The industrial IoT power couple: Remote condition monitoring with remote service
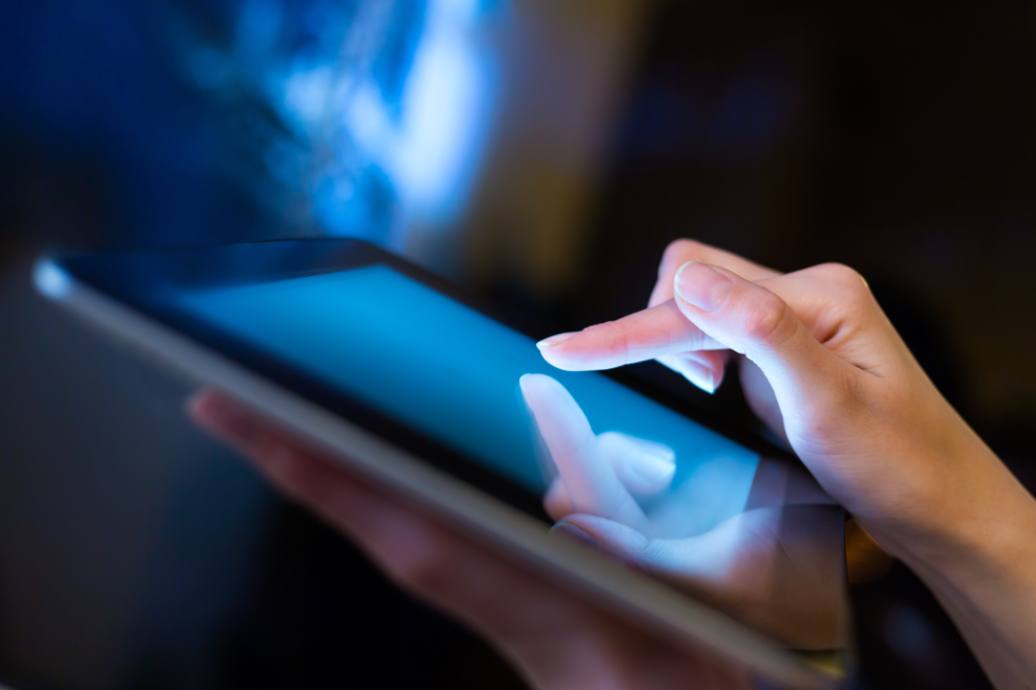
How do remote condition monitoring with remote service solutions empower manufacturers to build new revenue streams?
Using the industrial IoT opens machines builders up to a new world ripe with opportunities to implement new business models and revenue streams. Currently, once a machine is in the field, support from OEMs can often be viewed as costly and inconvenient. This results in customers using in-house service technicians or 3rd parties to maintain machines. With the customer’s preference of a “one and done” machine sale, there is little loyalty to the OEM. However, OEMs have an opportunity to change the narrative through digitalization.
Challenges of machine maintenance
The way most manufacturers maintain their machines results in unnecessary and costly downtime. Scheduled maintenance takes machines offline whether they need servicing or not, and it also does not prevent unexpected machine failures. To combat these maintenance obstacles, manufacturers need remote condition monitoring and remote service.
Remote condition monitoring + remote service
Through the industrial IoT, OEMs can offer new services, like maintenance as a service, to their customers and provide guaranteed uptime. By connecting to and monitoring the status and health of machines in the field, maintenance is performed only when the data indicates it’s needed. This results in more uptime, healthier machines, higher productivity and more satisfied customers.
Taking it a step further, offering remote services allows the OEM to remotely repair or update machine parameters. By diagnosing and repairing machines remotely, you can reduce travel costs and prevent downtime.
A customer success story
Join us for our Remote Condition Monitoring and Remote Service webinar, where we look at a customer who is successfully implementing remote condition monitoring with remote services for their customers. The company maintains twenty production sites globally, with a plan to produce approximately 200 machines worldwide within three years. With machines sold across the globe, they were challenged with high service costs and slow mean-time-to-repair – resulting in unhappy customers.
But with this new solution, they remotely monitor each machine’s health and then react before serious problems occur. Offering remote service allows them to diagnose issues remotely and have their experts guide the local technician through the maintenance, thus reducing time-to-repair and service costs.
Get started
With industrial IoT solutions, you can monitor the health of your machines in the field and respond quickly and proactively once anomalies are detected. Ready to get started or learn more about how it works? Watch our Remote Condition Monitoring and Remote Service webinar!