5 Myths of Computational Fluid Dynamics (CFD)
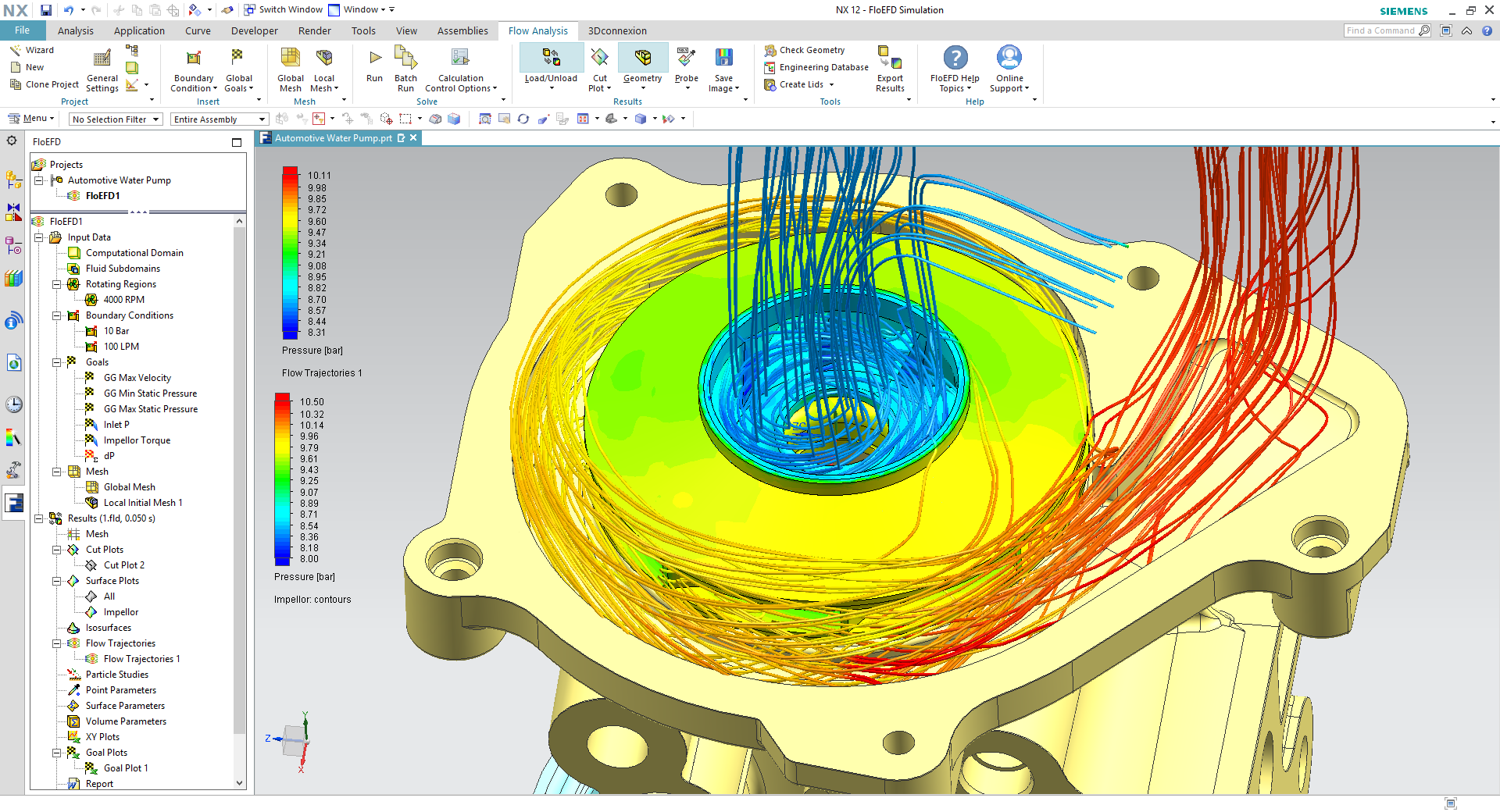
What is Computational Fluid Dynamics anyway? For an introduction on FLOEFD for NX please see our information here.
Lets get started:
Myth #1: “Most Products Don’t Need a CFD Analysis”
We judge this myth to have been largely consigned to history. It is apparent that, today, CFD is used to improve products as diverse as swimming pools, toilets, hand dryers, lawn sprinklers, gas meters, production printing systems, disk drives, and oil filters to name just a few applications. Although not yet complete, the democratization of CFD for use in product design has extended into undergraduate courses and even to high school programs.
Myth #2: “Experts are needed to get accurate CFD simulation results”
This myth still partly applies to traditional CFD, helping preserve Myth 1 within a broad cross-section of the CFD community, because near full-time use is required to gain and maintain a high level of proficiency. It is interesting that any two experts will always produce a different simulation result for any realistically complex industrial problem. They will generally disagree on whose result is the best one. This debunks the last line of defense in the argument for the involvement of expert analysts—that they are needed to check the results produced by non-experts.
Building in ease-of-use lowers the level of simulation-specific expertise needed, thereby allowing engineers to focus on the engineering problem. The numerical and physical modeling expertise of the software developers is accessed by the design engineer via the automation provided within the tool. Inputs are limited to what needs to be known about the problem being described: boundary conditions, materials, etc. applied directly to the native 3D geometry within the CAD system. Thus, non-simulation experts can get reliable, repeatable, high-quality simulation results.
As noted in the footnote earlier, an appropriate engineering background and domain expertise are necessary to understand the application being addressed to leverage the simulation results and improve the product design. However, automated optimization is already reducing the level of domain expertise needed to make design improvements. CAD-embedded CFD provides both parametric study and result comparison capabilities making design improvements easy to investigate.
We are in no way belittling the value of analysis experts. Such people are the very reason that CFD has grown to become what it is today, pioneering new applications that have driven the development of new physical and numerical models, etc. In late design, when the geometry is stable, traditional CFD can be applied, leveraging the availability of analysis-ready CAD which is refined using a CAD-embedded CFD solution, to provide further design verification if desired.
Alternatively, analysis experts can themselves use CAD-embedded CFD during design. CAD embedded CFD and traditional CFD can, and arguably should, complement one another. CAD-embedded CFD also integrates well with other CAE tools used in product design, allowing temperature data to be exported as a thermal load for use in Creo Simulation and NASTRAN-based FEA solvers, among others, helping to accelerate other aspects of the design.
Myth #3: “Production CAD is too complex to use for analysis”
When working with exported CAD geometry, fitness for analysis depends greatly on how the original CAD model was created, the quality of the translator used to convert it into some neutral file format, the neutral format chosen, and how well the target analysis tool’s CAD import handles the import of that particular format. Unfortunately, once a CAD assembly is exported, much if not all of the parametric and history information (i.e., the software history of how the assembly, parts, and their features was built) is lost; and with it, the ability easily to detect and fix design mistakes is massively impaired. At this point, simplification and reconstruction of parts of the assembly can be the only option, both of which can give rise to errors.
Working with native CAD inside the MCAD system is a different story. Mistakes can be detected and fixed once only, and with relative ease directly within the main design workflow so the analysis geometry and design geometry are always in sync.
Concurrent CAD-embedded CFD tools based on Cartesian meshing are also highly tolerant to CAD errors, because a surface mesh is not required as part of the analysis process. Furthermore, minor features present in the CAD model that have no significance for the CFD analysis can be neglected by not using a sufficiently fine local mesh to resolve them. Conversely, small features such as joins and small gaps can be resolved to investigate their effect on the flow performance of the system. In CFD, small features often have a marked effect on flow performance, for example, by causing boundary layers to “trip” and the flow to separate. Geometry simplification is not needed; however, it is not prevented. It is relatively easy to prepare the geometry for efficient yet accurate analysis by using either the feature tree to control parts and features, and/or the de-featuring capabilities of the CAD system.
Myth #4: “CFD is too expensive to be used by mechanical designers”
In our original whitepaper, we observed that traditional CFD codes cost in the region of $25,000 to lease for one year. The latest generation of CFD code intended for use during the mainstream design process cost around $25,000 for a perpetual license. The only ongoing cost is a maintenance fee on the order of 18% ($4,500) per year. The cost of ownership is further reduced because it can be used by a mechanical design engineer with minimal training. Novel techniques, such as immersed boundary treatments for fluid–solid surface friction and heat transfer, massively reduce the mesh count required to achieve accurate results, allowing useful work to be undertaken on multicore personal computers and laptops, reducing the cost still further
Myth #5: “You can’t directly use your CAD model to do CFD analysis”
In the past, it was necessary to copy or translate the CAD model to a different program and then modify it substantially to create the CFD model. Many people found it more reliable and less effort to start from scratch by recreating the geometry within the CFD program, despite this involving a considerable expenditure of time and introducing an additional and significant source of error.
Today, native 3D CAD data can be used directly for flow simulations without the need for translations or copies, or creating phantom “objects” in the feature tree to represent the flow spaces. The myth that CAD geometry can’t be used directly for analysis persists today, but in a slightly different guise, giving us our fourth new myth: Myth #9 – Production CAD is too complex to use for analysis.
Like what you see? Want to learn more? For the complete list (10) of CFD myths please download our whitepaper here.