Design Excellence in Medical Device: Digital Evidence
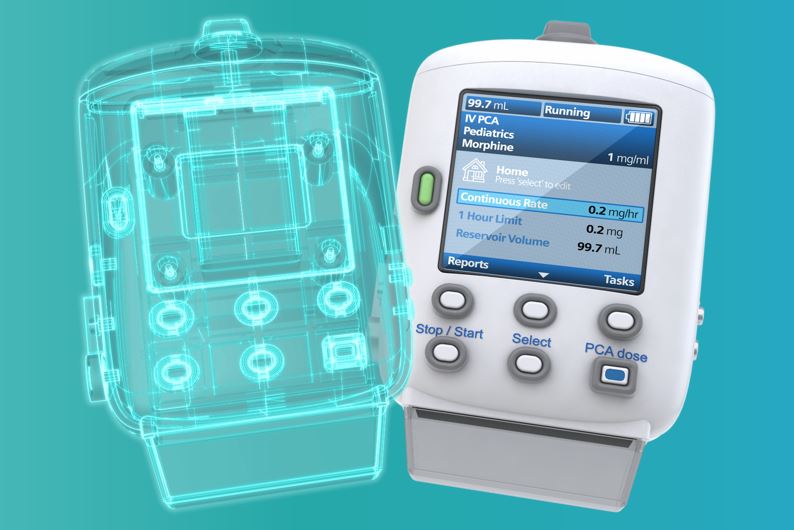
In this post we will explore Digital Evidence to reduce costly physical tests and iterate quickly through Verification and Validation as part of our Design Excellence series for Medical Devices. Follow along to learn how 5 key areas of Design Excellence combine multi-disciplinary design collaboration with advanced design tools and multi-physics simulations to achieve competitively differentiated, premium-value devices.

Digital Evidence
The healthcare industry is well known historically to lag in the adoption of technology in many areas. From health records and HIPPA concerns to medical device design files and audits, many of these activities continue to be done on paper, at least in part, even today. Paradoxically, this slow transition is due in large part to the regulations put in place to protect public health and provide better outcomes. While these regulations provide increased control and oversight, it comes with increased cost and complexity, and a perhaps unintended consequence of slowing new technology deployment which correspondingly delays healthcare improvements.
When looking at medical device design, a significant expense and effort must be made to ensure a new device is both safe and efficacious, while also showing compliance to all applicable regulations. Ultimately the evidence for this resides in the Verification and Validation (V&V) evaluation of the device. If you look at a typical project change cost model for and product development (below), the costs are inverse to the freedom of change as the project progresses, with the highest costs and least amount of design freedom at the end.

Typically, V&V occurs once production equivalent samples are available in statistically significant quantities to generate evidence of ‘goodness’. This means though that the testing is often expensive both from the costs of the samples and the testing itself, as well as the stage of project maturity required to achieve this evidence. What if we could shift V&V, at least in part, to the left in this model? What if we could potentially reduce sample sizes or frame more efficient testing through additional evidence earlier? Both the ability to make meaningful changes through increased design freedom and reduced project costs result. Computer modeling and simulation provide this possibility.
In fact, the FDA is increasingly interested in computer modeling and simulation as digital evidence – to provide better outcomes. They are recognizing and promoting this as a valid approach across a range of modalities such as simulation of the device, the anatomy, the physiology, treatment effects, and even simulation as a device among others. While regulations do not prohibit using simulation tools by any means, barriers to industry use (some of which is self-imposed) have ranged from lack of guidance, computer system validation regulations, and general risk aversion of modeling vs physical testing.
To further the cause, the FDA has published guidance in September 2016 regarding using this digital evidence in submissions ‘Reporting of Computational Modeling Studies in Medical Device Submissions: Guidance for Industry and Food and Drug Administration Staff.’ Note that this guidance targets both industry and the agency to provide a common set of expectations and consistency in the evaluation of such evidence. In addition, FDA representation is involved and currently chairing ‘ASME V&V 40 Computational Modeling of Medical Devices’ to help industry standardize verification and validation of simulation/modeling. It uses a risk-informed credibility assessment framework to aid decisions on how extensive the support should be.
So – you want to make the leap to use more simulation for better design choices & freedom, reduced change costs, and to produce digital evidence – how do you ensure your digital twin is accurate? Do you have an identical twin or a digital Frankenstein?
A significant effort goes into modeling your digital twin and you want to maximize returns. In order to do this, you need to be able to simulate the product, design variation, and the environment accurately under real-world conditions. The more closely you can achieve a true digital twin the greater the value.
Companies can accurately simulate a range of problems ideally suited to medical device development ranging from fluid, structure, particle, and thermal modeling into acoustics, electromagnetics, rheology, and even electrochemistry. These can be modeled in unison to predict real-world performance.
Modern performance engineering requires analysis design excellence. Dabbling in simulation in a narrow area of focus only provides a limited view of performance. In the medical device field, patient performance and risks must be fully vetted – and they live in the real ‘multi-physics’ world. In order to improve health outcomes and maintain a competitive advantage, medical device companies can utilize multi-physics simulation to optimize total lifecycle costs and reduce time to market, all while producing a better product. It’s a win-win through a digital twin.
To Learn more about Design Excellence at Siemens please visit here.