The Evolution of Tool Path Design (Part 3)
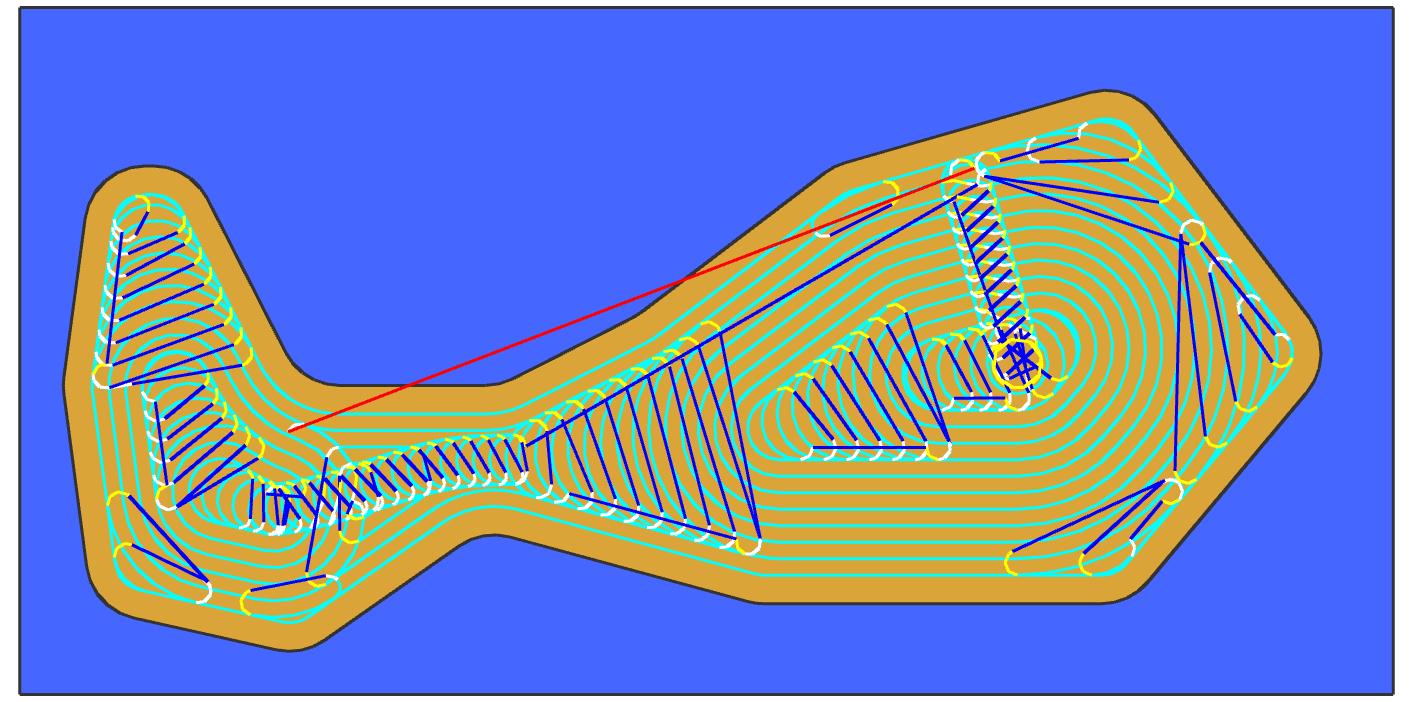
In this post, I will explain the latest tool path innovations for removing large quantities of material.I mentioned in Part 2 that Offset tool paths have problems when the offsets meet at sharp angles.To counter that, the Trochoidal tool path was developed.
The purpose of the Trochoidal tool path is to detect areas where full engagement of the cutting tool occur and then modify that portion of the path so that it becomes a series of circles.The circles act to eliminate full engagement of the cutter.
Pictures are worth 1000 words, and videos are priceless.The first video is Offset tool path, and the second is Trochoidal. The area of focus is outlined in red.
You can even set the Trochoidal tool path to “tornado” into tight corners with ever-reducing circles.Trochoidal is a cut pattern setting in NX CAM and CAM Express.
Another tool path technology also uses a looping method. Instead of just looping in the corners, the entire tool path is a series of loops. This enables the stepovers to be almost completely uniform throughout the tool path. The picture below is a tool path created by Volumill (NX plug-in milling application from Celeritive Technology).
Remember our original measures of cutting performance?
- The rate at which material is removed (also known as Material Removal Rate or MRR).
- The overall time required to perform the material removal.
- Tool life.
Both Trochoidal and Volumill reduce stress on cutting tools which increases tool life.They also allow for higher MRR, which means that jobs can be machined faster.
All of the tool path strategies discussed so far are great for removing large volumes of material, and in some cases finish-machining. In my next post, I will discuss how roughing operations work.