Executable digital twin: when industrial IoT and simulation converge
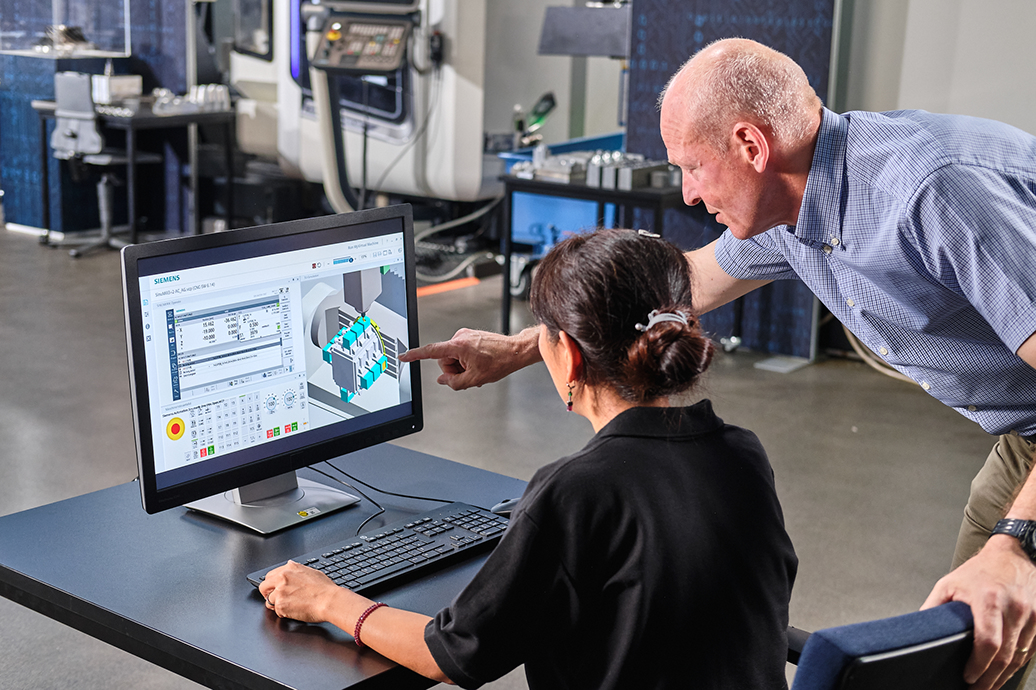
Leverage adaptable, secure and scalable xDT to drive operational excellence and gain competitive advantages
Digital twin is no longer science fiction. Companies has adopted to it if they do not want to fall behind development in their industry and their competitors as they embark on their digital transformation journey. But what exactly does digital twin mean? How can digital twins be used to create new opportunities for product development and manufacturing? What is the true maturity of industrial enterprises in implementing and leveraging digital twin’s invaluable potential?
What is the difference between digital twin and an executable digital twin?
The digital twin is a virtual representation of a physical object. It integrates all data, models and other information of a physical asset generated along its lifecycle. The role of the digital twin is to predict and optimize performance of the physical asset, by leveraging various simulations in the virtual world prior to implementing the right setup in the real world. While the benefit of simulation is obvious, on the other side of the coin the simulation models are sometimes large and resource consuming to execute, and then not able to provide information in real time.
The executable digital twin (xDT) is a reduced physics-based simulation model that is simple enough to be run in near real time, while still being accurate to represent the physical asset. They can be self-adapting and optimizing by continuously gathering data from field. They can be leveraged by anyone at any point of the product’s lifecycle on any certified device – from edge to cloud, without the need for heavy simulation software and infrastructure.
How does the executable digital twin affect the industry as a whole?
According to CIMdata, Siemens’ xDT advancement is an important step to making models relevant throughout the entire product lifecycle. “Siemens’ xDT is an innovation, we view it as a milestone in product design, production and utilization, as it transforms what was previously only a virtual copy of a product’s geometry into a working model that enables autonomous adjustments of the product within its actual operating environment and use throughout its lifecycle.” 1
xDT adds value to the entire product lifecycle:
- Design: improves product design by bringing “real world” data into the product virtual model, thus optimizing the product performance through various physics-based simulations.
- Production: improves production efficiencies by optimizing product design and performance specifications (bill of material), as well as the product manufacturing process, ultimately allowing for less interruptions in production, smooth manufacturing process and better product quality.
- In-service: improves in-service asset health, performance and output through real- time condition monitoring and predictive remote service.
Use case: high temperature monitoring for motor fast start scenarios
Large-scale electric drives are subjected to significant stress during startup due to induction heating. Motors can overheat if they are frequently started without adequate cooling time, resulting in unplanned downtime and increased operating costs. However, measuring the temperature of high-speed rotors within the motor is nearly impossible. xDT allows for continuous calibration using available stator-side sensors and virtual measurement of temperatures that are inaccessible to sensors. This significantly reduces cooling time for electric motors while increasing plant availability and optimizing operation costs. Meanwhile, it saves energy in two ways: reduced cooling time for electric motors and optimized operations.
Use case: overload monitoring of cranes in a nuclear powerplant
In a nuclear power plant, ensuring safety and preventing overloading are of the utmost importance. It is impossible to perform reliable predictive maintenance on a heavy-loaded gantry crane with a limited number of sensors. This could result in severe damage to such a sensitive area without maintenance. Smart virtual strain sensors are deployed at strain hotspots which allow to execute the xDT directly in near real time on edge devices on the shop floor, while sending data to the cloud to monitor the critical metrics and trigger/activate a predictive maintenance whenever required.
How does the industrial IoT empower the executable digital twin?
xDTs are not only deployed on edge devices or other local hardware systems connected to physical assets, but also in a cloud context. When a cloud version of the executable model is linked to the physical asset via the industrial IoT and integrated with solutions such as remote condition monitoring, near real-time product performance improvement becomes possible.
And because Siemens technologies are easy, open and flexible, here is our recipe for a simple/straight forward xDT implementation which could be applied to various industries and processes.
From monitoring to diagnosis to design improvement:
- Generate xDT: create your xDTs from 1D, 3D, flow, and other simulation models
- Monitor assets: deploy xDT in your IoT solution, where you can use near real-time data from sensors in the field to remotely monitor your fleet of assets against the xDTdefinition/KPIs/thresholds
- Events/anomalies: using xDT output as a benchmark, the IoT solution will generate an event to notify the engineer when an anomaly occurs or exceeds a threshold
- Root cause analysis: you can gain insights into asset performance by using IoT data and performing various physics based hi-fidelity simulations
- System optimization: optimize the system faster by leveraging xDT models of smaller and targeted parts of the system
- Design improvement: close the loop with design and engineering team by connecting to PLM
By leveraging IoT in xDT, business and operational systems become more transparent and optimized, which increases productivity, reduces design and development, improves product quality and performance, and enables the creation of new revenue streams.
Related Reading:
Digital Twins Calibrated with Operational Data Drive Efficiency
Manufacturers guide to closed-loop digital twins
Want to try Siemens industrial IoT for free? Start today with Start for free.