Master medical device compliance with closed-loop manufacturing
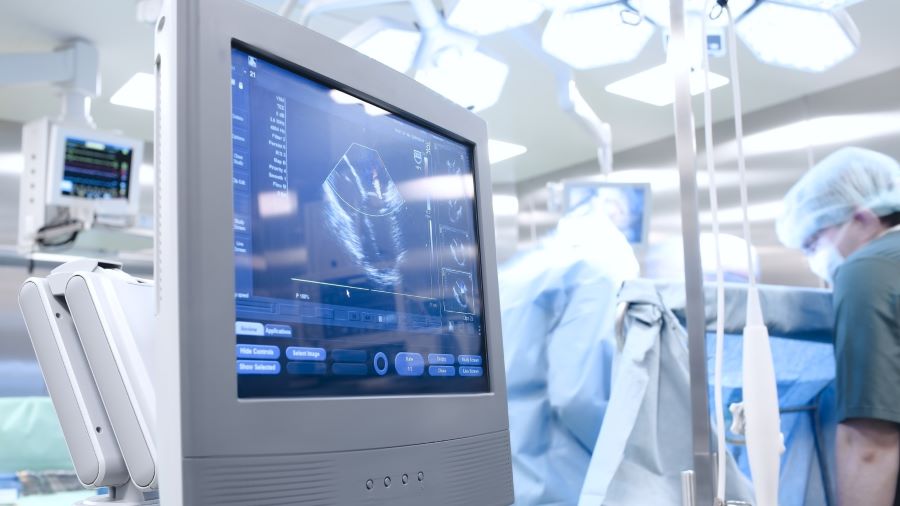
Struggling with quality and medical device compliance? Learn how to overcome the ever-changing regulatory landscape and how closed-loop manufacturing drives innovation and cost reduction.
Medical device manufacturers have to face one of the biggest challenges – an explosion of complexity. The companies that are leaders and innovators in the industry do not try to limit the complexity. Instead, they embrace it. While every company wants to be a leader, many manufacturers tend to be reactive versus proactive. This reactivity happens for various reasons – increased demands, more complex products and heavy overhead of regulatory compliance.
What is the cost of quality?
As many have seen with the COVID-19 pandemic, healthcare spending is rising. Based on a recent study from Medicare and Medicaid Services, the amount of healthcare spending in the United States is expected to grow to $5.34 trillion by 2025. The workforce is aging, and people are growing older. A United Nations study identified that there are over 700 million people of age 65 or older. This number is expected to reach one and half billion by 2050.
As this aging population grows, medical device manufacturers must grow too. Invest in technology and solutions that can handle the demands of the market. It is the responsibility of manufacturers to make sure their devices are of the utmost quality. Product quality affects the patients that receive them and the businesses that make them.
A recent report from McKinsey shows that non-routine quality events cost the medical device industry between $2.5 billion and $5 billion per year. This includes $1.5 billion to $3 billion per year on non-routine costs, plus $1 billion to $2 billion in lost sales of new and existing products. The cost of quality is too great to be overlooked or underestimated.
One way to measure the cost of quality is to understand the cost of complying with quality regulations. The average compliance cost for the medical device industry is between 6.8 percent and 9.4 percent of annual industry sales. Approximately a third of this is tied to quality activities. After a large amount of time spent on quality, half of FDA inspections are still leading to official action, including warning letters and product recalls.
An ounce of prevention is worth a pound of cure.
Benjamin Franklin, 1736
Having the right systems in place early to manage product quality and detect errors can be lifesaving to patients down the line.
What is closed-loop manufacturing?
Closed-loop manufacturing (CLM) seamlessly integrates the three major domains: product lifecycle management, enterprise resource planning and manufacturing operations management. CLM enables synchronization and optimization along the complete value chain from product design to manufacturing execution.
CLM can coordinate product design, production engineering, production planning and production execution. This enables direct cross-domain feedback loops from upstream to downstream processes. This can include change management and non-conformance or defect tracking.
CLM continuously improves the cost, time and quality of the manufacturing process to accelerate time-to-market.
How to master medical device compliance
To master medical device compliance means having to embrace complexity. As mentioned above, many manufacturers are reactive. Using paper-based processes, struggling with non-value activities, and suffering from resource constraints give way to more errors. Changing from reactivity to proactivity in medical device manufacturing can improve quality and bring down costs.
So, how can one become more proactive in the manufacturing process?
Here are some ways that leaders in the medical device industry are showing proactivity:
- Take a digital comprehensive approach to manufacturing
- Improve sustainability by optimizing resources and eliminating paper
- Significantly improve focus on quality and patient safety
- Find opportunities to lean processes and reduce costs
- Eliminate non-value activities
- Improve time-to-market
There are also three competitive advantages that manufacturers can use to master compliance.
The first concept is the comprehensive digital twin. With the insights and data from the digital twin, companies can accurately simulate and predict device performance and the product systems in their factories.
The second concept is personalized, adaptable and modern resources. Companies must be able to provide people across their organizations with tools that are easy to use and pull information from multiple places. Making data available is not helpful if it is presented in a complex or confusing way. It must be consumable and digestible.
Finally, the third concept is a flexible open ecosystem. Information technology plays a critical role in harnessing complexity as a competitive advantage.
To learn more about manufacturing execution and medical device compliance, watch the webinar here.
Interested in more blogs on the medical device industry? Read more here.