PM-Bearings achieves excellent part quality with integrated NX solution
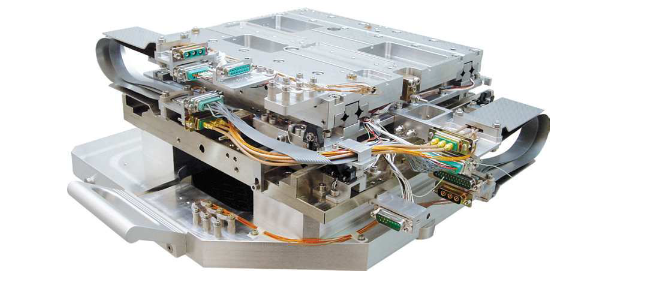
PM-Bearings specializes in the design and manufacture of high-precision linear bearings, motion systems and positioning stages, and supplies the high-end semiconductor, medical device and machine tool industries. Its global customer base extends from Silicon Valley to Shenzhen. The diversity of customer needs presents a number of challenges for the precision bearing manufacturer. These include requests for customization (up to 80 percent of the system design in most cases), short time to market, and extreme precision (for example, smooth motion of two microns per meter). Additionally there are requirements for reduced bearing sizes and exotic materials, including ceramics used in non-magnetic or ultra-high vacuum environments.
To maintain a competitive edge, PM-Bearings knew that complete control of the product realization, from design to delivery, was essential. This is why the company chose a comprehensive set of solutions from product lifecycle management (PLM) specialist Siemens PLM Software. These include NX software for computer-aided design (CAD), Simcenter software for performance prediction, NX CAM for computer-aided manufacturing and Teamcenter software for PLM to make certain that all stakeholders use the same data and workflows to make the right decisions. PM-Bearings has used these solutions for more than a decade, supported by the Siemens PLM Software reseller, cards PLM Solutions.
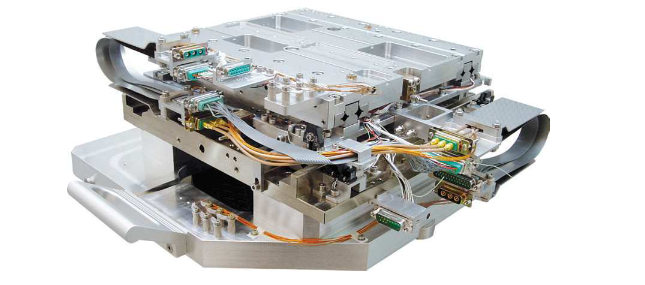
For purposes of the NX Manufacturing blog, we will focus primarily on their use of the CAM solution.
Read the complete PM-Bearings success story.
With extreme requirements for dimensional precision and for minimizing vibration magnitude down to nanometers, PM-Bearings faces unique manufacturing challenges. The accuracy, which is highly dependent on the machining process, affects products’ performance and aesthetics. Efficiently machining precise moving parts from 3D designs requires exact manufacturing instructions for the people and machines on the shop floor. NX CAM software, with its integrated CAD, NC programming and machining simulation capabilities, enables PM-Bearings to define a complete manufacturing plan long before the first production run.
Kenny Prins, computer-aided manufacturing (CAM) engineer responsible for planning and control of production at PM-Bearings, knows from experience that in order to set up the production run completely right the first time, one must plan it digitally. “In the beginning, all the programming was done at the machine,” Prins says. “For each change we had to check and modify the whole program, which was very time-consuming and prone to errors. The resulting downtime of shop floor personnel and machine tools cost us a lot of time and money. Now, with NX CAM we can reduce programing time by up to 80 percent using a digital twin of the workpiece, tooling, and machine, which helps us stay competitive.”
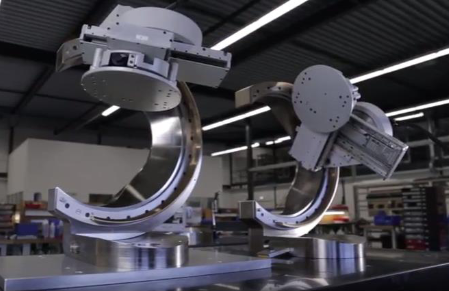
Like many manufacturing companies, PM-Bearings needs to mill, turn, and finish higher-quality products faster, while extending the tool life. “When I receive a model for production from the design team, I first make sure that our tools and machines can handle the job,” explains Prins. “A quick verification of the operations in NX CAM software shows whether the physical machine and tooling might have issues handling the designed part. This is a very powerful functionality that helps us easily eliminate any possible manufacturing problem early in the planning process. When we identify a manufacturability issue, we work with the design team to modify the design. Our teams rely on Teamcenter software for collaboration and data sharing. Using this closed-loop process, the design change automatically propagates through the analysis and planning steps, all the way to manufacturing on the shop floor.”
“Another functionality that I use every day are the flexible machining strategies in NX CAM,” Prins continues. “Not all machining cuts are equal. The precision of the final part is directly linked to the stress induced by cutting operations. The machining strategies are different when milling a large metal block or small parts with five-millimeter thickness. The software automatically proposes a tool path to remove material, but it also gives us flexibility to use our know-how to adjust the machining strategy for best results. By capturing and re-using our experience, we apply efficient machining processes to achieve excellent part quality while extending tool life.”