Additive manufacturing and the industry of tomorrow

As product development and manufacturing times extend, the pace of innovation is accelerating and market competition is escalating. Manufacturers of everything from passenger cars to smartphones, aircraft and more are striving to bring brand new products to market faster than ever. In addition, companies are trying to respond to growing demand for customizable products, requiring flexibility in manufacturing. Automotive, aerospace, consumer products and other companies must find a way to streamline product development, from design through manufacturing and certification, to overcome these challenges.
Additive manufacturing (AM) technology may prove to be the answer. Additive manufacturing technology has the potential to solve the challenges facing companies today by improving the processes required to produce complex products and parts. However, there are still sizable barriers to the practicability of AM, especially at an industrial scale. It will take concerted effort and collaboration from the growing number of additive manufacturing companies to overcome these challenges and realize the potential of AM.
Additive manufacturing – Benefits and challenges
Additive manufacturing (and 3D printing) is the process of printing parts, sub-assemblies or entire products layer-by-layer from detailed computer aided design (CAD) models (figure 1). Compared to traditional manufacturing methods, AM delivers some substantial benefits. AM is faster and more flexible than traditional manufacturing methods, such as injection molding, that require bespoke infrastructure, like a mold of the product, to be designed and produced before production can begin. Not only does it take time to design and create this manufacturing infrastructure, but it also makes traditional production lines difficult and costly to adapt to new products or configurations.

AM can also reduce the cost of producing complex products, both economically and temporally. Complex assemblies can be simplified to a single part, vastly reducing the material and number of operations required for production, and, therefore, lowering cost. In turn, replacing complex assemblies with single, 3D-printed parts allows companies to condense supply chains, reduce assembly times and make repairs easier.
Third, additive manufacturing machinery and processes are highly flexible. AM imposes very few constraints on product geometry and can transition between various products or configurations with relative ease. This flexibility makes ‘lot size of one’ manufacturing possible, meaning a production run of one unique part or product. This is a critical capability in the current age of customizability because it can enable the production of highly individualized products at an industrial scale. With AM, companies can meet the individual needs and demands of the consumer while reaping the cost benefits of producing at a mass scale.
Finally, AM facilitates the adoption of new technologies and innovative product designs. Fewer manufacturing constraints allow engineers to reimagine product designs to integrate new technologies or design philosophies (figure 2). For example, AM can print complex lattice structures that maintain structural rigidity while also improving thermal performance and reducing the weight of the product or part.
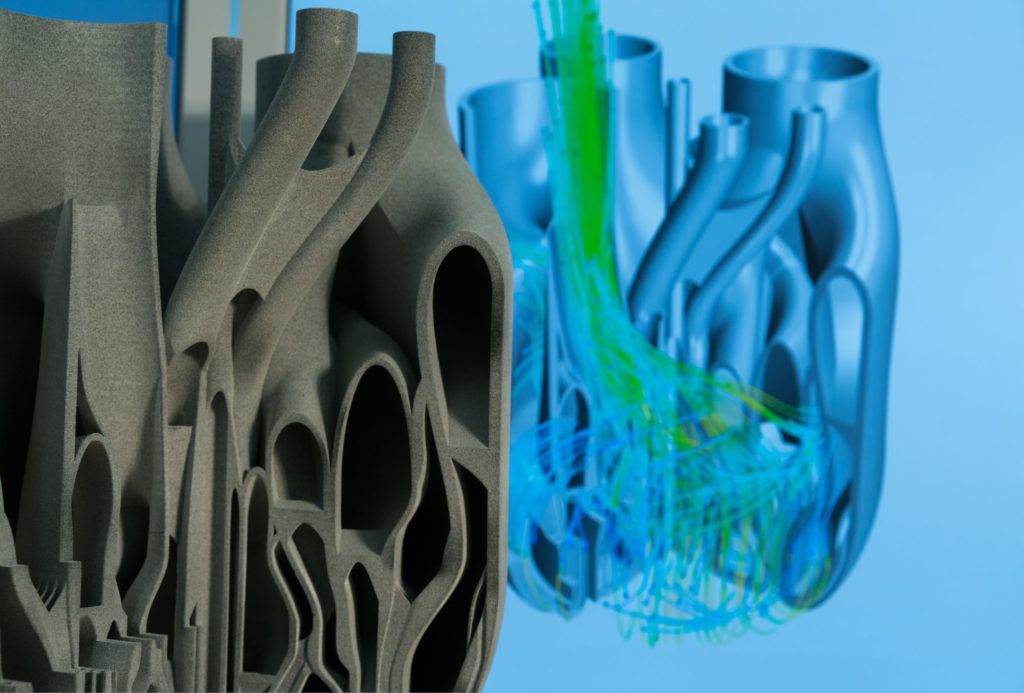
At the same time, AM continues to face some significant challenges that impede progress. First is the development of new printing materials. New printing materials have the potential to improve AM results significantly, but the development and certification of these materials, at least for now, is extremely costly and time consuming. The industry also lacks a robust standard for the certification of new printing materials, leaving companies to evaluate and benchmark developmental materials on their own while also accepting greater risk.
It is also more difficult to achieve repeatable product quality with AM. Compared to parts produced with conventional manufacturing technologies, AM-produced parts require up to three-times more iterations to achieve a design that will print repeatedly at high quality. Following on from this, the final major challenge for AM is delivering high-quality parts at an industrial scale. AM processes involve numerous variables and require frequent monitoring and management. Companies have to select the right materials, define and optimize printing sequences and part designs, and ensure print quality remains consistent. Achieving each of these tasks across industrial scale production is extremely challenging.
Industrializing additive manufacturing technologies
These challenges are daunting, but every company can take steps to prepare for or improve the integration of additive manufacturing into their production processes. Most importantly, companies will need to establish a robust additive manufacturing software platform that connects product design, simulation and manufacturing.
For AM, a tightly integrated and closed-loop design-simulate-manufacture flow, leveraging digital twin technologies, is critical to achieving quality products while minimizing design iterations. Before printing, designs have to undergo rigorous simulations of the printing process to mitigate risks, optimize the printing and, thus, improve yield (figure 3). These simulations must cover the full breadth of variables that can affect the outcome of AM, including the mixture of virgin and recycled print material, ambient humidity, machine parameters and more. With AM, simulation of designs and the printing process are a necessary step on the path to manufacturing actual product.

In addition, most companies will fit AM machinery into existing facilities, integrating it with conventional manufacturing processes. It is important that the transition to a mixture of AM and traditional manufacturing processes occurs as seamlessly as possible to minimize cost and downtime. Manufacturing engineering software can help companies virtually plan and integrate AM processes, and simulate the operation of the new mixed-production facility. This allows engineers to uncover potential problems and optimize the implementation of AM processes before commissioning any machinery.
The Xcelerator portfolio provides an additive manufacturing platform
Xcelerator, a comprehensive and integrated portfolio of software and services from Siemens Digital Industries Software, can provide the software foundation companies need to bring AM into their production portfolios. Through Xcelerator, Siemens can support the most comprehensive digital twin of products and additive manufacturing processes. This digital twin spans from initial design to simulation, production and testing with the goal of improving yields from AM (figure 4).
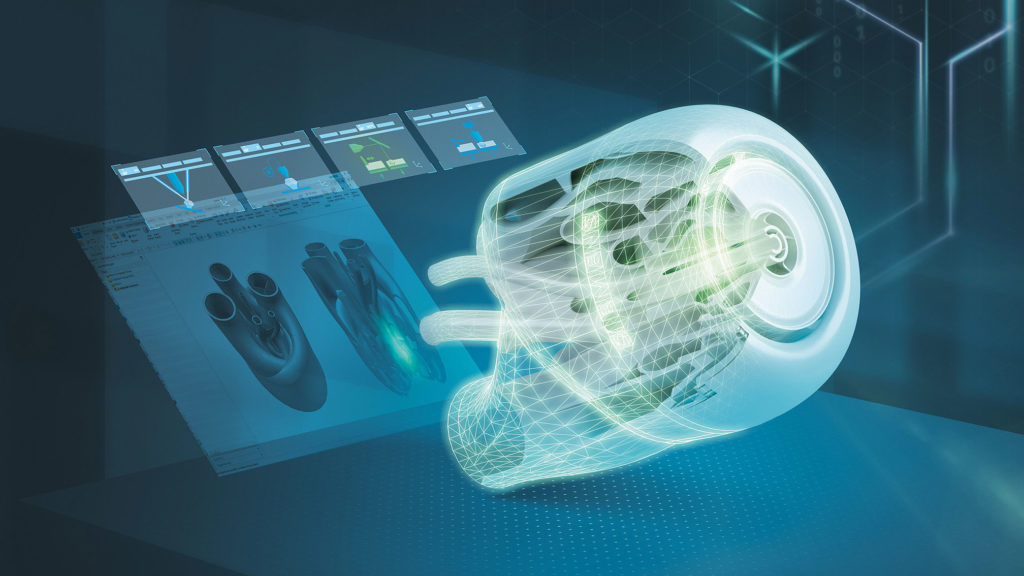
Comprehensive digital twin technologies also facilitate close collaboration between the product design team and manufacturing. Designers and manufacturing engineers can simulate the entire printing process to validate the product geometry and print sequence virtually. Then, the print can be monitored, with real-time data being fed back into the digital twin to adjust the print sequence and avoid errors like deformations and re-coater collisions.
As each company has unique needs, software solutions must adapt to a variety of needs and applications. Some companies focus solely on the creation of prototypes with AM, while others offer prototyping and full production services to their customers. All of these companies use a unique mix of materials and printer hardware. Xcelerator can enable companies of all sizes with outputs from a few prototypes up to full production runs. It also supports the largest number of printer hardware companies in the industry.
Finally, no one company can solve all of the challenges alone. Recognizing this fact, Siemens and its peers in the AM industry have fostered a strong ecosystem of collaboration and co-development. We work with a large network of additive manufacturing companies, including hardware and software partners, that encompasses some of the largest vendors in the AM space like HP and Materialise. Siemens Digital Industries Software is also a founding member of the newly launched Additive Manufacturing Network. This network connects product designers and companies without AM facilities of their own to manufacturers that have the machinery and experience to print products successfully. The network also allows companies and designers to solicit expert feedback on product designs to improve them for the printing process. This will help even the least experienced companies achieve success with AM.
Where additive manufacturing meets tomorrow
AM has the potential to play a vital role in the development and manufacturing of the ever more sophisticated products of tomorrow. Complexity is continuing to grow while, at the same time, time-to-market is shrinking. These challenges are escalated by the demand for customizable products, which requires greater flexibility in production systems. AM has the capabilities to solve these challenges because it can simplify the process of developing and manufacturing advanced products. Complicated assemblies can be reduced to single parts that are easier to produce and require less material. As a result, AM can save cost and a help companies get to market faster.
AM, however, is also very challenging to implement and scale, especially without strong partnerships. Optimizing designs for the AM process often entails arduous trial-and-error while sustaining product quality from print to print remains troublesome, especially as scale increases. Despite these hurdles, AM’s potential to drive change in product design, manufacturing and service makes it a technology you cannot, or should not ignore.
Fortunately, companies in the AM industry are coming together to solve these problems in the pursuit of bringing the technology to the industrial scale. Siemens Digital Industries Software is a central player in this ecosystem. With broad partnerships and the technology and experience to support AM implementations at all stages, Siemens can help companies achieve their AM goals more quickly and more securely.
This is where manufacturing meets tomorrow.