What is driving Digital Transformation today?
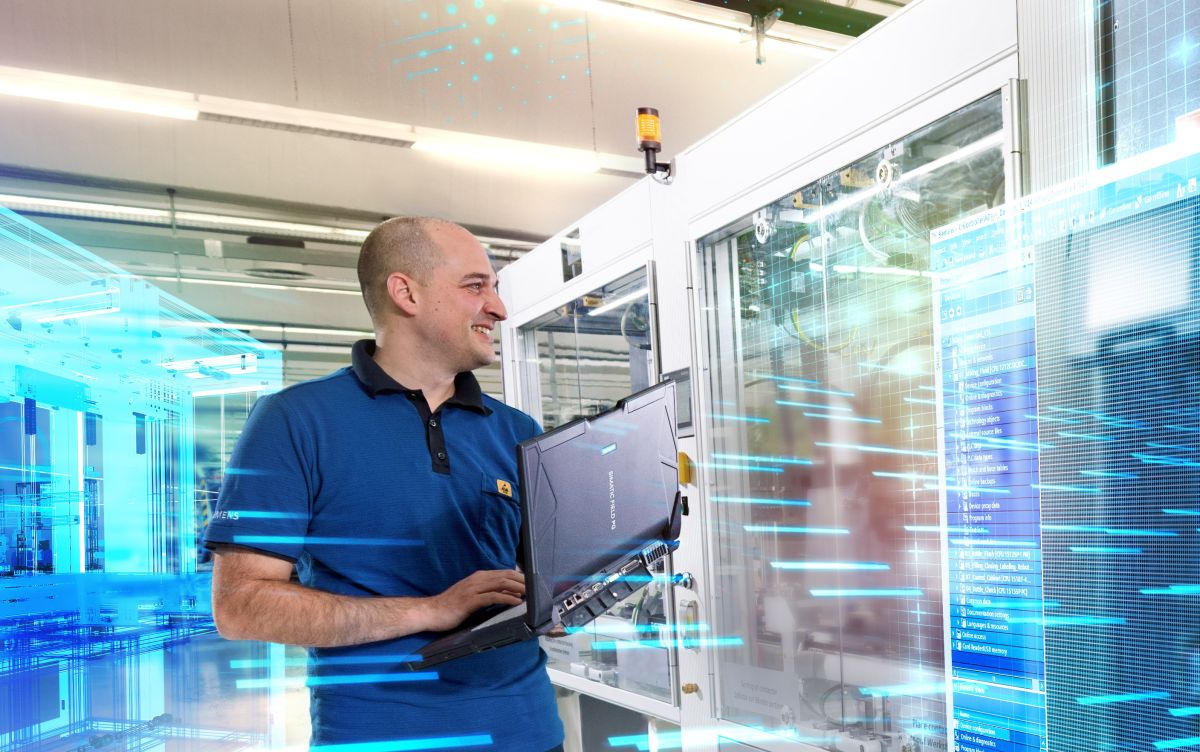
Multiple factors are driving today’s manufacturers to pursue different digital transformation (DX) initiatives. The current state of the U.S. economy and the increasing complexity of new products and production facilities have manufacturing organizations looking for new technology-led efforts to make improvements across the entire product development process.
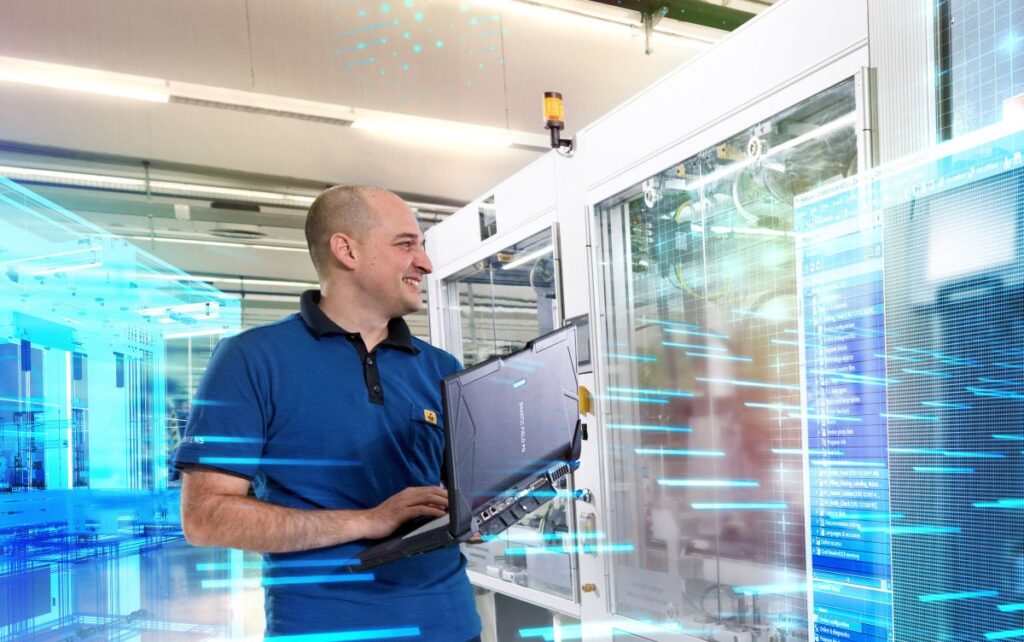
Introduction
The U.S. economy is undergoing a “seismic shift” with direct consequences to the manufacturing industry. The combination of growing consumer confidence and job gains in manufacturing sectors mean that the industry is poised for explosive growth. Today’s manufacturing organizations are looking for innovative ways to keep up and stay competitive.
Recent COVID-19-related business disruptions have accelerated digitalization across different industries and even brought such technologies into our day-to-day lives. The manufacturing sector is no different. In order to meet the moment and keep pace with new demands, many companies are looking at implementing digital transformation (DX) initiatives and other emerging manufacturing technologies.
This post is part of a series regarding new insights into DX initiatives in the manufacturing space. Be on the lookout for the next blog in the series.
The ROI of DX Study
To better understand how organizations are leveraging DX efforts, the research and industry analyst firm Lifecycle Insights conducted a research project called the 2021 Return on Investment (ROI) of Digital Transformation (DX) Study. The purpose of the study was to quantify the issues that were driving manufacturing organizations to pursue DX improvement initiatives. In addition, study participants were asked to assess the complexity of their internal products and development processes and consider how DX efforts might help streamline related workflows. Taken together, these metrics illuminate the trends currently driving DX initiatives and provide a deeper understanding of the ROI from such efforts.
While organizations are exploring DX initiatives to make improvements across the whole product development process, Lifecycle Insights’ 2021 ROI of DX Study examined product design, manufacturing, and service and operation areas. The survey was developed in October 2020, sent out to respondents in November 2020, and then analyzed in December 2020 and January 2021. The 343 survey respondents included design engineers, manufacturing engineers, and service planners, hailing from organizations headquartered in North America (57%), South America (19%), Africa (1%), Europe and the Middle East (16%), and Asia and the Pacific Region (8%).
Drivers of DX Initiatives
In the 2021 ROI of DX Study, survey respondents shared some of the most pressing issues leading to the increased adoption of new DX efforts. Those included expanding eco-friendly requirements, the growing consumer demand for smart, connected products, and the disruption of norms currently seen in traditional manufacturing processes.
Environmental policy
As public policy shifts to more aggressively address climate change both in the United States and abroad, today’s manufacturers must meet a host of new environmental regulations. The requirements associated with those new policies may vary between countries or locales, which presents a challenge for product development. Eco-friendly requirements also often come with a wide variety of incentives. Many organizations are looking to DX initiatives to manage emerging eco-friendly challenges and ensure they are recouping the related financial incentives for compliance.
Product complexity
The growing complexity of new products is also driving DX adoption. Today’s consumers want more than old-fashioned mechanical products from days of old. They are looking for smarter, more connected options. DX initiatives can help organizations manage design across multiple engineering domains, including electronics, electrical systems, and software development. They also permit more cohesive collaboration across the supply chain.
Organizational complexity
Finally, the COVID-19 pandemic changed the way that manufacturers traditionally do their work. Organizational complexity was already an issue for many companies even before anyone had heard of the novel coronavirus. Yet, as employees were sent home to meet social distancing and work-from-home mandates, manufacturing organizations had to find new ways to support collaboration and project management both within the company and outside of it—throughout the entire product development process.
These trends pushed manufacturers outside of their comfort zones. Traditional processes and workflows began to buckle under the weight of these new burdens. So, in order to address these new and compelling drivers for change, organizations had to look toward new, innovative technology-led improvement efforts like DX investments to expand their capabilities and stay competitive in the marketplace.
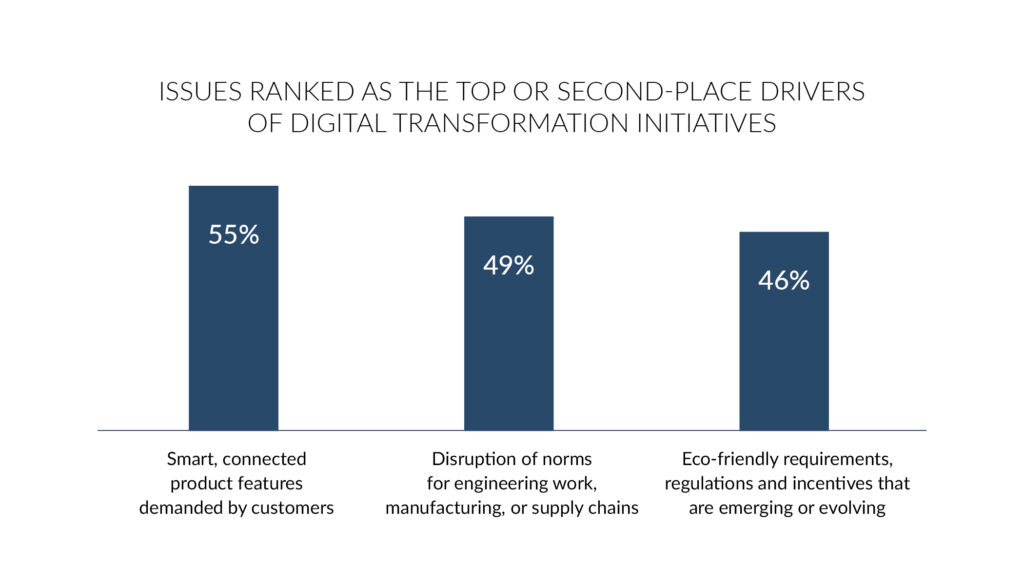
Rising Complexity in Manufacturing
The combination of new eco-friendly policies, consumer demand for more sophisticated products, and work disruptions have converged to make manufacturing, as a whole, more complicated. As products have become more complex, so has manufacturing (consider the emergence of smart manufacturing practices where streaming sensor data comes off the production systems themselves). As a result, many companies have struggled to keep up with requirements, not only with regards to product design workflows, but also while creating manufacturing and assembly processes. More complex products translate into more complex assembly which, in turn, results in the need for more complex production facilities. This growing complexity problem affects every aspect of the business, and manufacturers need additional support to manage the challenges that come with it.
The manufacturing industry does not exist in a vacuum. Within the context of recent business disruptions ranging from the COVID-19 pandemic to the blocking of the Suez Canal earlier this year, organizations need to be more agile to meet the moment. Once again, DX investments can help organizations pivot more easily when necessary, no matter what challenges they face. This sort of flexibility is invaluable from the earliest stage of product design to the development of the factory floor, and on through service and maintenance tasks.
When survey respondents in the Lifecycle Insights’ 2021 ROI of DX study were asked to pinpoint significant or overwhelming obstacles they were currently facing, 42% stated that product systems or line layouts were a challenge, followed by manufacturing cell layout and workflows (38%). Factory or facility layout (34%), machining toolpaths (32%), and tool design (26%) were also of concern, highlighting that complexity is not just limited to the products themselves. Manufacturing organizations are also looking for ways to develop manufacturing plans and deliverables more effectively.
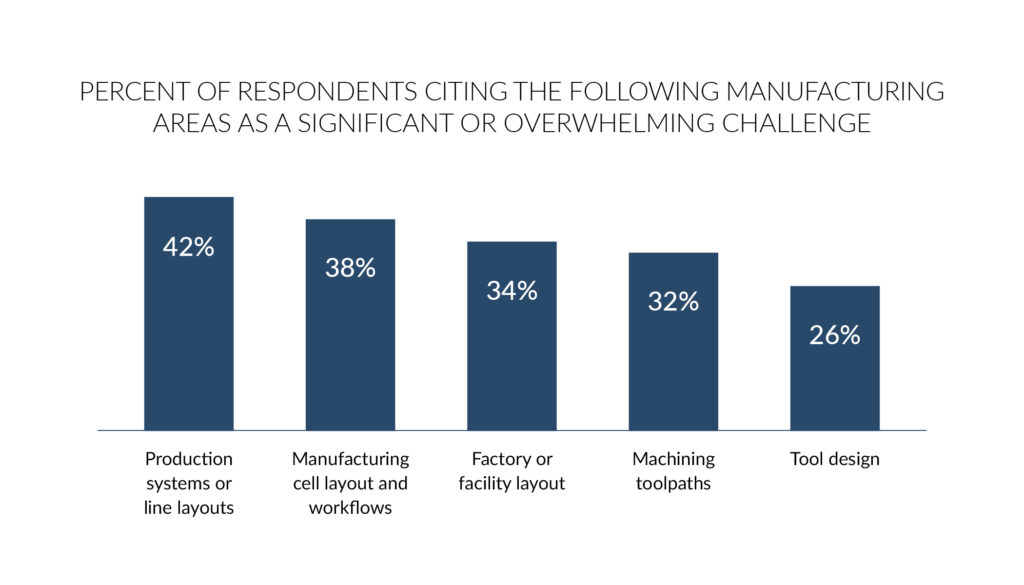
Pursuit of DX Initiatives
It is easy to see why so many organizations are pursuing different DX initiatives to address emerging trends—and to better manage compacted time schedules and limited resources in the process. Critical drivers including eco-friendly requirements, regulations, and incentives; growing demand for smart, connected products; and the continued disruption of product development norms have all pushed organizations to consider new technology-led improvement efforts. Furthermore, the growing complexity of both products and production facilities is also contributing to current DX investments.
Having the right technology solutions on hand can help organizations solve the many challenges they face in today’s market, whether it’s pivoting to manufacture a new, connected product according to specific eco-friendly guidelines or finding ways to support meaningful collaboration across the supply chain during a global pandemic.
It is probably not a surprise that Lifecycle Insights’ 2021 ROI of DX Study uncovered a high rate of DX activity over the past year. In fact, more than half of survey respondents (57%) stated they have completed some DX-related plans. Fifty-four percent are in the process of investing or assessing new DX initiatives. The adoption of DX initiatives is likely to continue well into the future.
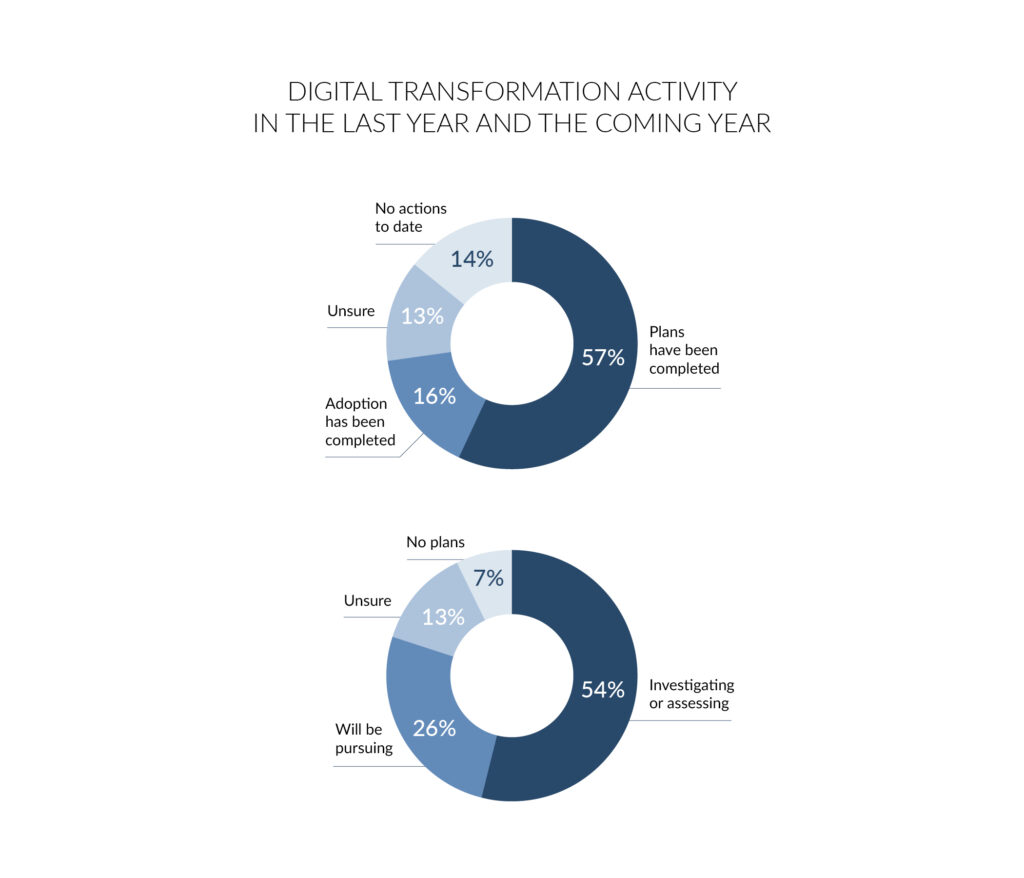
The survey results demonstrate a high rate of activity when it comes to DX initiatives in manufacturing, as well as some of the factors driving new investments. In the next two posts, we will discuss DX initiatives in part manufacturing and assembly and the ability of these initiatives to impact key performance indicators like manufacturing throughput and inventory. This can make or break a company’s bottom line.
Zvi Feuer is senior vice president of Digital Manufacturing Software Solutions for Siemens Digital Industries Software. Digital Manufacturing Software develops software products to deliver world-class solutions for Manufacturing (Part & Assembly) planning, simulation, and validation and Operations (MES, Scheduling, Quality and automation).
Read the second blog in the series, Increased throughput: A $7M opportunity for manufacturers.