Procurement, early design and digitalization in the post COVID-19 marine industry
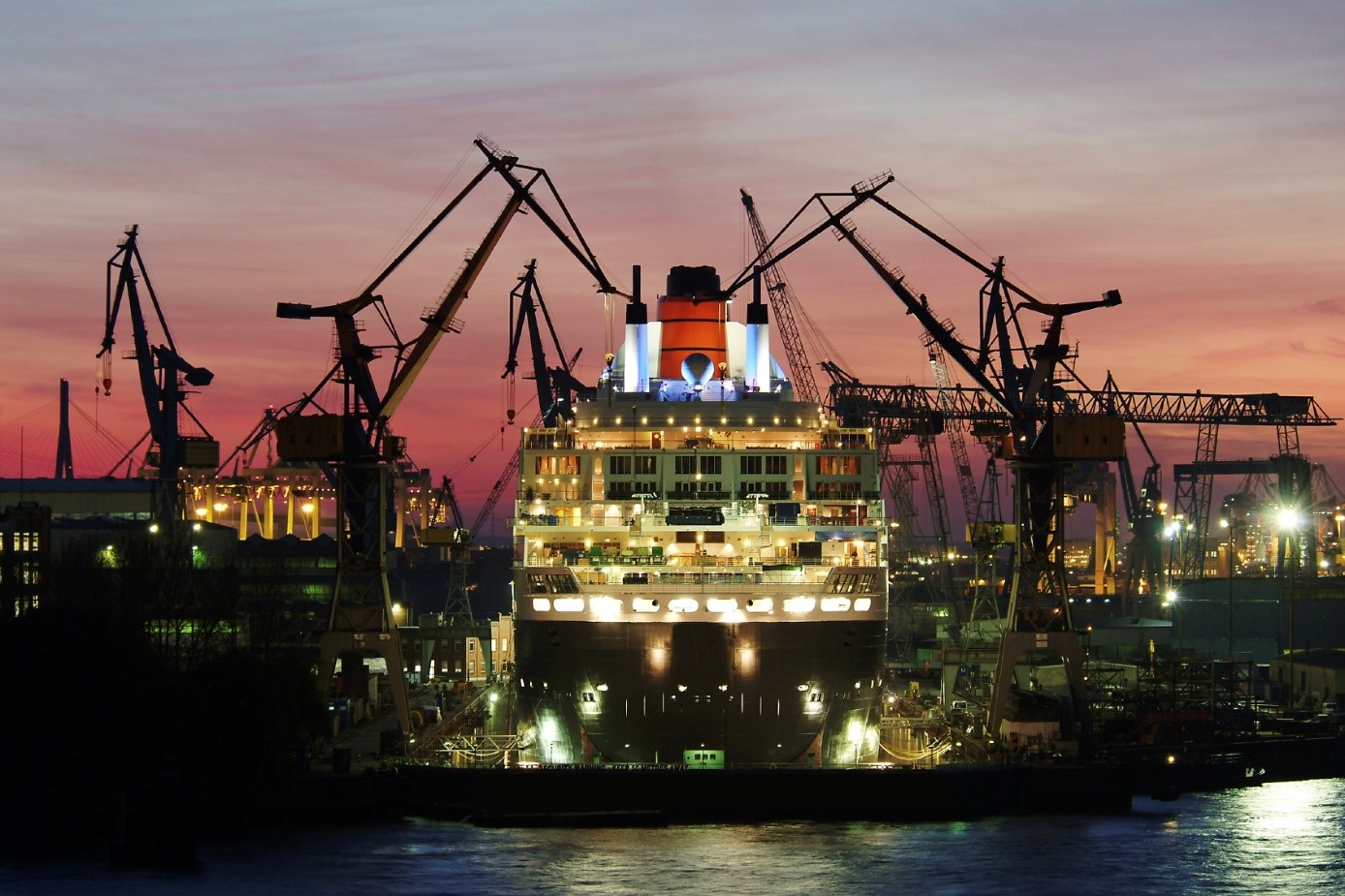
New challenges don’t always need new solutions. It is fascinating to see how different businesses have been dealing with the limitations placed by the COVID-19 outbreak. For example, in their recent ad “You Can’t Stop Us”, Nike decided to re-use existing old footage in a creative way, since shooting new footage is extremely difficult in current times. Although the marine industry couldn’t be more detached from the advertising industry, the principle of using what exists in smarter ways to create more value remains very much applicable. It is perhaps a good moment to reflect on how digitalization strategies and existing technology can be leveraged to not only adapt but to thrive in the new normal.
As Dr. Deponti very nicely articulates in his blog, the digital twin is more about people than it is about technology. Shaping processes that enable people to leverage data and technology to create value forms the basis of innovation. Data strategies that reduce repetition, re-use digital data and leverage fast solving simulation models across teams and project phases, are imperative to developing a sustainable strategic competence for any ship or submarine building entity.
In this part of the four part blog series, we will assess some problems and trends in the process of procuring heavy duty equipment and how the combination of technologies offered by Siemens solutions can help make them more efficient.
Heavy duty assets like pumps, compressors, pipes, fittings, valves and storage vessels etc. need to be ordered much in advance since RFQ (Request for Quotation) to delivery times for such assets are often quite long. Even a small delay at this stage may result in severe disruptions to project timelines. This leads to increased pressure to place such orders as early as possible often at a stage when the final system specifications are not even known [Designing a modern submarine – Thyssenkrupp Marine Systems].
How does it work today and what’s the problem?
The bill of materials (BoM) for such assets is often managed in a PLM system like Siemens Teamcenter. Although some purchases are routine, in other cases it is important to consult engineering before a decision can be made. As engineering hours are expensive, procurement decisions are still made based on thumb rules which were developed to keep CAPEX low with a high emphasis on safety. Those decisions are often costing more over the life cycle as we will demonstrate in next part of the series [Light Bulb Economics and Basic Engineering of Auxiliary Systems].
A decade or two ago, it might have taken experts multiple graph papers, pencils and rulers to determine the answer to engineering problems (Figure 1). The accuracy would have been determined by the degree of sharpness of the pencil’s tip. Today, these problems (and much more complex ones) can be solved in a matter of minutes if not seconds.
Figure 1: Typical methods for determining the specifications of assets to be procured
In some marginally advanced environments, spreadsheets have been used for their simplicity and ubiquity. However, these entail significant limitations when it comes to technical depth, versioning, integration with PLM and robust parameter and model lifecycle management. Worse even, the person who authored them decides to go work somewhere else and all of that precious knowledge built over the years is lost.
Altogether, the argument for convenience and ubiquity in favour of spreadsheets is lost in view of major technical limitations, difficult maintenance, resource inefficiencies and significant inconsistencies in design calculations.
In contrast to this, Simcenter Flomaster together with Siemens Teamcenter for simulation provides a robust solution for enterprise-wide deployment with efficient data and model management that enables cross collaboration between teams (Figure 2).
Figure 2: Leveraging model-based insights across enterprise and project phases
Simcenter Flomaster streamlines fluid-flow-related plant engineering aspects with built-in validated loss data libraries, multiple standards for pipe schedules, CAD import functionalities, etc. allowing the same models to be re-used for detailed engineering and dynamic loading of piping when fluid transients occur.
Siemens Teamcenter provides basis that allows tasks to be created, assigned and monitored with analyses results being published back into the same environment so that teams performing a range of different functions are able to retrieve information relevant to them and make the right decisions quickly and with confidence. This allows procurement teams to validate various equipment specifics from any vendor quickly and limit only special cases to be assessed further by engineering.
Integrating models as part of digitalization strategy
Although there is a lot of stress on digitalization with ERP and PLM, almost all current approaches miss out on two key aspects:
- Strong disconnect between CAD and CAE: Consolidating digital data scattered in different formats (solid CAD, PFDs, P&IDs, Isometrics etc.) across multiple tools and teams throughout the enterprise to create value (Figure 3).
- Leveraging the predictive power of fast solving deterministic models for decision support. For example to answer questions like “Why is one design alternative better than another?”
Figure 3: Industry-wide disconnect between CAD and CAE
An enhanced integrated digitalization strategy addressing these points will not only positively impact profitability but also reduce project risk and shorten timelines.
Digital thread connecting CAD & CAE
Simcenter Flomaster offers unique functionalities that can use digital information to automate model creation and save precious engineer hours. The supported CAD platforms include major tools like Siemens NX, SolidEdge and other CAD solutions. Isogen/piping component file formats created by systems from Siemens NX or other vendors can also be used to automatically create models.
The video shows how an auxiliary system’s CAD layout in Siemens NX is used to automatically create a model. This allows a wide range of operating points to be assessed quickly so that an appropriate pump can be timely ordered.
In the absence of reliable information during the early project phases, the models default to using empirical pressure loss data based on the works by D.S. Miller. However, they maintain the flexibility to incorporate any relevant vendor information like pump curves or valve Kv/Cv curves as vendors get finalized and the design matures. Thus, performance for a range of different parameters and vendor data can be assessed quickly and early in the project to support asset procurement decisions and avoid project delays and technical problems later.
As the industry struggles with uncertainty in global demand, an investment in processes that connect people, data and technology to create value pays-off directly. This further opens doors for more innovation, extended asset life and higher reliability and performance of assets over their life cycle.
The current blog is part 1 of a series of four blogs exploring the idea of digital continuity and integration of data management and fast solving thermo-fluid models for plant piping in ships and submarines.