Applying simulation and CFD for better medical device designs with Terumo Corporation
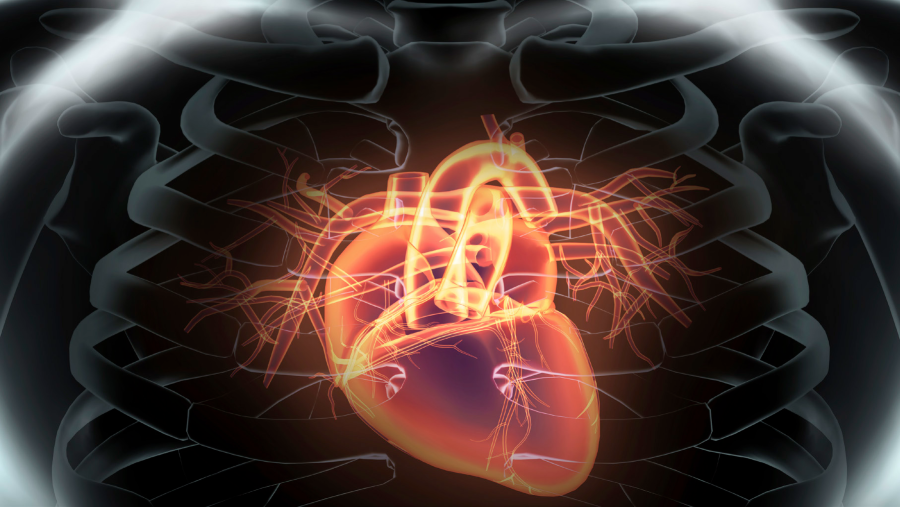
The use of computer-aided engineering (CAE) and computational fluid dynamics (CFD) significantly reduces workload while ensuring reliability and improving medical device designs. Engineering simulation is now being widely recognized and adopted by regulatory authorities, manufacturers and suppliers around the world. One such example is a workshop on blood damage studies via the modeling of a blood pump. This workshop was organized by the U.S. Food & Drug Administration (FDA) to set best practices and promote the use of simulation in device design.
Let’s see how Terumo Corporation used simulation to optimize their designs and develop a better ventricular assist device (VAD).
Numerical simulation at Terumo
A VAD is a mechanical pump used to increase blood flow to offset a malfunctioning ventricle in the heart and take over the function of a failing heart. During the VAD development process, computational modeling is an efficient tool for finding the best design for the blood pump even before building a prototype. Blood pumps in VADs need to deliver the required blood flow while minimizing damage like hemolysis and thrombosis. Using CFD facilitates analyzing and optimizing blood flow and the pump.

Takehisa Mori – R&D principal research manager at Terumo – is no stranger to CFD. Mori was the first to apply CFD at Terumo about 15 years ago. By using CFD analysis methods, he evaluates the feasibility and challenges of new devices at the conception stage.
“When I started with CFD, I realized how much I was able to understand designs better. One cautionary point is that some people think too lightly of simulation, assuming that anything can be simulated or imagined. In reality, it’s important to consider what the problem means and what the physical implications are…By utilizing CFD, we can build a base for prototype manufacturing to some extent.”
Takehisa Mori, Prinicpal R&D Research Manager, Terumo Corporation
In the field of cardiovascular surgical devices at Terumo, CFD is used to develop blood pumps. The purpose of introducing a CFD-based design exploration tool is to increase the efficiency of blood pump development and bring a better design to market faster.
Overcoming difficulties in pump design with CFD
One problem when designing a pump is that if efficiency takes too high a priority in development hemolysis can occur. Previously the only way to access the occurrence of thrombosis was with experimentation. However, a new technique using CFD has been established at Terumo.
The assessment method indicated that thrombi do not occur as easily if the shear rate in the retention area is lower than a certain threshold. If a problem occurs with products designed before CFD application, it is possible to conduct root-cause analysis and change the design quickly by repeating the analysis using CFD. By applying Simcenter STAR-CCM+ to pump design, design and troubleshooting have become extremely efficient.
Results of using Simcenter STAR-CCM+ and CFD
Conventionally, the design method for blood pumps has involved using CFD to analyze dozens of initial-stage models in order to estimate the performance of each under the same conditions, and this method produced several candidate models. Then, pump performance evaluation and blood-related experiments were conducted, with problems in design being rectified. This process was repeated until a final prototype was determined. Consequently, the development period for one product took years.

With Simcenter STAR-CCM+ and the Intelligent Design Exploration solution add-on, Terumo was able to significantly reduce the development time for blood pumps while achieving a better design faster. The geometry of the pump was created using the 3D-CAD modeler in Simcenter STAR-CCM+. As 3D-CAD can parameterize the design variables, optimization calculations can be implemented in a more seamless manner, saving time and additional license costs.
The total number of analysis cases from the optimization process was 102, and the time required for the calculations was about six days. Based on the constraints and the base case, Simcenter STAR-CCM+ automatically refined the design variables (impeller diameter and casing) and iterated the simulations for all cases. Of these, 38 cases met the constraint conditions.
Furthermore, the optimization results showed that a design with good pump efficiency that satisfies the constraint conditions tends to be a design with small values for the height of the opening of the casing side and a small starting diameter. Using design exploration, it was found the shorter the interval between the impeller and casing is, the more efficient the pump becomes. The best design was identified within a week with the simulation-led optimization process.
Learn more about how Terumo used Simcenter STAR-CCM+ for better and faster medical device designs.