Why Is Facet Modeling Necessary for Generative Design?
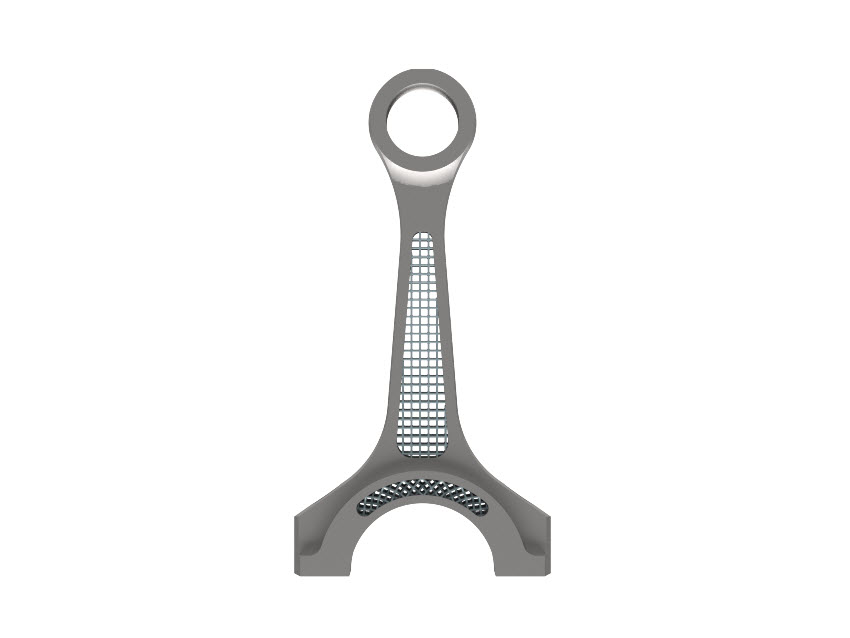
Generative design is a topic you’ve likely heard mentioned before today. Everyone in the PLM industry is talking about it, but few actually have the capabilities in place today for you to take full advantage of it. For those that do, you still have to undergo a long process before your optimized design can be changed or incorporated in the rest of your model. That is, of course, unless you have NX. Download the eBook from Lifecycle Insights analyst Chad Jackson to learn more about why facet modeling is a must to unleash the true power of generative design.
Generative Design: The Way Forward
It’s no secret that products today are far more complex than even those of just five years ago. The increased complexity and technological strides we’ve made impact every aspect of a product—from design and development, to how it’s manufactured, to even how it purchased and used in the market.
You won’t be surprised then to hear that engineers face more pressure than ever. There are strict legal and safety requirements to meet; the product lifecycle grows ever shorter as more companies race to be the first to market with a new design. All of this compounds a problem that has existed in the product development industry for some time: bandwidth. How do you keep up while still delivering a high quality, safe product? Generative design offers hope.
A relatively new approach to product design, generative mimics nature’s evolutionary approach to design. The technology autonomously produces a number of design alternatives using algorithms such as topology optimization and which are based on a set of constraints that you, the engineer, defines up front. Thus, you can consider many more alternatives from which to choose the best design, rather than the first feasible design.
Generative design results in complex, organic shapes that more closely resemble bone structures than manmade components. While these generative designed parts are more lightweight and use less materials than their traditionally designed counterparts, they retain the original structural integrity.
To recap, generative design is a new method of designing parts that leverages algorithms such as topology optimization to explore more design alternatives. The benefit to you, the designer, is twofold: First, you get increased bandwidth to focus on what really matters in your work. Second, your designs are lightweight, cost-efficient (through a reduction of materials used), and often stronger than traditional designs.
Incorporating Generative Design in CAD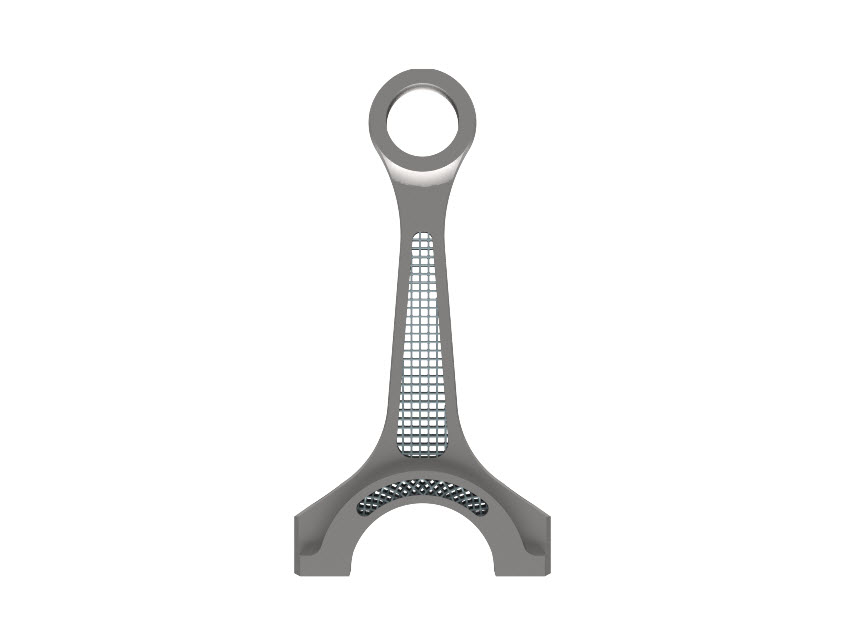
Of course, the extra bandwidth you gain from utilizing generative design doesn’t do you any good if you still have to translate data in order to incorporate the results in your CAD models. The problem is that the geometry you get from topology optimization is faceted or mesh data – meaning the design is made up of many tiny little triangles, compared to traditional CAD data which is either surfaces or solids. (You can read more about the difference between facet modeling and solid modeling in a previous post.) Almost every CAD software out there today is unable to work with facet geometry, requiring you to use a standalone application for facet modeling and work through data translation issues that can take weeks.
With NX there is no conversion process, no switching between applications. You can simply use Convergent Modeling to work with both facet and traditional geometry in one environment. Changes that would normally take you weeks with other CAD systems can now be completed in as little time as an hour.