Automotive supplier Euroform uses NX to increase market share by 11 percent
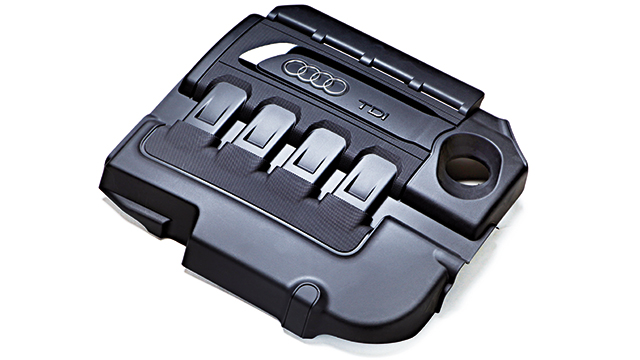
The business challenge: Euroform needed to meet technical and quality requirements while reducing time for design and production.
The result? Increased market share by 11 percent. Reduced design time by 50 percent. Cut cycle time by 50 percent
Euroform
Who is Euroform? Euroform is one of Europe’s leading designers and manufacturers of tools for the production of plastic injection molded parts. The company serves customers in the food and packaging industry, but its primary area of focus is the automotive industry.
“The design phase is of decisive importance in
István Harcsa
the production of plastic molding tools, and
that’s the reason that Euroform chose NX.”
Tools Plant Manager
Euroform
With a strong presence in a number of sectors, including home applicances, Euroform thrives in the automotive industry, designing and manufacturing tools for the production of acoustic housings, air intake systems, pedals, glass enclosures, housing elements, chassis shock absorbers and bellows. Its products are molded parts that weigh anywhere from 5 grams to 5 kilograms.
Boosting Market Share
Euroform used computer-aided design (CAD) software even before the introduction of NX. At first, Euroform used I-deas™ software, which is now integrated into NX. However, with some of the company’s suppliers using NX to design products, the company took the opportunity to get familiar with the advantages of the comprehensive product development system. In 2011, Euroform transitioned entirely to NX, which it continues to use to create 3D designs and molding simulations, and to perform drafting.
“By using NX, the duration of our designing processes has decreased to roughly half the time it used to take us,” says Harcsa. “Today, we can design a tool – depending on its complexity – in about two to three days, so we can serve many more customers than in the past. We have also increased our market share by 11 percent.”
Euroform engages NX in the bidding phase and continues its use throughout the product lifecycle. For example, with NX, project leaders assess the models and drafts that are used to calculate the tool parameters and the required standard elements in order to get bids to customers faster.
After the bid phase, Euroform starts by designing the tool housing, shaping surfaces and cooling systems based on the 3D models that it received from the customer.
Achieving cost-efficient development
“We use NX to design and simulate the tool. Moreover, early in the process, we achieve precision and functionality that results in a longer lifespan for our molding tools,” says Harcsa. “NX Mold Wizard provides the right stuff for the cost-efficient development of molded plastic parts.”
When creating molding tools, Euroform has to consider not only how the tool will be used, but also how the equipment that is manufactured using the molding tools will be used.
What do you think of Euroform’s usage of NX to achieve lesser time to market, cost, and increased market share? Let us know by leaving a comment below.