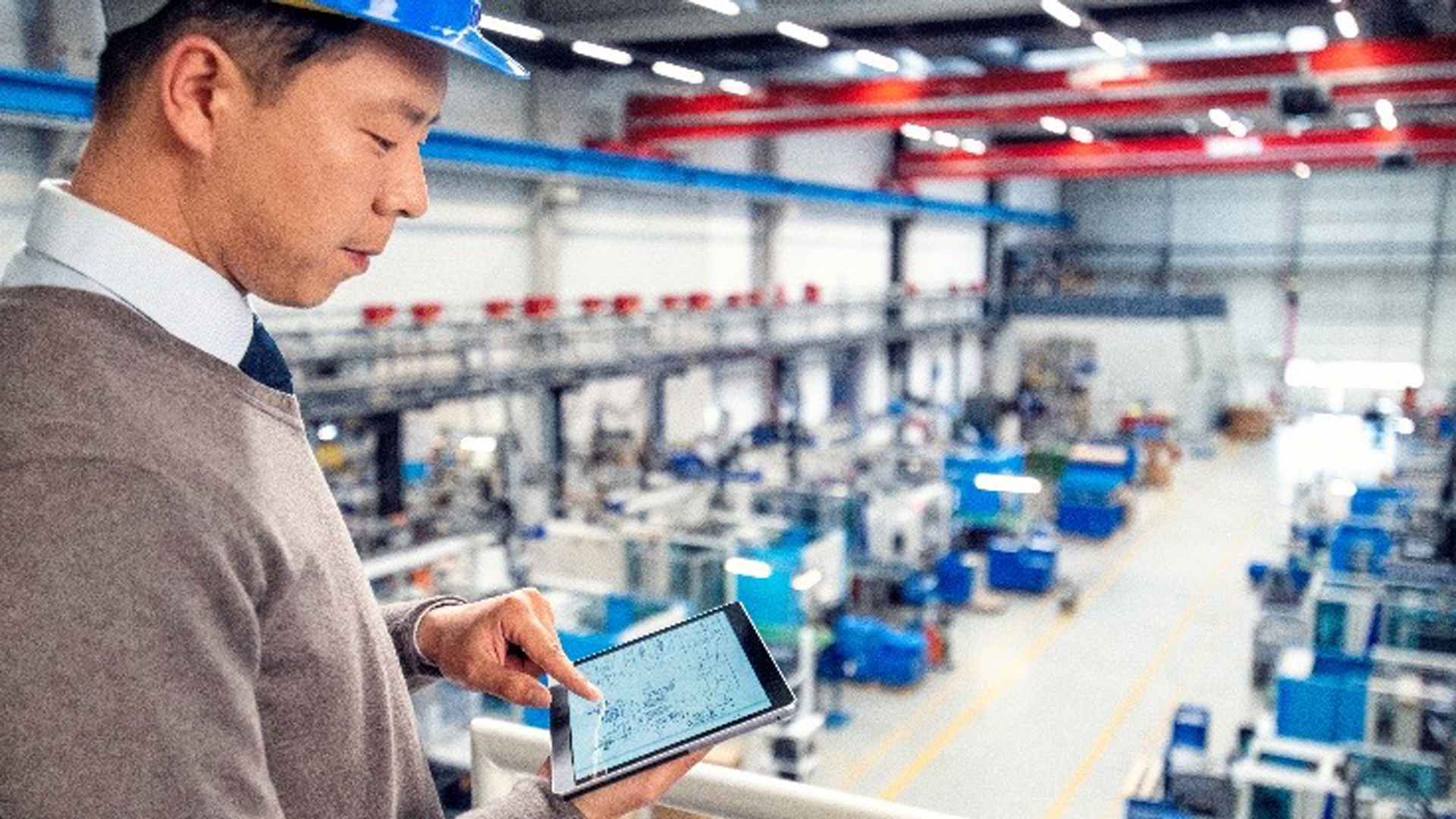
The industrial landscape is undergoing a seismic shift. Driven by globalization, technological advancements and changing consumer demands, manufacturers are facing unprecedented challenges.
To remain competitive and thrive in this dynamic environment, manufacturing process improvement is no longer optional, it’s essential.
Smart manufacturing adapts that changing landscape for your benefit. It’s a holistic approach that leverages cutting-edge technologies like the Industrial Internet of Things (IIoT), cloud computing, artificial intelligence (AI), and machine learning (ML) to transform traditional manufacturing processes.
But what exactly is smart manufacturing? In a nutshell, it’s about seamlessly integrating these technologies into your operations to achieve three key imperatives: Plan, Execute, and Optimize.
Get a better understanding of manufacturing process improvement with smart manufacturing in the infographic below:
Laying the groundwork for your success
Manufacturing process improvement starts at the beginning. It starts with a solid plan.
Imagine using digital twins to simulate and optimize your machines, processes and sequences before they hit the shop floor. Create smart, agile production lines and automation solutions cost-effectively using digital tools.
Integrate enterprise systems with manufacturing planning to optimize production processes with real-time data. Get early visibility into energy usage, downtime, throughput potential, and more.
Virtual commissioning tools streamline equipment setup and reduce downtime. Siemens solutions can help reduce commissioning time by a staggering 30 percent!
Executing seamless production with enhanced control
Now it’s time to put your plan into action.
Smart manufacturing streamlines execution by integrating regulations and safety standards for faster alignment. Improved quality becomes a part of the process without slowing it down through standardized automation and safety concepts.

Eliminate redundant tasks through process synchronization and foster seamless collaboration via the cloud. Without data silos, it becomes easier to increase process efficiency through improved end-to-end visibility of the entire production process.
The right solutions improve manufacturing efficiency and productivity.
Delivering continuous improvement through data-driven insights
The power of smart manufacturing lies in its ability to continuously improve. These digital solutions empower users to leverage data captured through virtual sensors and edge devices to identify inefficiencies and optimize performance.
AI and ML tools further enhance analysis, helping manufacturers reduce root cause analysis time by more than 50 percent and improve performance.
Ultimately, manufacturing process improvement leads to better product quality and design by embracing a closed-loop system that fosters continuous improvement.
Overcoming the challenges of manufacturing process improvement
Navigating the path to manufacturing process improvement is riddled with challenges.
Global supply chains demand intricate coordination, often hindered by disconnected systems and information silos. This lack of real-time visibility and control makes adapting to fluctuating demands or optimizing production a struggle. Setting up new machinery is time-consuming and disconnected systems create data islands that stifle improvement.
But smart manufacturing offers a lifeline for industrial machine, component and equipment manufacturers.
It connects data across the value chain and provides a single source of truth for enhanced visibility and control. Virtual commissioning reduces setup time while cloud solutions enable real-time collaboration and agility. Data-driven insights and predictive maintenance empower proactive issue resolution and consistent product quality.
By embracing this digital transformation, companies can navigate complexity and achieve lasting success.
Ready to embark on your smart manufacturing journey?
Manufacturing process improvement is an ongoing journey, and smart manufacturing provides the tools and technologies to achieve continuous improvement.
Embrace smart manufacturing and unlock the full potential of the machines, components and equipment your customers need to gain a significant competitive advantage in the ever-evolving market.
Siemens offers a comprehensive suite of solutions within the Siemens Xcelerator business portfolio of software, hardware and services that will guide you through each step of the process.
Frequently asked questions about manufacturing process improvement
Q: What are the specific steps and technologies involved in implementing a digital twin in a manufacturing process?
A: Implementing a digital twin in manufacturing requires data collection from physical assets using sensors, creating a virtual model of the physical process, and integrating AI and machine learning algorithms to analyze and optimize operations. This approach helps in real-time monitoring and predictive maintenance.
Q: How does smart manufacturing address cybersecurity concerns when integrating cloud computing and IIoT?
A: Smart manufacturing addresses cybersecurity concerns by employing robust security protocols, encryption, and regular vulnerability assessments to protect data and network integrity. This ensures the secure integration of cloud computing and IIoT technologies.
Q: What are the potential costs and ROI for small to medium-sized enterprises (SMEs) adopting smart manufacturing technologies?
A: For SMEs adopting smart manufacturing technologies, the costs typically include initial investments in hardware and software, training, and ongoing maintenance. The ROI is realized through increased efficiency, reduced downtime, and improved product quality. While initial costs can be significant, the long-term benefits often justify the investment, leading to overall cost savings and enhanced competitiveness.